物流現場の人手不足に備えるなら物流ロボットの導入など「作業者」の不足に対するものだけではなく、「管理者」の不足へも対策する必要があります。当コラムでは管理者が不足するとどういった課題が出てくるのか、どのような対策が考えられるのかについて、事例をまじえて解説します。
目次
コラムのポイント
- ・物流現場の管理者が不足した時の管理体制とその課題
- ・ホワイトボードによる情報共有を応用した解決策
- ・デジタル上のホワイトボードの画面イメージ
物流現場の人手不足にロボット活用では不十分?
物流を含む多くの現場で「人手不足の常態化」が懸念されています。
人手不足は一過性の現象ではなく「この状態が20年以上続く」と考えられているため、多くの企業が「将来への投資、リスク対策」として物流ロボットを活用し始めました。
しかしロボット活用だけでは不十分です。
ロボットは「作業者」の不足に備えた対策であり、「現場管理者」の不足には備えられていないためです。
手を動かすリソース(作業者やロボット)が充分だったとしても、管理者の不足がボトルネックとなって物流のQCDが低下する恐れがあります。
「人手不足の常態化」というピンチは、物流管理の在り方や手段を変革するチャンスでもあります。
当コラムでは、新しい物流現場管理の在り方とそれを実現するためのDX手法をご紹介していきます。
人手不足と物流ロボットの関係性に関する詳しい解説はこちら
物流現場管理者の不足がまねく課題
人手不足によって、物流現場の管理はどのような課題を抱えることになるのでしょうか。
現場管理者の役割を交えて解説します。なお当コラムでは物流センター長(倉庫の管理責任者)や各作業チームのリーダーを「物流現場管理者」としています。
物流現場管理者が不足した時の体制
物流現場の運用管理を行う人材が不足してくると、今までよりも少ない人数で現場を管理しなければいけません。
すると複数の業務を兼務する可能性が出てきます。センター長が複数倉庫の責任者を兼務したり、チームリーダーも複数の作業工程を管理したりするでしょう。そうなると管理者は担当する現場に留まっていることは難しく、問題が発生したり部下が判断を仰ぎたい時に「その場に居ない」ことが出てきます。
このような状態でQCDを維持・向上するには、どうすれば良いのでしょうか。
物流現場の管理者に期待される役割とQCDに関する解説はこちら
物流現場の管理品質を保つためには
より少ない人数でも今と同等以上の管理を行うには、2つの課題を解決する必要があります。
- ・離れた場所からでも現場の状況が分かる
- ・問題に対する具体的な指示やその後の経過観察が離れた場所からでもできる
大変難しいことのように思えますが、実は物流DXによって実現できます。
以下で実現方法やそのポイントを具体的にご紹介します。
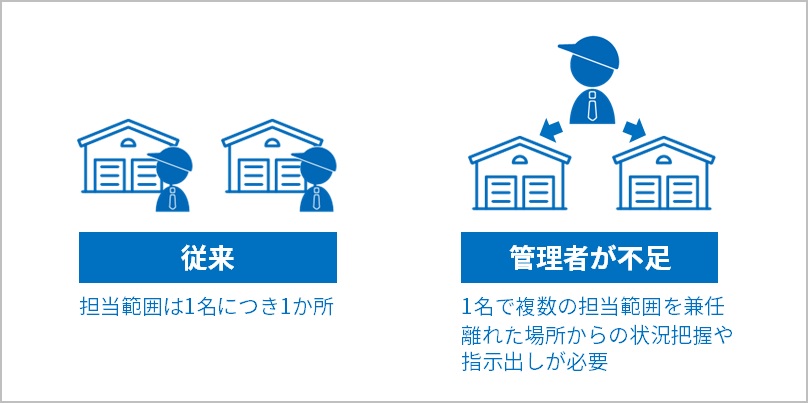
少数の管理者で物流現場を管理する方法
皆さんの物流現場には、作業の進捗状況や今日の作業量などをホワイトボードに掲示していることでしょう。
実はこの方法をさらに応用すれば、少ない人数でも今と同等以上の管理を行えるようになります。具体的には離れた場所からでも見られる「デジタル上」にホワイトボードを作り、運用管理に必要な情報をそこに集めてしまうのです。
デジタル上にホワイトボードを作るには
デジタル上にホワイトボードを作るには、以下3点を実現する必要があります。
物流現場の管理に必要な情報を全て可視化する
まず大前提として、物流現場の管理に必要なことは全て可視化しておく必要があります。
可視化とはデータで「見える」「計れる」状態にすることです。データを見る側にとってその立場を問わず誰でも物流現場の状態の良し悪しが適切に判断でき、人の勘や経験に依存しないようにしなければなりません。
しかし中には可視化されていない情報もあるはずです。例えばハンディーターミナルを使用しない作業の進捗状況は「現場で指示書を数える」などアナログな方法でチェックしていないでしょうか。そのような場合はカメラやセンサーなどのIoT技術を活用して可視化しておきましょう。この取組みはデジタルホワイトボードの実現だけでなく、物流DXの推進、データを活用した改善活動の促進にもなります。
なお可視化すると良い情報は当コラムの第4章「離れた場所からの現場管理に必要な2つの機能」で紹介しています。
可視化した情報を統合する
現場の様子を可視化したら、次は情報統合です。
情報統合とは、複数のシステムからデータを集約することです。例えば在庫計画に関する情報は生産管理システム、倉庫内のピッキング作業の進捗状況はWMS(倉庫管理システム)、トラック輸送に関する情報はTMS(輸配送管理システム)、といった具合に物流情報はいくつものシステムに点在しています。それぞれに個別に探しに行くよりホワイトボード1か所に集めておいた方が、より素早く状況把握できます。
離れた場所からでも管理可能な環境の構築
デジタル上のホワイトボードで現場状況を把握する場合でも、現場の人が見られるものと同じ情報をリアルタイムに取得する必要があります。また大前提として情報は正しくなければいけません。
情報のリアルタイム性と正確性を確保するには、単に情報を集約するだけではなく取得した情報を送信するためのIoT機器や通信技術といった先端技術が必要不可欠です。デジタルホワイトボードは、近年めまぐるしく進歩している先端技術によって実現できるようになったと言えます。
ご紹介した3点(可視化、情報統合、環境構築)は離れた場所からの運用管理を実現するだけではなく、ロジスティクス全体の最適化にも適用できます。
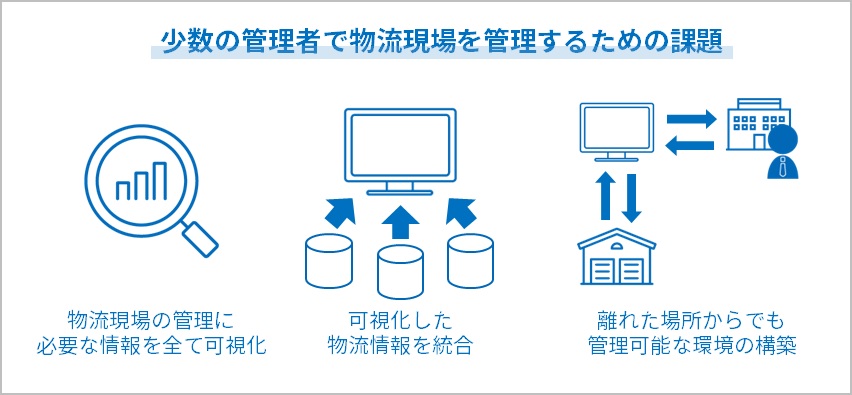
離れた場所からの現場管理に必要な2つの機能
デジタル上のホワイトボードを活用して離れた場所から物流現場を管理するには、大きく2つの機能が必要です。
物流現場の状況をリアルタイムに可視化
1つ目は、作業進捗など物流現場の状況をリアルタイムに可視化するための機能です。
必要となる情報は大きく4種類あります。
- ・物流業務に関するリアルタイムな情報
倉庫の作業進捗、トラックバースの予約状況、商品の輸送状況、在庫量など
物流業務に関する情報全般を各管理システムから集約 - ・物流ロボットの稼働状況
倉庫で稼働している物流ロボットのリアルタイムな稼働状況、過去実績、エラー情報など - ・物流コスト・KPIに関する情報
算出した物流コストや収支、KPIに関する数値など定期的に計測している数値情報 - ・監視カメラの映像
倉庫に設置された監視カメラの映像
画像もデータの1つであり、現場の様子が見て取れる貴重な情報
コミュニケーションもホワイトボード上で
もう1つはコミュニケーション機能です。
物流現場でよく発生する「突発的に入るイレギュラーな作業依頼」への対応方法を指示するのに使用します。
トラブルに対するリカバリー策の指示や、指示した後の進捗管理にもこの機能を活用します。
物流現場での作業は毎日少しずつ違うため、報告・連絡・相談が頻繁に発生します。営業部門や本社物流部などから依頼や問合せもよく入ってきます。現場にいれば電話をしているのに気づき「今の電話、誰から(どのような依頼・相談)だった?」と確認できますし、部下からも報告しやすいでしょう。しかし現場にいないとそうはいきません。離れた場所から管理するからこそ、コミュニケーションも作業進捗と同じように可視化しておくことが大切になってきます。
物流情報を可視化・統合する際のポイント
では実際、どのように可視化・統合すれば良いのでしょうか。
デジタル上のホワイトボードで情報を可視化・統合する方法やそのポイントをご紹介します。
情報は「一目瞭然」の状態に加工
1つ目のポイントは、情報を「一目瞭然」の状態に加工することです。
WMSなどで管理されている情報をヒストグラム、線グラフ、円グラフ、ヒートマップ、地図などに図解して表示します。ホワイトボードに数値をそのまま表示するだけでも情報を探す手間を無くせますが、図解することで現場管理者が情報を読み解く時間を短縮、よりスピーディーな状況把握と判断を支援します。
複数の情報を並べて可視化
2つ目のポイントは、一画面で複数の情報が見られるようにすることです。
作業の進捗状況、実際の現場の様子(監視カメラの映像)、イレギュラーな作業依頼に関するやりとり(コミュニケーション)といった情報を同一画面上に配置します。ホワイトボード上で一元管理するだけではなく表示も同一画面上にまとめてしまうことで、管理者が情報を探したり複数個所を参照したりする手間を限りなく減らします。
イレギュラーな依頼は一覧化・紐づけて可視化
イレギュラーな作業依頼を可視化する際のポイントは2つあります。
1つ目のポイントは一覧化することです。
依頼を一覧化することで五月雨式に来る依頼を抜け漏れなく管理できます。
「今日対応が必要なもの」など選別と優先順位付けがしやすくなるほか、関係者で共有することも可能です。
2つ目のポイントは依頼に対するコミュニケーション内容と進捗状況を紐づけて管理することです。
現場管理者は問題の発生から状況確認、完了までを一元的に管理できるようになります。
この改善は離れている場所から指示する時はもちろん、現場にいても役に立ちます。
物流現場では複数のプレイヤーが協力し合って作業しています。例えば緊急出荷したいなら、ピッキングチームだけでなく梱包チームにも依頼しますし、事務員へ在庫数の確認を依頼することもあります。コミュニケーションと依頼が紐づいていれば「詳しくはこのチャットに書かれています」と伝えるだけで済み、伝言間違いも発生しません。
「物流現場の可視化」というと作業進捗などが注目されがちですが、コミュニケーションの可視化は意外と重要です。
ここまでデジタル上のホワイトボードを活用する有効性をお話ししてきましたが、新しい取組みのため想像しづらいかもしれません。
そこで活用事例をご紹介します。
今回紹介するのは、倉庫業を営むA社でデジタルホワイトボードの効果検証を行った際の効果です。デジタル上のホワイトボードを活用した改善事例
デジタルホワイトボードの活用目的
同社はデジタルホワイトボードを活用することで3つの課題改善を目指しました。
デジタルホワイトボードに表示する情報と活用効果
A社では当社の倉庫管理システム「SLIMS」を活用いただいています。
SLIMSとデジタルホワイトボードを連携させることで、倉庫業務の進捗状況を可視化しました。
また今回は取組みのスピード感を重視し、対象作業を出荷工程におけるピッキング作業と検品作業に絞って検証しています。約2か月間、A社からの要望に応じた表示の修正と現場での試使用を繰り返し、本番運用を開始ししました。
作業の進捗状況
デジタルホワイトボードに表示する情報は、現場管理者が作業進捗を確認する際にチェックしている内容をもとにしています。作業進捗は運送事業者(便)ごとに各作業の未完了件数や進捗率、完了見込み時刻などを表示しています。
デジタルホワイトボードは現場にも設置
A社では実際にピッキングや検品作業が行われている現場に大型モニタを設置し、作業員も進捗状況を確認できるようにしています。従来は倉庫管理者が1日に何度もWMSへアクセスして作業進捗を確認し、作業者に情報共有していました。
現在は管理者も作業者もデジタルホワイトボードを見て進捗状況を確認しています。管理者が現場を離れてWMSの情報を見に行ったり、作業者へ共有したりする必要はなく、管理者の手間を軽減できました。
作業者の意外な変化
デジタルホワイトボードを現場に設置することで、作業者の意識も変わりました。
- ・作業現場にリアルタイムな進捗状況が表示される事で、作業者が進捗状況を意識しながら作業を行うようになった
- ・管理者からの指示内容にも理解が生まれスムーズに指示が伝わるようになったことで
意思疎通にかかっていた時間が削減 - ・作業員から「サポートに行く必要はないか」との自主提案が出るようになった
デジタルホワイトボードの可能性
A社の検証では倉庫の作業進捗を対象にしましたが、輸配送の現場や物流部門の運営管理などにも活用できます。
倉庫から輸配送まで現場管理に必要な情報を手間なく「一目瞭然」の状態で得られることで、意思決定の標準化や迅速化、トラブルの未然防止、物流リソースの有効活用が可能になります。
セイノー情報サービスの物流可視化ソリューション「LOGISTICS・COCKPIT」
当社ではA社の検証をもとにした物流可視化ソリューション「LOGISTICS・COCKPIT(ロジスティクス・コックピット)」をリリースしています。今回紹介した機能のほかにも、在庫ヒートマップなど多くの機能を備えています。
ご興味のある方はぜひお問い合わせください。
まとめ
物流現場の管理者が不足すれば、1人で複数の倉庫や作業チームの管理を兼務する可能性があります。
そうなると担当する現場に留まることは難しく、離れた場所から管理を行わなければなりません。
そのような状況でも管理品質を維持・向上するには、2つの課題を解決する必要があります。
- ・離れた場所からでも現場の状況が分かる
- ・問題が発生し対応策を指示した場合、その後の状況管理が離れた場所からでも行える
様々なシステムに点在する物流情報や監視カメラの映像など、現場の運用管理に必要な情報を集め、一元的に閲覧できるようにするのです。このような改善は、管理者が現場にいる状況でも役に立ちます。スピーディーに状況の把握や指示出しができるようになるため、刻々と変化する物流現場において、よりスピーディーに問題へ対処できるようになります。
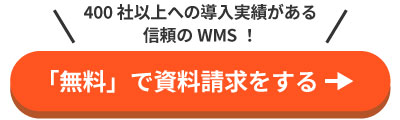