WMS(倉庫管理システム)とは
WMS(倉庫管理システム)とは
WMSとは倉庫管理システムのことでWarehouse Management Systemの頭文字をとった略称です。
従来の倉庫作業は手書きの台帳や表計算ソフトでも行うことができました。ところが量販店や一般消費者のニーズが多様化し、正確かつ迅速なモノの供給が求められるようになりました。「物流」を他社との差別化ポイントに位置づける企業も増え、倉庫管理の強化は必要不可欠の時代になりました。製造業に限らず流通業、小売業、通販業など幅広い業種で注目されています。
WMSは入荷・出荷・保管という倉庫内の業務について、バーコードリーダーなどを用いて作業の精度と効率化を支援する仕組みです。近年、物流の人手不足がクローズアップされており、作業進捗や生産性の可視化、物流ロボット・AI(人工知能)・センサーなどデジタル技術の活用がキーポイントに挙げられます。
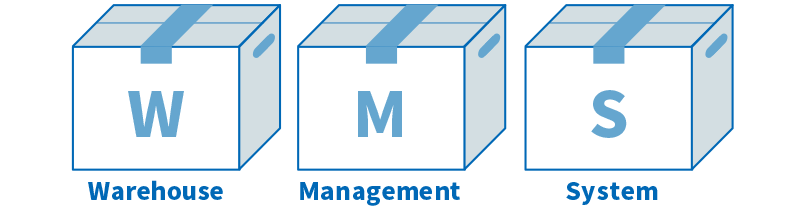
WMSの基本機能
WMSは倉庫内作業の精度向上、効率化を支援するシステムです。
大きくは入荷管理・出荷管理・在庫管理・進捗管理という4つの機能があります。現在はバーコードリーダーの活用が主流ですが、今後はカメラやAIなどデジタル技術の可能性に期待が高まっています。
入荷管理機能
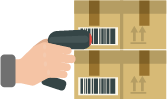
倉庫に入ってきたモノを検品し、所定のロケーションへ保管する作業を支援します。
入荷は倉庫作業の最初の要です。入荷の時点で予定との差異や期限など基本的なチェックを行い、ロット情報を収集することで多様な出荷ニーズに対応することができます。なお、バーコードがない場合はこの時点でラベルを印刷して貼付する必要があります。作業者を迷わせないように推奨の保管先(ロケーション)を指示するなどWMSには便利な機能も充実しています。
出荷管理機能
出荷の依頼に従って、所定の場所からモノを取り出し、決められたルールに従って梱包・出荷する作業を支援します。
先入先出(さきいれさきだし)、期限・ロット管理、ラベル貼付、納品書など、届け先によっては様々なルールが取り決められており、それが正しく行われるようにWMSで制御します。出荷は倉庫作業で一番の効率化ポイントでもあり、作業効率を高めるためにオーダーピッキング方式、トータルピッキング方式など作業方法も柔軟にコントロールできます。
在庫管理機能
何が、どこに、どれだけ保管されているかといった基本情報と、荷姿や期限・ロットなどの詳細な情報を一元管理します。
近年はクロスドッキング(入荷即出荷)など作業スピードが要求されており、そのためには在庫情報もリアルタイムでより詳細な内容が求められています。
進捗管理機能
WMSを導入する上で重要なポイントとなる機能です。
人手不足時代の倉庫作業においては、さまざまな切り口で作業状況を可視化することが何よりも重要です。一言に「出荷作業状況」といっても、フロア別、作業チーム別、得意先別、運送会社別などいろいろな切り口があります。見たい情報を早く見やすく可視化することが生産性の向上につながります。
他システムとの違い
物流や在庫を管理するシステムはWMSだけではありません。
基幹システムや在庫管理システムはWMSと似通った機能を持ち、TMSなど倉庫以外で使用されるシステムもあります。それらとWMSとの違いを解説します。
基幹システムとの違い
企業は基幹システムを導入していますが、なぜ基幹システムで倉庫業務も管理しないのでしょうか。
それは管理対象と目的が異なるからです。基幹システムは企業が事業活動をするために必要な情報全般を管理します。販売管理・生産管理・財務会計・人事給与などで構成され、ヒト・モノ・カネを有効活用し業務を効率化するためのシステムです。モノの流れ(物流)を管理するWMSと比べ、基幹システムはお金の流れ(商流)に重点を置いているため情報の内容やリアルタイム性に大きな違いがあります。
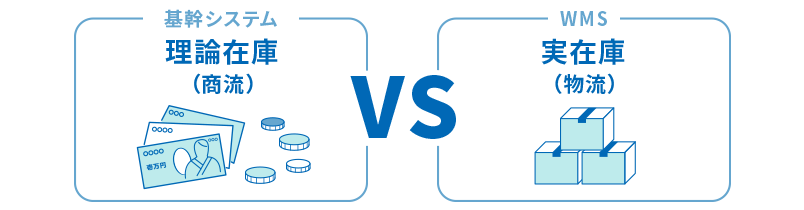
管理項目の違い
管理項目 | 基幹システム | WMS(倉庫管理システム) |
---|---|---|
商品管理 | ・仕入単価、金額 ・売上単価、金額 |
・商品サイズ、重量(バラ) ・荷姿サイズ、重量(梱、ケース) |
在庫管理 | ・全社在庫(製品在庫、商品在庫) ・拠点内在庫 ・固定ロケーション ・ロット管理 |
・製造ロット ・保管ロケーション (固定/フリーロケーション、複数ロケーション管理) ・ロケーション移動(補充) |
受注・出荷管理 | ・未来出荷分も含めて日単位管理 ・引当順(得意先別優先順、受注順=顧客) |
・当日処理分のみを時間単位に管理(作業進捗) ・引当順ロケーション単位の先入先出、ロット逆転不可/同一ロット、ロット指定 |
顧客管理 | ・請求先 ・与信、回収管理 |
・出荷先(納品先) ・納品条件管理、所在地管理 |
更新タイミング | ・取引先伝票処理単位で更新 ・日次単位:仕入計上日、売上計上日 |
・物の動きに連動してリアルタイムに増減 ・時間単位:入荷、格納、出庫、出荷時間 |
基幹システムに物流機能をアドオン開発している企業もみられます。決して間違いではありませんが、商流に比べ物流の変化はスピードが速く頻度も高いという特性があります。その都度システム修正にかかるコストを考えると、本来はシステムを分けるべきでしょう。
基幹システムとWMSの違いを解説する小冊子『商物分離実践講座』
ダウンロードのお申し込みはこちら
在庫管理システムとの違い
在庫管理は倉庫管理と混同する場合がありますが実際は異なります。
WMSの在庫管理機能は「倉庫内の在庫」に限定されますが、在庫管理システムは自社の倉庫以外の在庫も管理対象とします。在庫管理システムは基幹システムの一部分という見方が強く、商流視点での在庫管理に重きをおきます。対してWMSはいかに効率的に作業を遂行するかを追求したシステムです。当然在庫管理システムにはピッキング方式の選択や進捗管理という観点はありません。
TMSとの違い
TMS(Transport Management System)とは輸配送管理システムのことです。
WMSが倉庫内の業務を対象としている反面、TMSはトラックの配車を中心に輸配送の進捗管理を目的としています。TMSを導入することで、積載率の向上や配車業務が標準化され、輸配送状況が可視化されます。そしてWMSとTMSを連動することで、モノの入荷~配達までを一気通貫で管理することができます。
WMSを導入するメリット
WMSを導入するメリットはどのようなものがあるのでしょうか。
400社以上への導入実績をもとに、主なメリット4つについて解説します。
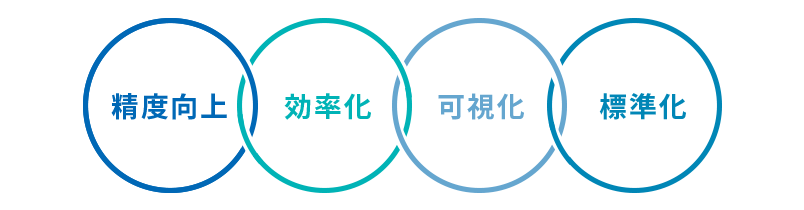
ミスを減らし精度を向上
出荷作業だけでも、モノのチェックに始まりロケーション・数量・期限など、倉庫内ではさまざまなチェックが発生します。それを全て目視で行っていると必ず間違いが発生します。WMSは、先入先出や期限など届け先によって決められるルールを踏まえ最適な出荷指示を出します。バーコードリーダーも活用することで、目視検品と比較して飛躍的な精度の向上が図れます。ベテラン作業員の業務知識に依存することなく、均一の作業精度を維持することができます。
作業効率のアップ
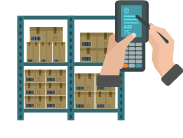
ある統計調査では、倉庫内の作業時間で一番多いのは「歩行」と言われています。WMSは歩行時間を減らすための工夫が盛り込まれています。ピッキング方式の選定もその一つです。トータルピッキング・オーダーピッキング・マルチピッキングなど、特性を踏まえて柔軟にピッキング方式を選定でき、歩く時間やチェックする時間をトコトン削減します。探す手間や同じことを繰り返す手間(伝票作成など)も大きく効率化します
誰でもできる作業現場へ
WMSを導入することで、倉庫・作業員ごとに異なっていた作業手順が標準化されます。他社との差別化を狙うあまり、出荷・梱包作業は届け先固有のルールが増加し、ベテラン作業員に依存することが多くなります。WMSだけで解決することではありませんが、WMSの導入に合わせて業務を見直すことで、ベテランでも新入社員でも誰でもできる作業現場となります。
リアルタイムに進捗状況を可視化
バーコードリーダーを活用することで、各作業の進捗や在庫情報がリアルタイムに可視化されます。遅延を察知し早期にリカバリーすることで、トラブルの未然防止も可能となります。パソコンやスマホに状況を表示すれば、管理者が会議室や出張先にいてもまるで現場にいるかのように状況が把握でき、具体的な指示が出せるようになります。営業部門や届け先からの問い合わせにも迅速に回答することで満足度も上昇します。
WMSを導入するデメリット
一方、デメリットもゼロではありません。
基幹システムにも改修が必要
WMSを導入する場合、多くは基幹システムとのデータ連携が必要です。入荷予定・出荷依頼の受取や、逆に基幹システムへ入出荷実績や在庫情報を送り込むこともあります。基幹システムとWMSを連携するには、両者にシステム改修コストが発生します。情報システム部門や基幹システムベンダーと密なコミュニケーションが肝要です。
操作説明や一定の慣れが必要
WMSに限らず新システムの導入直後は操作ミスや残業が発生する場合があります。これを防ぐためには操作説明や教育を入念にする必要があります。業務設計書やマニュアルを準備し、説明会やリハーサルを行うことで回避することができます。
WMS導入事例
WMSを導入すると現場はどのように変化し、どんな効果が得られるのでしょうか。
導入事例をもとにご紹介します。
丸栄ニューウェーブ株式会社
- お客様の概要
- 丸栄工業グループの自動車部品物流を一手に担い、トヨタグループを中心に取引しています。ベテラン作業員に頼ってアナログな運用をしていましたが、外販ビジネスの拡販と効率性の高い「かんばん方式」を高度化するためにWMSを導入しました。
- 業務の変化
-
- ・目視に頼ったかんばん照合をバーコードリーダーとQRコードを活用したオペレーションへシフトチェンジ
- ・入荷検品の際、当日出荷品はバーコードリーダーで判別できるようWMSで制御し作業員同士の口頭伝達を廃止
- 効果
-
- ・年間1~3件の誤出荷を撲滅!(ゼロ件)
- ・目視での作業や口頭での指示が廃止され在庫精度が向上
- ・バーコードリーダーの活用と業務の標準化で生産性が24%向上
TONE株式会社
- お客様の概要
- 総合工具メーカーのTONE様は、鉄骨のボルト締めに使うシヤーレンチで世界トップシェアを誇ります。工具卸やホームセンターなどから多品種少量の出荷が急増し、即納体制と品質を維持するためにWMSを導入しました。
- 業務の変化
-
- ・WMS導入と同時に業務プロセスを再構築し、バーコードリーダーを多用したオペレーションを確立
- ・物流センター新設に際し作業員を新規雇用。包装・出荷工程の複雑な作業をWMSで標準S化し増員なしで立上げ
- 効果
-
- ・導入前は20時頃に作業を終えることもあったが、WMS導入後は定時(17時)に終了
- ・出荷量の増加にも関わらず、従来と同じ人員で対応(本来なら2名増員が必要)
- ・バーコード検品により月間50件弱あった誤出荷を10件未満(誤出荷率0.02%)に削減
株式会社にんべん
- お客様の概要
- 元禄十二年創業。300年以上にわたり、鰹節やつゆ、調味料の製造を中心に日本の食文化を支える企業です。物流事業者に任せきりの現場運用を脱却し、作業品質の向上とトレーサビリティの強化を目的にWMSを導入しました。
- 業務の変化
-
- ・賞味期限を含む在庫情報をリアルタイムに可視化したことで、問い合せにスムーズに回答
- ・基幹システムとWMSを連携することで、受注センターで行っていた出荷指示の手入力を廃止
- ・バーコードリーダーを活用した賞味期限管理により、目視検品やエクセルなどのアナログ作業を撤廃
- 効果
-
- ・営業部門や得意先からの問い合せに対応する時間を短縮(削減効果:166時間/年)
- ・出荷指示の手入力、伝票作成を廃止(削減効果;466時間/年)
- ・新人を採用すると一通りの作業ができるまでに約2カ月かかっていたが二週間で一人前に!
株式会社にんべん様のWMS導入事例はこちら
これからのWMSに求められること
世の中は日々刻々と変化しています。サプライチェーンにおいては供給能力が重要視され、物流で差がつく時代となりました。業務システムの1つでしかなかったWMSは大きく脚光を浴びています。物流を経営課題として取り上げる経営者も増えており、WMSに求められている役割も変わりつつあります。
業務改善から経営課題の改善へ
品質向上、効率化、標準化は不変なものですが、今後は「情報活用」や「収益性の向上」「継続性」への重要性が高まります。WMSに蓄積される情報を指標化(KPI)し、改善活動を数値で継続的に評価する時代です。
DX(デジタル変化)に対応
深刻な人手不足が進む物流業界では、ロボットやAIなどのデジタル技術を活用した変革が不可欠です。WMSがその変革の足かせになることは許されず、いかにDXに対応できるかが重要なWMSの選定ポイントです。
自動化設備を積極的に活用する場合の「システム連携イメージ」はこちら
改善に向けた業務設計が重要
物流課題はますます複雑化し、「WMSやロボットを導入すれば解決する」という単純なものではなくなりました。システムの導入には常に業務設計がつきまといます。自社の物流はどうあるべきか、物流で他社と差別化するためには何をすべきかを一緒になって真剣に考えられるパートナーが求められます。
セイノー情報サービスの「SLIMS」は、販売開始以来400社以上に導入実績があり、多くのお客様から支持されているWMSです。深刻化する物流業界の人手不足時代に向け、経営目線で解決策をご提案しWMSを軸に物流DXを推進します。