導入ソリューション
- 倉庫管理
- ロボットマネジメント
- 省人化・省力化で人手不足を解決
-
-
- 企業名
- スケーター株式会社
- カテゴリ
- 倉庫管理(WMS)、物流DX BRAIS
- 業種
- 製造業
- 売上高
- 158億36万円(令和6年2月決算) 事業内容 プラスチック家庭日用品、ファンシー雑貨の企画および販売
お客様の概要
スケーター株式会社様は、1938年に奈良県奈良市にて万年筆の製造・販売業として創業されました。その後、日本において核家族化が進んでいたことから家庭用品の需要が増えることを予測し、プラスチック家庭日用品の製造・販売をスタートされました。万年筆の製造で培ったインジェクション成型技術を活かした高品質なオリジナル商品の開発に取り組まれており、現在ではお弁当箱を中心に、コップや水筒、ステンレスボトルなどの家庭日用品やファンシー雑貨を取り扱っています。
スケーター様の特徴はキャラクタービジネスにあります。サンリオ、ジブリ、タカラトミー、ディズニー、ポケモンなど多様なキャラクターのライセンスを獲得しており、それらを多彩な日用品・雑貨へと具現化する商品開発力を強みとしています。近年は、テレビや映画のキャラクターだけでなく、SNS発信のものなどキャラクターが細分化されているため、最新のトレンドをいち早くキャッチし新たな商品として発信するなど、新製品の開発にも力を入れています。
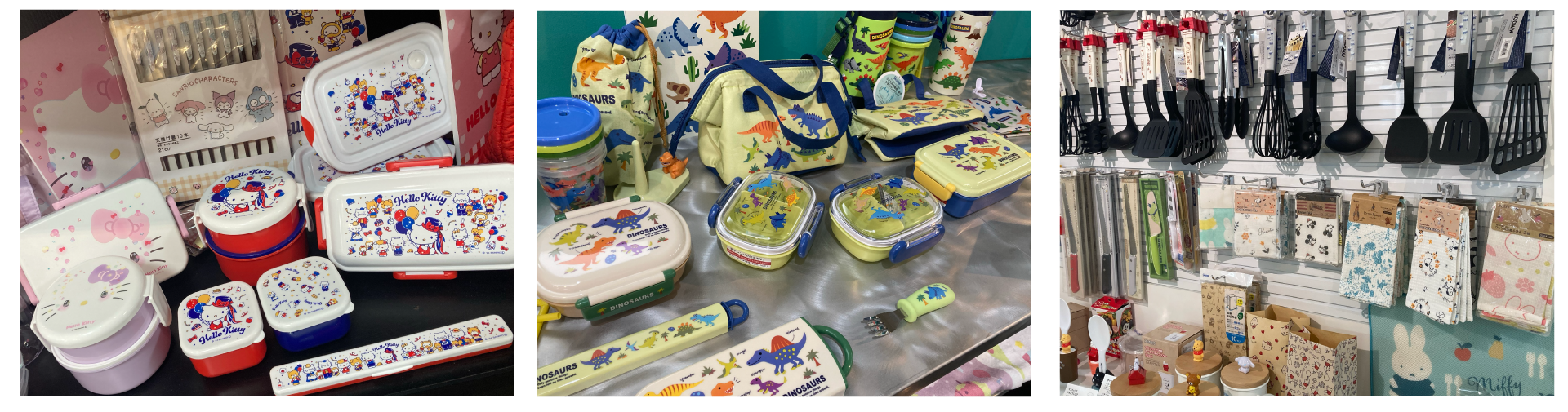
物流ロボット 導入のきっかけ
新たに設立した大和郡山物流センターは、西名阪自動車道郡山インターチェンジを降りて500mほどの場所に位置します。敷地面積は約4,700坪を誇り、約100名の従業員が業務に従事しています。
センター設立には「長く快適に働ける職場」をテーマに掲げ、特に「自動化」と「快適な職場環境」を意識されました。従業員に継続して働いてもらうため、倉庫内の空調や充実した休憩室、シャワールーム、駐車場など様々な設備が完備されています。そして、今後益々働き手の確保が難しくなることや人件費の高騰を見越して、自動倉庫や自動梱包機、ピッキングアシストロボットAMRを導入し、業務の省人化・効率化を図りました。
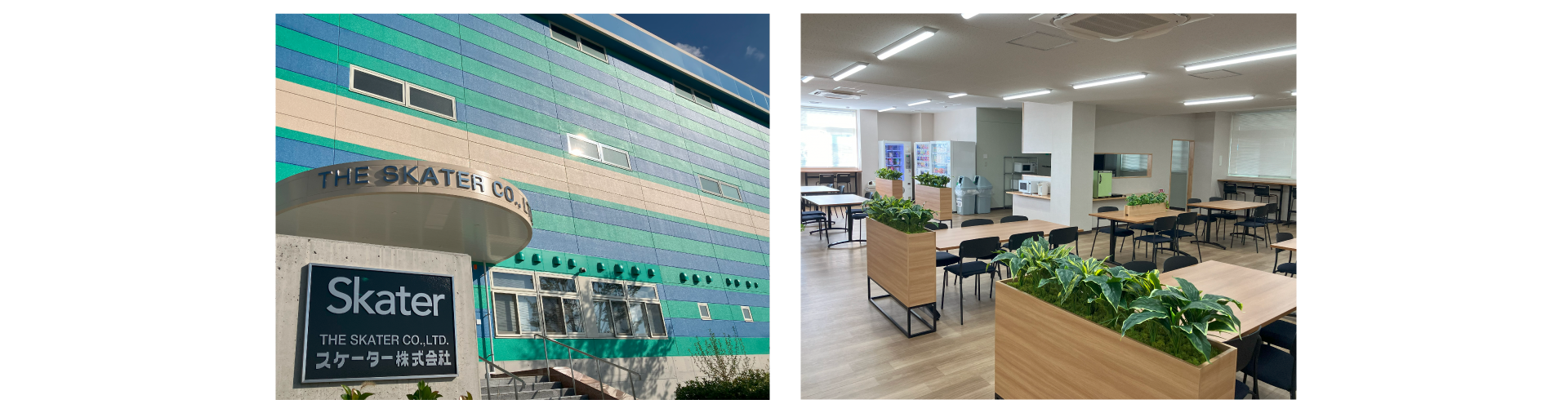
-
課題
- ・人手不足の対策として自動化設備を備えた物流センターを構築したい
- ・物流センターが広いため、ピッキングの歩行時間が長い
- ・出荷業務以外にもWMSを活用したい
-
成果
- ・歩行距離の削減により作業負荷が軽減
- ・出荷作業の生産性向上
- ・従業員の現場管理への意識向上
動画で見る|WMSと協働型ロボットの連携で倉庫内作業の生産性が向上
物流ロボットの選定
AMRが選ばれた理由
様々な物流ロボットの中でも、協働型ロボットであるAMRはスケーター様の運用の特徴であるシングルオーダーピッキングにピッタリと合うロボットで、すぐに活用イメージが持てました。検討の際にはラピュタ社のショールームで実際に作業を体験したり、AMRの簡易シミュレーションで導入後の費用対効果を算出したりすることで使用感や導入効果も感じることができました。
物流ロボットの導入には費用がかかるため社内で理解を得るのに苦労するのが一般的ですが、スケーター様は社長をはじめ会社全体が「新しいことへの挑戦」に前向きで、自動化への投資も積極的に検討されていたため、導入まで全社一丸となって進めることができました。
ピッキングアシストロボット ラピュタPA-AMRとは
ピッキングアシストロボット ラピュタPA-AMRは作業者と協働でピッキングします。障害物を検知しながら、1秒間に約1.4mの速度で移動し、積載可能な重量は45Kg、8時間の連続稼働が可能です。このAMRをコントロールしているのが、弊社のロボットマネジメントシステム RMSと倉庫管理システム(WMS) SLIMSです。特にRMSは多種多様なロボット・マテハンを制御でき、ベンダーやプロダクトは問いません。このRMSを活用することでスピーディーにAMRを導入することができます。
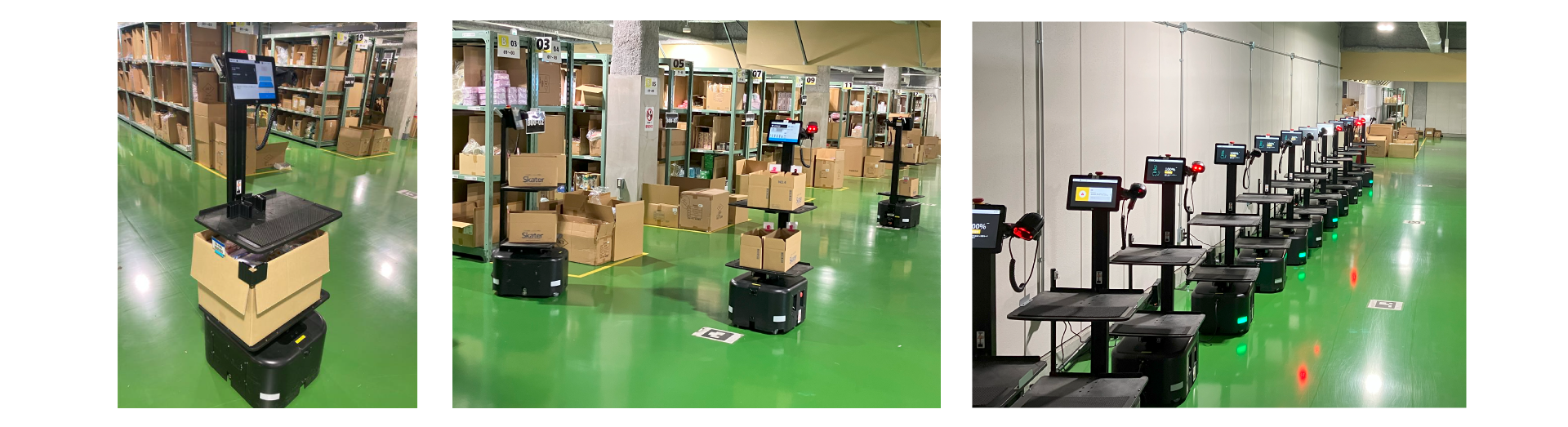
WMS「SLIMS」とAMRを活用した現場業務
管理者がSLIMSで出荷指示を行うと、AMRに出荷指示が届きます。作業者は指定されたサイズの箱に装着されたバーコードをAMRで読み取り、AMRに箱を設置したら画面を操作してピッキングスタートです。この箱にはサイズが4種類あり、事前に組み立ててバーコードのクリップを装着しています。
この時、AMRは届いた出荷指示から最短のピッキングルートをAIで分析し、床に貼られたコードをセンサーで読み取り位置を把握しながら所定のロケーションまで移動します。そのため、ピッキング作業者はピッキングルートを考える必要もなく、歩行距離も大幅に削減されます。
作業者は所定ロケーションで停止しているAMRを確認したら、画面に表示された商品を棚から取り、AMRで商品バーコードをスキャンし商品を箱に収めます。ピッキングが完了し画面の完了ボタンをタッチすると、AMRは次のロケーションへ移動していきます。
全ての商品のピッキングが完了すると、AMRは梱包エリアへ移動します。ここでは、梱包作業者が箱を下ろし画面の完了ボタンをタッチすると、AMRは待機エリアへ戻り次のピッキングに備えます。
そして梱包作業者がハンディターミナルでクリップのバーコードを読み込むと送り状が印刷され、それを箱に張り付けて梱包したら作業は完了です。
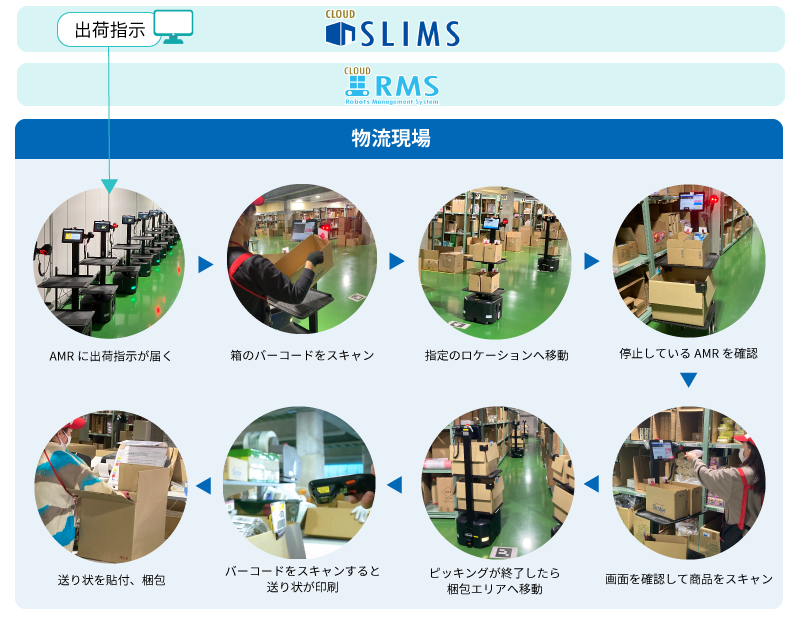
導入効果
協働型ロボット AMR の導入で出荷作業の生産性が向上
AMRでピッキングを行うことで歩行距離は大幅に削減されています。これにより出荷作業の生産性も向上しており、特にBtoBのような複数明細のオーダーにはAMRでのピッキングが適しており、大きな効果を発揮しています。
また、BtoCのような商品数の少ないオーダーなど柔軟に対応したいものにはハンディターミナルを使用した従来のピッキングも活用しており、実はここにもAMR導入の効果が現れています。それは、AMR導入を踏まえた新物流センターのロケーション配置にあります。
ここではフリーロケーションを採用しており、AMRと人が協働できるような広い通路の確保や、商品配置にも余裕を持たせています。また、棚だけでなく段や列にも番号も付けて細かく管理することで目視で商品を探す時間が大幅に削減され、生産性が約2倍に向上しています。
ロケーション管理は導入後も繰り返し改善活動を行っています。倉庫管理システム SLIMSの月間出荷数や在庫情報を参考に、頻繁に取りに行くロケーションの傾向を見て具体的な改善に繋げています。
従業員のスキル向上への意識が高まる
SLIMSの機能拡張、AMRの導入など先進的な技術の投入により従来の運用と大きく変化したことで、従業員の意識が格段に向上しました。ロボットやシステムに頼るだけでなく、より良い管理体制にしていくために、可視化された情報を様々な角度から検証し改善活動へ繋げています。
中でも、物流センター内の業務をSLIMSで一元管理したことで、今まで見えていなかった問題点も浮き彫りになっています。従来の物流センターではSLIMSを活用していたのは出荷業務のみであったため、出荷業務以外の工程では可視化されておらず、経験や勘での運用となっていました。しかし、SLIMSですべての工程が可視化されたことにより出荷業務だけでなく入荷や格納にも改善点があることに気が付き、さらには業務を1つ1つの工程で切り離すのではなく、一連の流れとして捉えた改善策を検討できています。「どこにどんな問題点があるのか」それに対して「どう対応することで改善するか」を常に考える環境に変化したことで、従業員の現場管理へのスキルも向上しています。
お客様の声
スケーター様の今後の展望
現在も品目数や出荷件数が増加しており、今後さらに拡大していきます。物流はバックアップ的な部門であるため、このような企業の変化、社会の変化に素早く対応していきたいと考えています。今回導入した倉庫管理システム SLIMSやロボットマネジメントシステム RMS、AMRは大きな効果を生んでいるため、これから更に効率的な運用を目指し、将来的には稼働台数の拡大も検討していきたいと考えています。また、現状を素早く把握するためにも情報の可視化は重要だと考えているため、物流現場の可視化 LOGISTICS・COCKPT にも非常に興味があります。今後も、ロボットやAIは急速に発展していくと考えられるため、更に活用していけたらと思っています。
セイノー情報サービスへの期待
セイノー情報サービス様には導入前も導入後の現在も様々な視点からのアドバイスをいただいており、いつも大きな気付きとなっています。これからも一緒になって改善活動に取り組んでいただけたらと思っておりますので、引き続きご支援よろしくお願い致します。
代表取締役 社長
鴻池 総一郎 氏