導入ソリューション
- 倉庫管理
-
-
- 企業名
- 丸栄ニューウェーブ株式会社
- カテゴリ
- 倉庫管理(WMS)
- 企業規模
- 約80名
- 業種
- 運輸・倉庫業
概要
丸栄ニューウェーブ株式会社様は、自動車部品メーカーである丸栄工業グループ各社やデンソー、アスモなどを取引先として、部品の取引・保管・配送などを行っております。本社である岡崎市内の物流センターの取扱量は、部品箱換算で月間15万箱に達します。 同社ではデンソー版のトヨタ生産方式「TIE(Total Industrial Engineering)や現場改善活動「EF(Efficient Factory)」を採り入れ、高品質な物流サービスの提供に力を入れています。かんばん方式によるジャストインタイムもその1つで、取引全体の60%がかんばん方式によるものです。 同社は、自動車業界に限らず様々な業種業態を対象に外販ビジネスを獲得に向けて、この効率性の高いかんばん方式をさらに高度化するための物流システムの品質向上を目指しました。
- 課題
- ・作業者のミスにより誤出荷が発生
- ・作業に手間がかかるため、誰でも確実に作業できる作業環境を整えたい
- 成果
- ・誤出荷がゼロに
- ・目視での作業や口頭での指示が廃止され、在庫精度が向上
- ・ピッキングからトラック出荷までのリードタイムが22%短縮
課題
グループ本社・丸栄工業の基幹システムと連携して出力される紙ベースの帳票類を元に、入出庫の作業を行っていました。
作業者によるミスの発生
入荷検品作業では、受入リストと部品箱の現品票の品番を目視で照合していたため、見落としの可能性があるだけでなく、作業者にも負担がかかっていました。 入荷検品後は、当日出荷とセンター保管に別れますが、この判断を担当者から口頭で伝えられていたため、聞き間違いも発生していました。 さらに、パレット単位で管理している1階では、部品箱を格納したらタグを外して管理版まで持っていく運用をしていました。この管理版には品番ごとにタグを入れるゲージがあり、格納するたびにタグが積みあがっていきます。ゲージの最下段のタグを抜いて該当のロケに行けば先入れ先出しが担保できるというものです。しかし、この運用には、タグの入れ忘れや入れ間違えのリスクがあり、ピッキング時に”あるべきものがない”という状況も発生しかねませんでした。
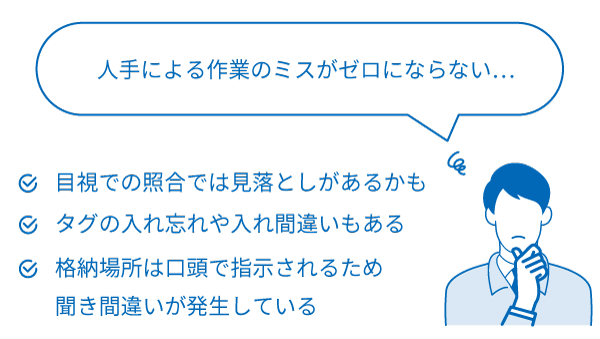
作業に手間がかかる
ピッキング作業では、紙のピッキングリストは1階、3階など保管場所の区別がなく、オーダー別で(納品先別)で出力されていました。そのため、作業者が1階と3階を行き来することが度々ありました。 また、進捗管理には「差立て表」と呼ばれるボードを使う独特の管理方法を行っていました。これは、出荷便が出発する時間軸に沿って、ピッキングを開始するたびに出荷伝票を抜いていきます。このボードは出荷エリアに設置されていたため、そこに見に行かないと状況が分かりませんでした。
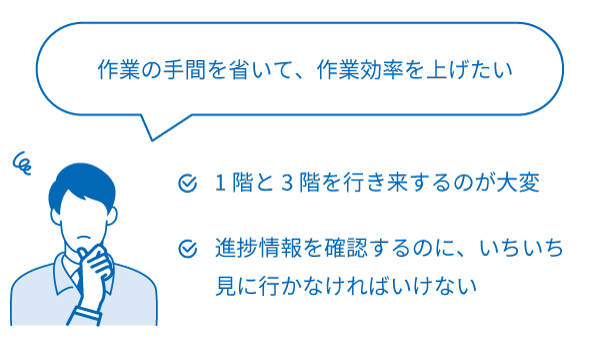
課題解決方法
入荷から出荷までの一連の作業をハンディターミナルで実施することで、各工程の作業が大きく改善されました。
入荷検品
部品は部品箱に入った状態で入荷されますが、ここにはかんばんとは別に現品票が貼付されています。このQRコードをハンディターミナルでスキャンして、品番や数量を確認するという、正確かつ簡単な作業となりました。 また、過去に間違って入荷された部品や類似品は、外見の画像を表示して注意を促しています。ここでポイントなのは、”すべての部品で画像を表示しないこと”です。やはり、作業者は、毎回表示されてしまうと次第に見なくなってしまいます。たまに出るから“気を付ける必要がある”と分かるのです。
格納
入荷検品後は、当日出荷とセンター保管に別れますが、この指示がハンディから出されるため、口頭での聞き間違いによるミスがなくなりました。 また、SLIMSで先入れ先出しを管理できるようになったことで、以前のように部品箱を格納したらタグを外して管理版まで持っていくという手間が省けました。さらには、タグの入れ忘れや入れ間違えなどのミスも起こらないため、在庫精度も向上したのです。
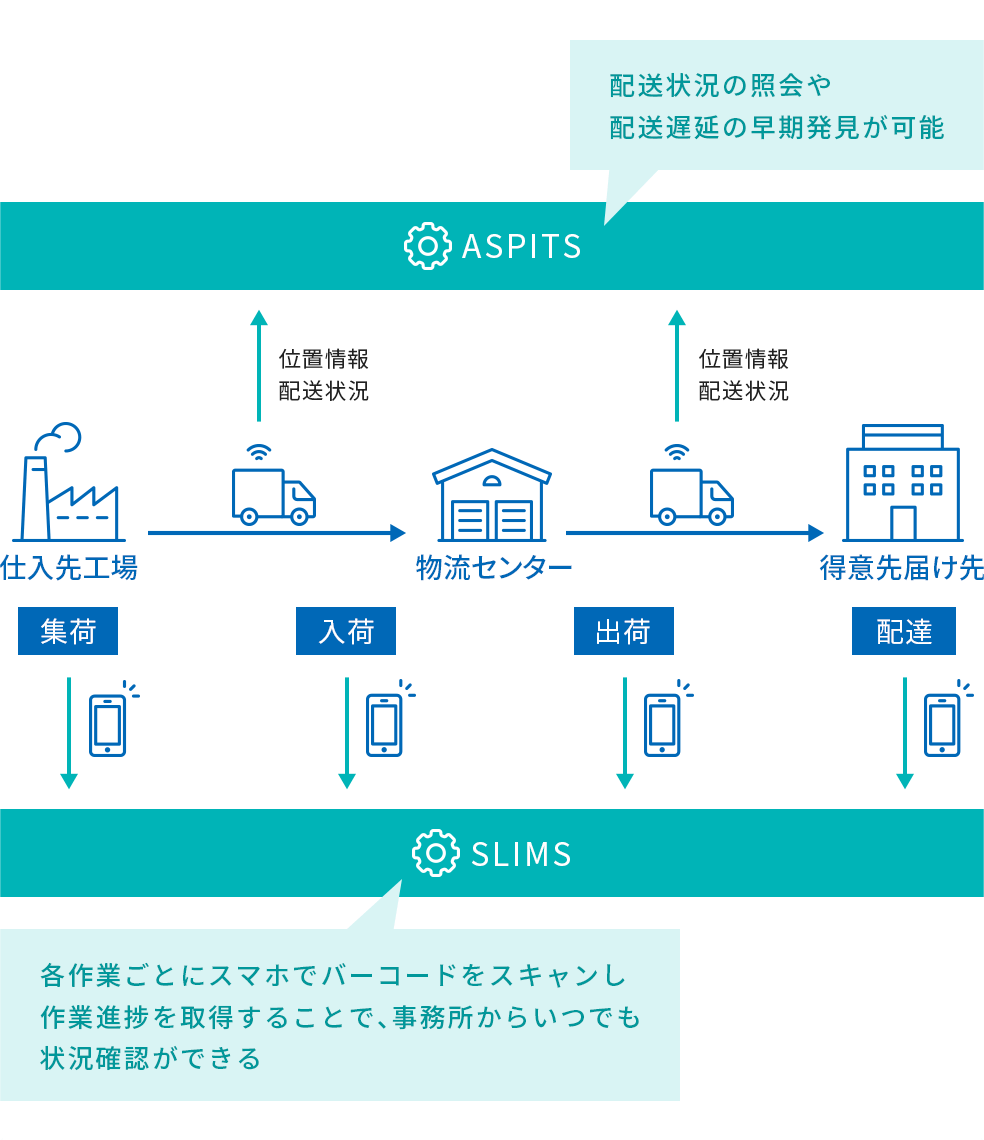
ピッキング
- 1. 得意先から受注が来ると、ピッキングを開始します。これはトラックが来る2時間前に作業を始める仕組みになっており、出荷指示ラベルが出力されます。
- 2. このラベルは1階、3階、当日出荷品の3種類あり、1階と3階のラベルはQRコードをハンディで読むことでピッキング作業を開始します。
- 3. ハンディにロケ番号が表示されるので、該当の場所まで移動、そこでロケのQRコードをスキャンします。場所が正しければ(ハンディが判定)部品箱のQRコードをスキャンしながら必要な数量をピッキングしていきます。
この作業を、SLIMSでは、保管場所別に作業バッチを組み、1階と3階に振り分けています。また、対象の部品の出荷待ち・格納待ちの状況も分かるようになりました。 進捗管理についても、PCの管理画面にピッキングの進捗がパーセンテージでリアルタイム表示されます。そのため、何らかの事情で作業が遅れていれば、管理者が応援に入る、あるいは要員を再配置するといった判断ができます。さらに、SLIMSはクラウド運用のため、PCやスマートデバイスでどこにいても確認可能となります。
出荷
1階3階でピッキングが終了したら、1階の荷揃え置き場まで運び、当日出荷品と荷合わせして出荷準備となります。ここではまず「かんばん照合」機能を使って、ピッキングした部品に付いていたかんばんと出荷用に使うかんばんを照らし合わせてピッキング内容をチェックします。これは2つのかんばんのQRコードを交互スキャンして相違がないかチェックし、出荷用のかんばんに付け替えていきます。 そこまで進めば最後の作業は積込検品となります。これは、3枚の出荷指示ラベル(1階3、階、当日出荷)をハンディでスキャンすると、SLIMSの在庫からピッキングした部品箱が除外されるのです。
導入の効果
-
01誤出荷の減少
人手による作業のミス、同社の出荷ミスは年間1件~3件程度と、月15万箱もの取扱いがあるにも関わらず、非常に少なかったのです。しかし、どうしてもゼロにはならなかったのが、今回の導入以降、「誤出荷はゼロ件」となりました。
-
02生産性が24%向上
様々な場面での確認時間の短縮により、導入前と比較して生産性がさらに24%向上しました。その他にも様々な効果を検証したところ、月刊100万円以上のコスト削減効果が出ています。
-
03作業者の負担軽減
元々ミスの発生が少ない環境だけに、ミスをした作業者は事態を深刻に受け止めて悩んでしまうことも多々ありました。しかし、今は手順を守って作業を進めれば誤出荷の心配はなく、作業者の精神的負担も軽くなりました。
-
04作業実績データの自動化
これまでは作業ごとに用紙で記入していましたが、各作業がハンディオペレーションになることで、作業実績が簡単に把握することができました。
お客様の声
今後、SLIMSの導入範囲を他の拠点に拡げ、グループ全体の在庫を可視化していく考えです。その点、クラウド型のSLIMSならば基本料金と出荷明細単位の従量課金で使用料を計算するので、導入範囲を広げれば広げるほど、出荷1単位当たりの基本料金負担も軽くなります。さらには、SLIMSは多言語対応なので、国内では日本語、海外では英語で表示するなどの切り替えも可能になるのです。
また、今回、ハンディオペレーションにより誰が作業しても同じレベルの物流サービスを提供できるようになりました。今後さらに作業を簡素化することで、正社員が行っていた作業をパートタイマーの方に任せるなど、雇用の多様化も見込めます。
さらには、今後、自動搬送機器などのマテハン設備の導入も視野に入れています。そのためにもWMSは必須であり、SLIMSにはまだまだ期待をしています。SLIMSの存在こそが、最終目的である「外販ビジネスの獲得」の大きな推進力になっていきそうです。