製造業にとって「モノづくり」は企業の価値そのものです。
市場が混迷を深め変化のスピードが増している今日、ヒト・モノ・カネといったリソースを「モノづくり」に集中させることは重要な経営課題の1つです。
しかし実際には、原材料の入荷や保管など「製造」以外の業務が工場内に存在しています。当コラムでは工場の業務そのものと、
モノの配置や動かし方を変えることで工場が「モノづくり」に集中できる環境を整える方法について解説します。
目次
-
- ・「モノづくり」にとって最適な環境とは
-
- ・工場のあるべき姿
- ・あるべき姿を実現するための2つの改善
-
- ・業務を細かく分解し工場で行うべきか検討
- ・在庫配置を見直して工場在庫を最小限に
4. 改善2. 生産計画をもとにしたJIT納品の仕組みを作る
- ・JIT納品を実現するコツは作業計画の連動
- ・門前倉庫を活用しJIT納品を実現しやすくする
6. まとめ
コラムのポイント
- ・今の時代に適した「工場のあるべき姿、役割」の一例を紹介
- ・実現するための改善手法を具体的に解説
「モノづくり」にリソースを集中させる時代
製造業にとって「モノづくり」は企業の価値そのものです。
競争が激しく、変化のスピードが速く先が見通しにくい今日では、ヒト・モノ・カネといったリソースを「モノづくり」に集中させることは、経営効率や業績を高め競合他社との競争に勝ち抜くために重要な経営課題となっています。
経済産業省が推奨するスマートファクトリー化は、製造業が自社の「モノづくり」に関する基盤を強化する方法の1つです。多くの企業が自社の生き残りをかけて戦略的に取り組んでいます。
「モノづくり」にとって最適な環境とは
まず考えられるのが、工場のリソースを「製造」に集中させることです。
ところが、工場で行われている業務の多くは「製造」に関連しますが、自社の強みに繋がることばかりではありません。
作業については、原材料の入荷チェックや製造ラインに投入する前の計量・検品など、実際の「製造」以外の作業に多くの時間を費やしています。
環境面については、円安の影響で原材料を一括購入したため工場内のスペースが圧迫されているなど、さまざまな要因が「製造」への集中を妨害しています。
工場の本来の役割は「製造」であり、企業価値を創造する製造工程にリソースを集中すべきです。そのためにも、工場の役割を見直し、工場が「モノづくり」に集中できる環境を整える必要があります。
今の時代に適した「工場のあるべき姿、役割」とは
工場のあるべき姿
以下の図は、工場のリソースを「製造」に集中させた「あるべき姿」の一例です。
- ・工場近隣に門前倉庫を運営
- ・原材料は門前倉庫で集約保管し、補充計画に従って工場へ出荷
- ・計量や配膳、簡易加工は倉庫で行い、工場は生産ラインへすぐ投入できる状態で受け取る
- ・各工場で作られたモノは倉庫に集められ、受注情報(出荷指示)に従って倉庫から顧客へ出荷
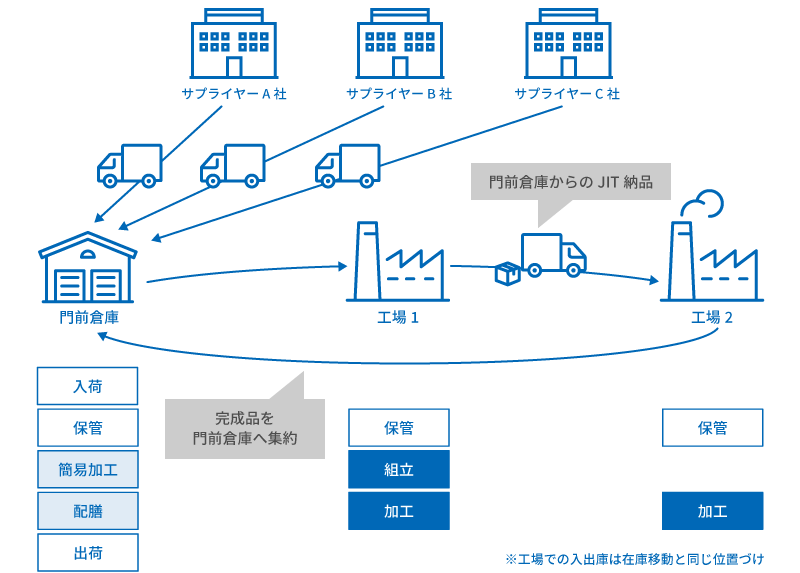
これは門前倉庫※を活用したJIT納品モデルです。
原材料の保管や配膳など、工場で行っていた業務の一部を倉庫に外出しすることで、工場業務が「製造」に集中できています。さらにモノの流れと在庫配置が整えられシンプルになっています。
※門前倉庫とは
工場近隣に設けられる倉庫のこと
一般的には、サプライヤーが納品リードタイムの短縮化を図るために顧客の工場近隣に倉庫を構える
あるべき姿を実現するための2つの改善
この門前倉庫モデルを実現するための2つの改善をご紹介します。
改善1. 工場の業務と在庫配置を見直す
工場の業務そのものと在庫配置を見直し、工場のリソースを「製造」に集中させます。
- ・工場の業務を細かく分解し、本当に工場で行うべきか検討
- ・BCPの観点、納品リードタイム、生産計画を踏まえ、工場で持つべき在庫量を明確化
※BCPとは
Business Continuity Planの略称で「事業継続計画」のこと
緊急事態が発生した際に、企業が事業を継続したり、迅速な復旧を行ったりするために必要な方針・体制・手順などを定めたもの
改善2. 生産計画をもとにJIT納品の仕組みを作る
生産計画をもとに、製造前のあらゆる業務を計画することでJIT納品を実現します。
- ・製造前の業務が生産計画に最適なタイミングで行われるよう計画
- ・門前倉庫を活用し、JIT納品を実現しやすい仕組みへ変革
JIT納品モデルの詳細はこちら(第2話)
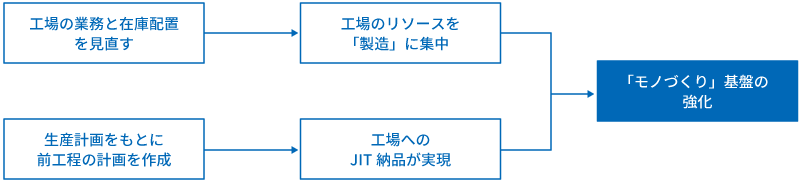
どのようにこれらの改善を行うのか、そしてどのような効果が得られるのか、以下で詳しく解説します。
改善1. 工場の業務と在庫配置を見直す
工場の業務そのものと在庫配置を見直して、人・モノ・スペースなどの工場リソースを「製造」に集中させます。
業務を細かく分解し工場で行うべきか検討
工場の業務を細かく分解し、1業務ずつ本当に工場で行うべきか検討します。
まず誰にでもできる、自社の強みに直接繋がらないようなノンコア業務は門前倉庫へ移管し、工場で行うべき業務を絞りこみます。
計量や配膳など製造前の業務を門前倉庫で行えば、ノンコア業務に従事していた作業者を「製造」業務へ再配置することも可能です。
工場に残すノンコア業務は最新のデジタル技術を活用し、省人化・省力化します。保管・搬送などの構内物流はその最たる例です。自動倉庫や搬送用ロボットを活用することで、構内物流にかかる人的リソースを最小化します。
在庫配置を見直して工場在庫を最小限に
BCPの観点や納品リードタイム、生産計画を踏まえ、各工場で持つべき在庫量を明確化します。 そして余剰の在庫は門前倉庫など別の拠点で集約保管します。在庫配置を見直すことで各工場の在庫量と保管スペースを最適化します。「安全在庫」も少なくて済むため、全社的に在庫削減が進みます。
加えて、在庫配置を見直すことでモノの移動がシンプルになります。
通常、各工場への原材料の納品は複数のサプライヤーから五月雨式に行われています。在庫を門前倉庫に配置換えすることで、必要なモノが門前倉庫からまとめて納品されるようになります。
工場での入荷業務が楽になると同時に輸送効率が改善しCO2排出量も削減できます。
改善2. 生産計画をもとにしたJIT納品の仕組みを作る
工場では必要最小限の在庫だけを持ち、門前倉庫から各工場へ原材料がJIT納品される仕組みを作ります。
JIT納品を実現するコツは作業計画の連動
工場が必要なモノを必要なタイミングで納品するために、生産計画と作業計画を連動させます。
生産計画から順に製造前の全工程・作業を計画することで、生産計画に沿った最適なタイミングで業務が遂行されます。
そのために情報の一元管理と可視化が重要です。計画情報をリアルタイムに管理することで、変更が生じた場合でもスムーズに計画を修正することができます。
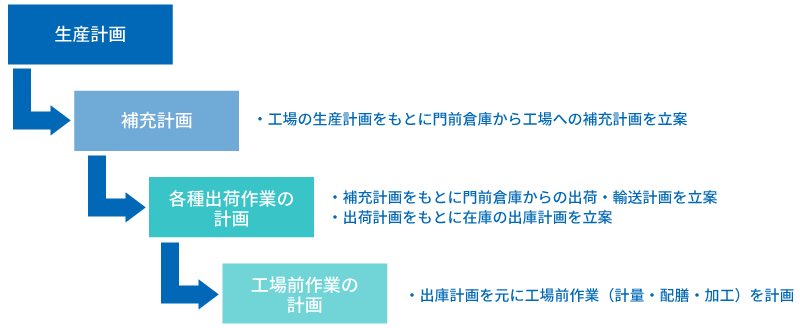
門前倉庫を活用しJIT納品を実現しやすくする
多くの場合、原材料の輸送手段決定やトラックの手配など、物流に関する業務はサプライヤーが手配しています。 サプライヤーは可能な範囲で顧客(工場)の要望を聞き入れてくれますが、工場にとって最適な条件であるとは言い難いのが現状です。 工場への納品を門前倉庫(自社拠点)から行うことで、生産計画に沿った最適なタイミングで計量や配膳を行い、生産ラインへすぐ投入できる状態で届けられるようになります。
原材料に関わる物流(調達物流)が抱える課題についてはこちら(第2話)
業務、仕組みの見直しに有効な手法「リビルド」
モノや情報の流れが上手くいっていないとき、現状を細かく分解し最適な状態に再構築する「リビルド」という手法が有効です。「原材料の計量は製造工程だ」といった思い込みを捨て、業務プロセスを細かく分解して問題点を洗い出します。
そして最適な流れになるよう、ゴール(生産計画)から逆算して再構築します。
モノと情報の流れ(ネットワーク構造)も合わせて整えることで、製造工程に加え全社的なサプライチェーンを最適化できます。
製造業におけるサプライチェーンの最適化、強靭化の取り組みは『2021年版ものづくり白書』でも提唱されている重要な取り組みです。
大規模な改革になるため、関係する部門やコストがかかるなどハードルの高い取り組みです。しかし得られる効果は大きく、長期的かつ戦略的に取り組む企業が増えています。
工場内での改善活動に限界を感じている方、生産ラインを自動化したが思ったような効果が得られなかった方は、製造工程全体に目を向けられてはいかがでしょうか。
製造業におけるサプライチェーン最適化、強靭化の取り組みはこちら(第1話)
まとめ
「モノづくり」の基盤を強化するため、多くの企業が工場のリソースを「製造」に集中させるべく取り組んでいます。
そのためには以下2つの改善が有効です。
- ・改善1. 工場の業務と在庫配置を見直す
-
- - 工場の業務を細かく分解し、本当に工場で行うべきか検討
- - BCPの観点、納品リードタイム、生産計画を踏まえ、工場で持つべき在庫量を明確化
余剰の在庫は門前倉庫など別拠点で集約保管
- ・改善2. 生産計画をもとにJIT納品の仕組みを作る
-
- - 門前倉庫を構えることで、JIT納品の仕組みが作りやすくなる
- - 生産計画をもとに製造前の業務を計画し、生産計画に最適なタイミングで業務が行われるようにする
「従来の改善では思ったような効果が得られなかった方は、このような改革手法を一度試されてはいかがでしょうか。