工場におけるコア業務とは「製造」そのもので、自社の価値を高める重要な業務です。
しかし工場ではそれ以外の業務もたくさん行われており、「物流」はその代表的な例です。
当コラムでは、構内物流(工場施設内で発生する物流業務)を改革し、リソースをノンコア業務からコア業務へ集中させる方法について解説します。
目次
-
- ・シンプル化・自動化して構内物流を改革
-
- ・ポイントは業務フローの細分化
- ・ECRSの視点でムダを排除
-
- ・材料の入出庫を自動化
- ・モノの移動を自動化
5. まとめ
コラムのポイント
- ・隠れているムダを見つけるポイント
- ・構内物流の自動化に向けた具体例
- ・改革のコツ「標準化」の重要性
工場は「モノづくり」に集中できているか
第3話でも述べましたが、
工場におけるコア業務とは「製造(モノづくり)」そのもので、自社の価値を高める重要な業務です。しかし工場ではそれ以外の業務もたくさん行われており、「物流」はその代表的な例です。
製造の前工程や後工程では、材料を入荷検品し保管場所へ格納したり、生産ラインへ運搬するといった構内物流が必ず発生します。
決して少なくないリソース(スペース・人)が使われていますが、これらの作業をゼロにすることはできません。限りあるリソースを「モノづくり」に集中させるための構内物流の改革は重要なテーマです。
シンプル化・自動化して構内物流を改革
構内物流を改革する上で重要なキーワードは「シンプル化」と「自動化」です。
構内物流をシンプル化・自動化することで「リソースのムダ遣い」が減り、工場内のリソースをコア業務へさらに集中させることができます。
- ・シンプル化: 構内物流に潜むムダをそぎ落とし単純化する
- ・自動化 :人の手(目)で行われていた作業をロボットやセンサーに代替させる
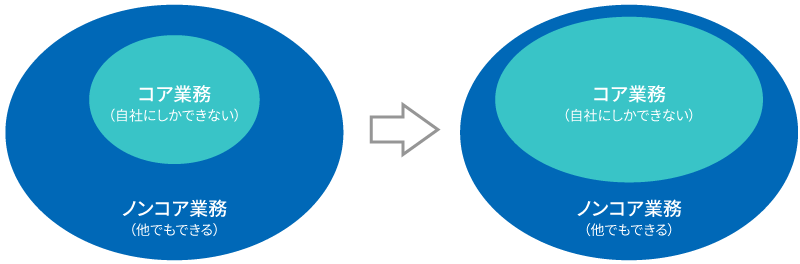
構内物流のムダをそぎ落とす
生産現場では日々改善活動が行われています。しかし長年生産現場に携わっているからこそ当たり前になり、見落としてしまうものもあります。 イチから業務を棚卸し最適な形に組み直すことで、隠れていたムダを見つけ出して改善することができます。
ポイントは業務フローの細分化
隠れているムダを見つけやすくするため、まずは業務を細分化します。
今やっている作業を1つ残らず洗いだせるよう、業務を細かく分解していくことがポイントです。
例えば「材料を生産ラインへ運ぶ」作業は、「在庫置き場から指定の材料を探す」「指定された分だけ取り出す」「検品する」「生産ラインまで運ぶ」といったように細かく分けていきます。
ECRSの視点でムダを排除
細分化された作業1つ1つを「ECRS」の視点で見直し業務のムダを排除します。
E:Eliminate (排除) | 無くせないか |
---|---|
C:Combine (結合と分離) | 別の業務と一緒にできないか |
R:Rearrange (入替えと代替) | 順序を変更し効率化できないか |
S:Simplify (簡素化) | 簡素化、単純化できないか |
全作業を1つ1つ見ていくというと、本当にその必要があるのか疑問に思われる方もいらっしゃるかもしれません。
しかし先の通り当たり前の中に改善のヒントが隠されています。
先の「材料を生産ラインへ運ぶ」を例にした場合、このような改善が期待できます。
- E:持ち出し時の手書き台帳を廃止する
- C:同時に梱包資材も運搬する
- R:生産ラインが空く前に事前に指示を出して準備させる
- S:投入時のチェックルールを統一する
以上はあくまでECRS観点での改善例ですが、ムダがそぎ落とされ、シンプルな状態になっていると自動化も検討しやすくなります。ぜひ一度お試しください。
ロボットやマテハン機器で構内物流を自動化
製造工程を細かく分解し業務に潜むムダをそぎ落としたら、次は自動化を目指します。
ここでも細分化された作業1つ1つを見直します。
- ・本当に人がやる必要があるのか
- ・AIやロボットなど最新技術で代替することはできないか
材料の入出庫を自動化
生産に使用する材料や製品、資材など工場には多くの在庫が保管されています。
自動倉庫
在庫の保管によく使用されるのは自動倉庫です。保管効率を上げる(省スペース化)、入出庫やピッキング作業を自動化(省人化)することが可能ですが、デメリットもあります。
最近ではスマートファクトリー化の一環としてJIT納品モデルを推進する企業も増えています。
JIT納品モデルは門前倉庫を活用することが多く、その場合は工場には最小限の材料しか保管しません。スマートファクトリー化を進めたい企業にとっては、自動倉庫がむしろ過剰設備となる可能性もあるため注意が必要です。
JIT納品モデルの詳細はこちら(第2話)
ロボット
保管効率の向上に加え、棚の出し入れをロボットで自動化するという方法もあります。
ロボットの中には、軽量ラックなど棚にしまわれた在庫を取り出してくれるものがあります。以下の写真はハイロボティクス社製の自律型ケースハンドリングロボットです。
大型のパレット倉庫だけでなく、写真のように段ボール箱やプラスチックコンテナの出し入れに適応したロボットも開発されています。
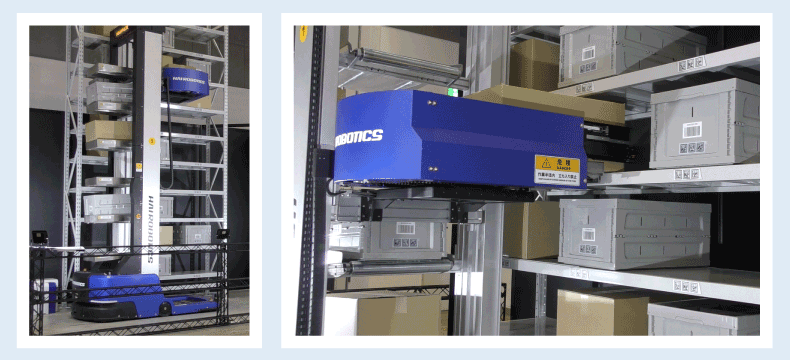
このようなロボットは自動倉庫と比べ、以下のようなメリットがあります。
- ・在庫の保管は軽量ラックを使用するため比較的簡単に早くスタートできる
- ・拡張性が高く、在庫が増えても必要な分だけ軽量ラックを増設・移設すればよい
確かにロボットは万能ではありません。保管している在庫の梱包形態(段ボール箱、袋、梱包無し)・大きさ・重さ、そして設置場所の条件など様々な要素によって自動化できない場合もあります。
しかし自動倉庫一択であった従来と比べ、現在は様々な機能・特長を持つロボットやマテハンが開発されています。
皆さんに最適なロボットが見つかる時代です。ぜひロボットを活用した自動化を検討してみましょう。
モノの移動を自動化
意外かもしれませんが、製造工程は細かな物流工程(モノの動き)の積み重ねです。
材料を生産ラインへ、生産したモノを一時的に保管場所へ、オーダーが入ったら出荷作業場へ運ぶといったように、工程を経る度にモノの移動が発生します。
工場施設内はある程度広いスペースが確保されているため、移動にかかる時間は決して少なくありません。モノの移動こそ自動化すべき代表例と言えます。
モノの構内移動を自動化する時によく使われるのが、コンベアや搬送用ロボットです。
この2つだけでも移動の自動化はできますが、自動倉庫と連携させることで材料の出庫から生産ラインへの搬送までを完全自動化することも可能です。
- 1. 自動倉庫から材料を出庫する
- 2. 出庫口に搬送用ロボットが待機し材料が積み込まれる(自動で積まれるよう設計)
- 3. 搬送用ロボットで指定の生産ラインまで運ぶ
この流れを実現するためには、自動倉庫や搬送用ロボットに指示を出すシステムと生産管理システムを連携させる必要があります。 生産管理システム上で「これから○○を生産する」という処理がなされると、自動倉庫や搬送用ロボットに稼働指示がかかるようにするのです。 自動化を検討する際は自動化設備や情報システムの連携を考慮して業務を見直すことで、自動化の幅を広げられます。
失敗しないためのコツは「標準化」
シンプル化するときにも自動化するときにも重要になるのが業務の「標準化」です。
作業フロアや担当者ごとに運用が異なっている状態はシンプル化されているとは言えません。
本当に必要な場合を除き、できる限り標準化することで業務がシンプルになります。標準化することで作業品質の向上や、新人の早期戦力化などのメリットも得ることができます。
ロボットを活用した自動化を推進する際は、特に標準化が重要となります。
先の通り、万能なロボット・マテハン機器はありません。それぞれ得意とする分野が違っているため、標準化されていない状態で進めても自動化できる範囲が限定されてしまいます。そのためにも標準化は大切です。
例えば仕入れ先から調達した材料などは梱包形態・大きさ・重さ・材質・ラベルの位置がバラバラなため、外部倉庫に一旦格納して形状を揃え、配膳なども行ってから工場へ納品されるようにすることで標準化も進みます。
また標準化されていれば、AIを活用した画像検品(画像認識)やデータ化(文字認識)も行いやすくなります。
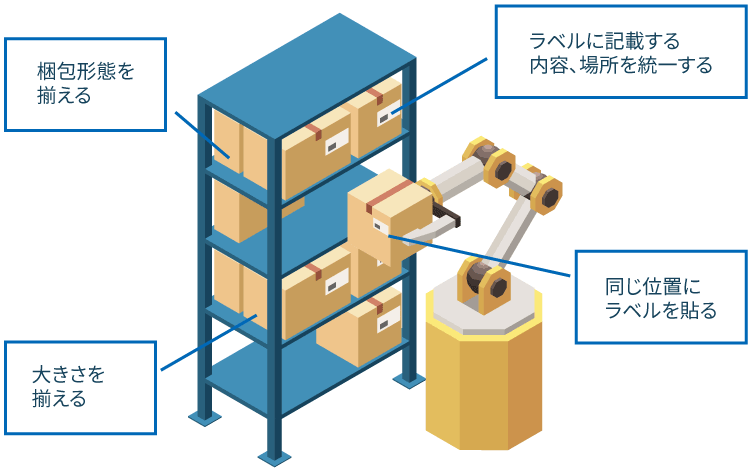
まとめ
構内物流を改革して省人化・省力化することで、工場内のリソースをコア業務へ集中させることができます。
まずは業務全体をシンプル化しムダをそぎ落としていきます。今やっている作業を1つ残らず洗いだせるよう業務を細かく分解し、ECRSの観点で作業1つ1つを見直すことで隠れていたムダを改善できます。
業務に潜むムダを無くせたら、次は自動化を推進します。在庫の入出庫については、自動倉庫やハンドリングロボットが活用されています。
さらに搬送用ロボットと連携させることで材料の出庫から生産ラインへの搬送までを完全自動化することも可能です。情報システムの連携や業務フローの見直しも必要となりますが、単体で自動化するより大きな効果が得られます。
工場内の構内物流で使用されているリソース(スペース・人)は決して少なくありません。
工場を改革する1つの方法として、構内物流にも取り組まれてはいかがでしょうか。