こんにちは。WMS:倉庫管理システム「SLIMS(スリムス)」を提供するセイノー情報サービスです。
「物流」が商品やサービスの一部分となり、競合他社との差別化要素になる時代となりました。
倉庫管理が企業を支える重要な業務として考えられ、その改善に緊急性が増しています。
このコラムでは、倉庫管理の基本から効率化の方法、混同されがちな在庫管理との違いを詳しく解説します。
目次
1. 倉庫管理とは
2. 在庫管理とは
3. 倉庫業務を効率化する方法
4. 倉庫管理システムとは
6. まとめ
倉庫管理とは
倉庫管理とは、倉庫(物流センター)内の業務をマネジメントすることです。
そこでは管理責任者(物流センター長)や各作業チームのリーダーがマネジメント業務を担っています。
Quality:品質、Cost:コスト、Delivery:納期、いわゆるQCDの観点で倉庫業務を管理することで、作業精度と品質の向上・生産性向上・納期遅延の防止・作業の安全性向上など、
一見相反する目標を同時に達成できるようゴールへ導きます。
関連コラム
・物流現場の管理者の役割とは:3章「物流センター改善における管理のポイント」
倉庫管理の目的
倉庫管理の目的は、先のQCDを最適に保つことで、顧客満足度の向上やビジネスの発展につながります。
製造業におけるJIT納品や宅配の時間指定など、「物流」が商品やサービスの一部分となり、差別化要素になる時代となりました。物流を経営課題として捉える経営者が増えており、積極的に投資をする企業も少なくありません。
特に物流センターでは人手不足が著しく「自動化」が大きなテーマとなっています。マテハン機器やロボット、AI(人工知能)、カメラやセンサーの活用や、システムに蓄積されるデータの有効活用も重要視されています。
将来を見据えて段階的・継続的な取り組みを行い、時代の変化に素早く対応できる企業が勝ち残っていけるのです。
倉庫管理主任者と倉庫管理の業務とは
倉庫業を営む上で、倉庫業法によって「倉庫管理主任者」の選任が義務付けられています。
倉庫管理主任者は倉庫業務の広い範囲で管理業務を遂行します。例えば倉庫の施設に関する管理や、荷役など業務に関する管理、労働災害に関する管理、作業員の育成など幅広い管理能力が要求されます。
そのため一定期間の実務を経験している、もしくは倉庫管理主任者になるための講習を受講している者から選任します。
ではどんなポイントで管理すると良いのでしょうか?
倉庫管理とは、倉庫(物流センター)内の業務をマネジメントすることです。そのために「計画」と「評価」が大切になります。作業管理においては、運用ルールの設定とマニュアル化が有効です。
加えて、そのマニュアルが正しく守られているか定期的に評価する必要があります。要員管理では生産性などの指標を使った評価が有効です。
また全てにおいて、倉庫内の状況が可視化されていることが必要で、変化・異常に対して未然に防止したり、早期にリカバリーできる管理体制を作ることが大切なポイントです。
-
倉庫管理業務(例)
- ・倉庫内を見回って作業ルールが遵守されているか定期的にチェックする
- ・作業の進捗状況をチェックし遅延が発生しないよう要員配置を調整する
- ・出荷の傾向を量や頻度でとらえ定期的に在庫配置を見直す
- ・実績を数値化(KPI)し変化に対して早期のリカバリー策を検討する
在庫管理とは
販売や製造にかかわるすべての在庫を管理することをいいます。
製造業でいえば原材料や部品、中間品、完成品(商品)はもちろんですが、保管・輸送に必要な段ボールや緩衝材などの資材まで、企業が持つ全ての在庫を漏れなく管理することが「在庫管理」です。
販売計画や生産計画、調達計画などの社内の情報に加え、市場の傾向などを加味して発注量や生産のタイミングをコントロールします。
余剰在庫による廃棄や、欠品による販売機会の損失をなくし、在庫を最適化して自社の利益を最大化する活動です。
倉庫管理との違い
倉庫管理と在庫管理は混同されやすいのですが、全く別の業務です。
大きな違いは「範囲」と「目的」です。
倉庫管理とは前述の通り、倉庫(物流センター)内の業務をマネジメントすることです。管理責任者(物流センター長)や各作業チームのリーダーがQCDの観点で業務を管理することで、
「品質向上」「生産性向上」「コスト削減」といった目標を達成します。
倉庫業務の1つに「在庫管理」があります。倉庫における在庫管理は倉庫内の在庫に限定して行われます。
倉庫内の在庫は商品別、入荷日別、ロット別、期限別、得意先別など、様々な観点で管理されています。倉庫内の「在庫管理」は常に入出荷業務と紐づいており、作業ミスの撲滅や効率化を図ることを優先として在庫管理を強化しています。
一方「在庫管理」は、企業活動に紐づく在庫全てを管理します。工場や倉庫、営業拠点、店舗、客先など保管場所を問いません。また、発注はしたけれどもまだ自社に納品していない在庫も対象とします。
業務と関連性が高い「倉庫業務の在庫管理」と比べ、一般的な在庫管理とは、在庫を情報(数字)として正しく認識し、適切な在庫量(または金額)が維持されるようコントロールすることに重きを置いています。
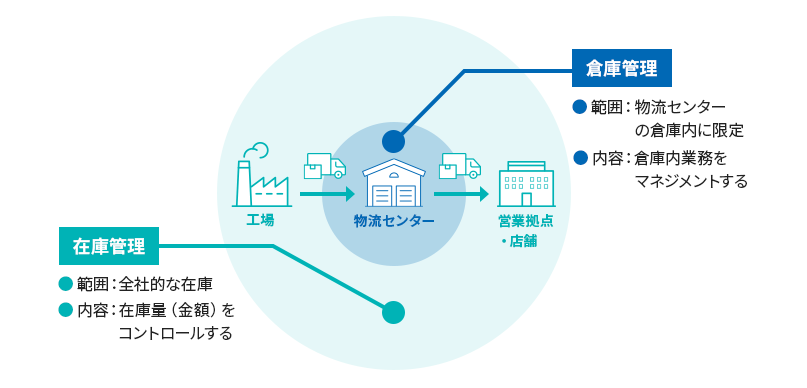
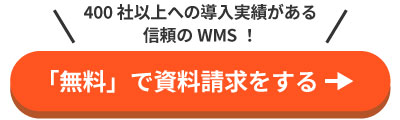
倉庫業務を効率化する方法
効率化は倉庫管理における代表的な課題で、多くの企業が改善テーマの1つとして取り組んでいます。
倉庫業務を効率化する方法について基本的なものから、いま注目されているものまで幅広くご紹介します。
倉庫内の整理整頓
倉庫内の整理は改善活動の第1ステップです。
大きくは在庫の保管と備品の整理整頓の2種類に分けられます。
在庫の保管
どの商品がどこに保管しているかを明確にします。フロア(階層)、エリア、棚の列・連・段まで細かく保管場所を管理します。 また、仮置き場に長期間放置されているモノを廃棄したり返品するなど、あるべき場所へ戻すことで在庫を正しく管理でき作業ミスも撲滅できます。
備品の整理整頓
使用した台車やパレットは所定の位置に戻します。段ボールや緩衝材も同様です。また不要なモノは廃棄しましょう。 作業場所や通路の幅がきちんと確保できることで、作業がしやすくなるとともに事故のリスクを軽減できます。
作業動線の見直し
作業動線や配置を見直して人とモノの流れを整えることで、ムダな移動を減らします。
人とモノの流れを整える
一般的に作業動線は、U字型やI字型など一方通行にするのが良いとされています。
入荷品の荷卸しから在庫保管、出荷梱包、荷積みまでがU字型やI字型で進められるように作業動線と倉庫内のレイアウトを設計することで、ムダな移動を減らすとともに衝突などの事故も撲滅します。
移動を減らす・無くす
作業動線を一筆書きにしたり、ピッキング方式を変えることでムダな歩行を削減します。
倉庫業務では約60%の時間を移動が占めると言われており、作業動線は業務改善に大きく影響します。
また商品や得意先の特性に合わせて柔軟にピッキング方式(オーダー/トータル)を変更したり、在庫配置を変えることも移動の削減に貢献します。
棚搬送型ロボットを活用すれば、人の移動そのものを無くすこともできます。
在庫配置の適正化
「作業動線の見直し」でもふれましたが、在庫の保管場所を変えることで移動を減らすことができます。 例えば、商品のカテゴリーごとや商品番号順で固定されている保管場所(固定ロケーション)を、フリーロケーション化し、以下の観点で在庫配置を見直すことで作業の効率化がさらに進みます。
-
保管のコツ(例)
- ・出荷頻度の高い商品は、作業場に近い場所に保管(移動距離を短くする)
- ・さらに、作業がしやすい棚の手前・胸や腰ぐらいの高さに保管
- ・重たい商品は棚の一番下に保管
- ・小さい商品やチェックが難しい商品は目線の高さに保管
- ・付属品など一緒に出荷される商品は隣同士など近くに保管
ロボット、マテハン機器の活用
いま最も注目されているのが、ロボットやマテハン機器など最新のデジタル技術の活用です。
最近では建物の補強など工事を伴わないマテハン機器や、比較的安価なロボットも増えています。搬送ロボットに限ってもAGV(無人搬送ロボット)、AGF(自動運転フォークリフト)、GTP(棚搬送型ロボット)、
AMR(協働型搬送ロボット)など種類が豊富なため、運用シーンに合わせて最適なものが選べます。
マテハン機器についても自動倉庫や仕分け機・梱包機など、保管から出荷梱包、移動まで倉庫内業務の全領域で効率化をはかれるほどラインナップが充実しています。
以前は大手企業や通販業者など限定した企業のみの利用でしたが、最近では中小企業でも活用が進んでいます。深刻な人手不足が進む物流現場では、ロボットやマテハン機器の活用がビジネス成長の成否を握ることになるでしょう。
関連コラム:物流ロボットとは マテハンとの違いや種類を紹介
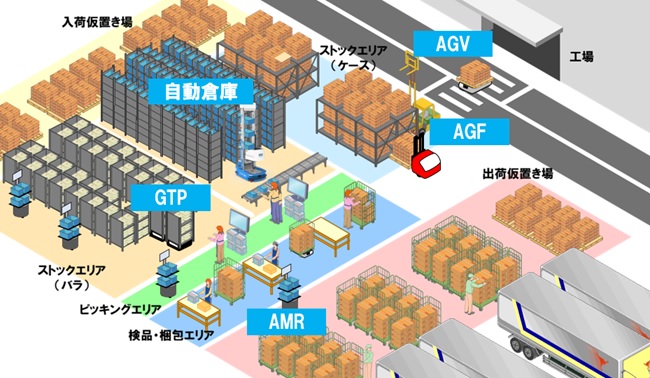
倉庫管理システムとは
倉庫管理システムとは、倉庫内の業務やマネジメントを支援するシステムです。
一般的にはWMS(Warehouse Management System)とよばれており、業種業態を問わず多くの倉庫で活用されています。
大まかには入荷管理・出荷管理・在庫管理・進捗管理という4つの機能を備えており、WMSを活用することで作業の精度向上や効率化が図れます。
関連コラム:WMS(倉庫管理システム)とは
倉庫管理システムで業務を効率化
物流現場の人手不足は深刻で、労働力の確保と人材育成は重要な経営課題の1つとなっています。
業務ノウハウの詰まったWMSを活用することで、より少ない人数で多くの作業量に対応できるようになります。
ハンディターミナルを活用すれば、作業と在庫の情報がリアルタイムに把握できます。また、ロボット・AIなどの最新のデジタル技術やマテハン機器と連携させることで、WMSを軸にして物流DXが加速していきます。
入荷管理
倉庫に入ってきたモノを検品し、所定の保管場所(ロケーション)へ保管する業務です。
検品の際に賞味期限やロット情報を収集することで、ロット番号の逆転防止や得意先ごとの出荷期限設定など多様な出荷ニーズに対応できます。
最近は入荷品を在庫保管せずそのまま出荷するクロスドック方式を採用する倉庫も増えています。
WMSを活用することで在庫品は所定のロケーションもしくは空きロケーションが、当日出荷品は出荷作業のための仮置き場が指示されるため、熟練の作業員から新人まで誰でもミスなく作業することができます。
出荷管理
WMSから出る出荷指示に従って所定のロケーションからモノを取り出し、決められたルールに従って梱包します。
出荷は倉庫内業務の中で最もコストのかかる業務です。特にピッキングや梱包作業は複雑化が進んでおり注意が必要です。
在庫配置を見直したりロボットを活用することで、移動を減らす・無くすことができます。また、オーダーピッキング方式、トータルピッキング方式など作業方法を柔軟にコントロールすることで効率化できます。
在庫管理
どの商品が、どのロケーションに、どれだけ保管されているかといった基本情報と、荷姿や期限・ロットなどの詳細な情報を一元管理します。 ハンディターミナルを活用することでリアルタイムに様々な情報を収集・データ化できます。その情報を社内にフィードバックすることで、過剰在庫や欠品による廃棄や販売機会の損失を防止します。 顧客から入る在庫への問合せ対応もスピードアップします。
進捗管理
ハンディターミナルを活用することで、リアルタイムに進捗状況を把握できます。 進捗状況を大型モニタで現場に表示することで、作業者全員が進捗状況への意識が高まり作業のスピードアップに繋がります。遅延を早期に発見し、遅延している作業へ応援を向かわせることができます。
また、作業進捗はフロア・作業単位・得意先・運送会社などシーンに合った切り口で管理します。管理者が欲しい情報を見たい形式で可視化し表示することで、早期の問題発見とリカバリーが可能となります。
セイノー情報サービスの倉庫管理システム「SLIMS」
セイノー情報サービスの「SLIMS」は、販売開始以来400社以上に導入実績があり、企業の規模・業種業態を問わず多くのお客様から支持されている倉庫管理システム(WMS)です。
人手不足が深刻化する物流現場の変革に向けて、WMSを軸に業務の効率化、DXをご提案します。また、WMSに限らず周辺システムも充実しており、サプライチェーン全体の課題解決に貢献します。
関連情報:倉庫管理システム(WMS)「SLIMS」の詳細
- 「SLIMS」の主な特長
-
- ・WMSに限らず周辺システムも充実、サプライチェーン全体の課題解決に貢献
- ・ビジネス環境の変化に合わせて常に進化
- ・ロボットやAI、マテハン機器など最新のデジタル技術と連携
まとめ
倉庫管理とは、倉庫(物流センター)内の業務をマネジメントすることです。QCDの観点で倉庫業務を管理して物流品質を高め、顧客満足度の向上とビジネスの発展に貢献します。
倉庫管理と混同されがちなのが、「在庫管理」です。
倉庫における在庫管理は、倉庫内の在庫に限定して行われます。入出荷などの作業との関連性が高く、作業ミスの撲滅や効率化を図るために定期的なチェックや改善策の検討が行われます。
一方「在庫管理」は、企業活動に紐づく在庫全てを管理します。在庫を情報(数字)として正しく捉え、適切な在庫量(または金額)が維持されるようコントロールすることに重きを置きます。
人手不足が進む倉庫業務において、重要なテーマが「効率化」です。
倉庫内の整理や作業動線の見直し、在庫配置の適正化に加え、ロボットやマテハン機器の活用が注目されています。そしてこれらの活動を支える軸となるのがWMS(倉庫管理システム)です。
業務ノウハウの詰まったWMSに、ロボットなど最新のデジタル技術を連携させることで物流DXがさらに加速します。
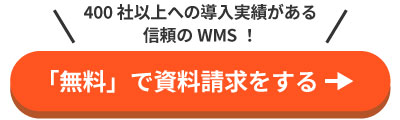
このコラムの監修者![]() |
セイノー情報サービスは400社以上へのWMS導入を通して培った物流ノウハウをもとに、お客様の戦略立案や物流改善をご支援しています。 当コラムは、経験豊富なコンサルタントやロジスティクス経営士・物流技術管理士などの資格を持った社員が監修しています。 |
---|