第7話に続き、改善活動の3要素QCDの中のC:Cost(コスト)として生産性の管理を取り上げます。
今回は、生産性の可視化と定期的なチェックについて解説します。
目次
1. 生産性の管理とは
- ・生産性を数値で管理するメリット
- ・2つの定期チェック
2. 日別の生産性のチェック
4. 生産性を可視化する方法
- ・業務日報を活用し全体的に可視化
- ・ITを活用し詳細に可視化
5. まとめ
コラムのポイント
- ・生産性を数値で管理するメリット
- ・管理の基本となる2つの生産性チェック
- ・業務日報を活用した生産性の可視化手順
生産性の管理とは
第7話で解説したとおり、物流センターにおけるC:Cost(コスト)の改善には、生産性管理の強化が有効です。物流コストの中でも比率の大きい作業人件費の増減に直結するため、改善できたときに得られるメリットが大きく、現場の工夫によって早期の効果も得られます。
多くの企業が取り組まれており、データの取得や可視化の方法も様々に試行錯誤されています。
※第7話(コスト適正化のための生産性管理 なぜ生産性の改善が有効なのか)は、こちら
生産性を数値で管理するメリット
物流現場における生産性は、多くの場合「作業別生産性」として作業単位で管理されます。
例えば、ピッキングの作業生産性は「1人1時間あたりのピッキング件数」です。
作業生産性を数値で管理することで、生産性が低下した(1回あたりの作業時間が増えた)という問題を感覚ではなく数値で把握できます。作業単位だけではなく、日別、時間別、作業者別など様々な観点で生産性を比較することで変化に気付くことができ、問題の早期改善につながります。
加えて、改善の前後の生産性を比較することで効果の確認もでき、施策の評価が可能となります。
つまり生産性を数値で管理することで、人件費を適正化するための改善サイクルがより加速するのです。
2つの定期チェック
数値の変化に気付くには定期的なチェックが欠かせません。次の2つのチェックを行うと良いでしょう。
問題の発見と原因を特定するための「日別の生産性チェック」と、曜日・月末月初など物量の波に合わせた要員配置を目的とした「週または月別の生産性チェック」です。
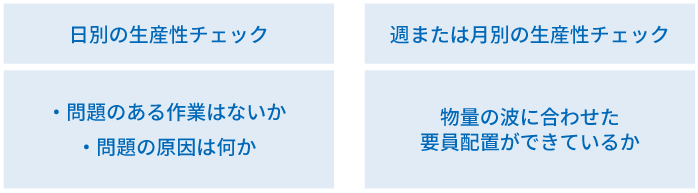
日別の生産性チェック
作業別生産性の推移から、数値が低下している作業が無いかチェックします。
そして、その原因を調査・特定して改善活動に繋げていきます。
生産性の低下が見つかったら、まずはその作業に関連する数値・指標を確認してみましょう。よくあるものとしては急な変化・変更のために通常では発生しない余分な作業や待ち時間の発生があげられます。
例:出荷作業の生産性低下を招く要因
- ・1つの届け先あたりの出荷明細数・出荷数量に大きな変化があったか
‐出荷特性の変化を確認 - ・出荷指示データの受信や現場への作業指示が遅れていないか
‐作業開始時刻を確認 - ・入荷作業の遅延が影響して出荷に待ち時間が発生していないか
‐入荷特性の変化を確認 - ・大口出荷により不慣れな臨時作業者を投入していないか
‐当日の物量推移を確認
加えて、当日の作業に何か特殊な事象が発生しなかったかを作業者にヒアリングすることも大切なことです。
ヒアリングをもとに、入荷および出荷実績データの変化を確認することで、新しい課題の発見にもつながります。
改善した生産性をさらに向上させる方法に関する解説はこちら
週または月別の生産性チェック
どの物流現場でも物量の波は必ず発生します。
通常日よりも月末月初の作業量が跳ね上がったり、ある曜日は特定の大口納品先向けの出荷があったりします。日別だけでなく時間帯別にも波が発生するでしょう。
物流現場では物量をコントロールすることはできませんが、物量に応じて要員をコントロールすることは可能です。
週または月別の生産性をチェックし、適正にコントロールできているか定期的に確認しましょう。
例えば、直近1年間または前年同月の波から特性を把握し、当月当週の物量を予測することも有効です。物量の多い日は作業員を増やし物量の少ない日は減らすなど、予測に合わせて柔軟に要員調整します。
生産性の維持・向上には、物量の波に合わせた要員のコントロールが不可欠です。
必要以上の要員を投入すれば生産性の低下を招き、反対に少なければ残業が発生し、最悪のケースでは作業をやり切れないこともあります。物量に合わせて要員手配し、生産性を一定に保つことが重要なポイントです。
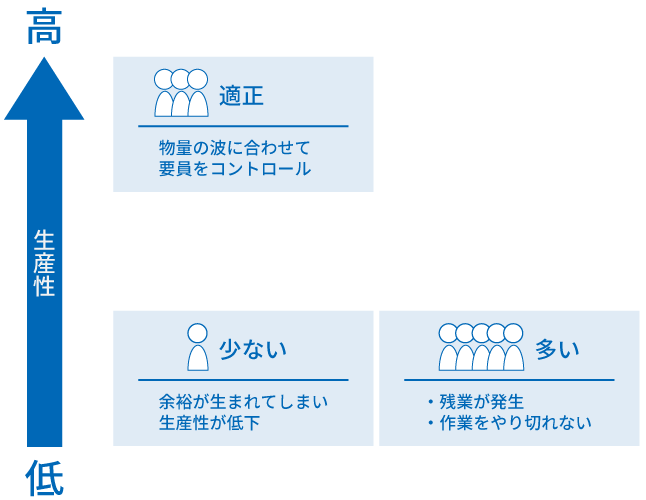
作業生産性を可視化する方法
定期チェックのためには、生産性が可視化されていることが前提です。
そこで生産性の可視化方法について、当社の事例を交えて解説します。
業務日報を活用し全体的に可視化
生産性の可視化に向けて最も簡単な方法は、業務日報を活用する方法です。
必要な情報は当日の作業別の物量とそれに関わった人数(作業時間)の2点です。
以下に日報を使った可視化手順をまとめてみました。
(1) 作業者が日報を記入
1日の業務終了後、全作業者に「今日はどの作業を何時~何時まで実施したか」を記入してもらいます。
気付いた点なども記入できるスペースを設けておくと、新しい改善テーマの発見も期待できます。
- 記入項目:作業日・氏名・業務名・作業開始時間・作業終了時間・気付いた点 など
-
- ‐業務名は現場作業プロセスにも依存するが、簡易的な分類でもよい
- (例:入荷・出荷・事務・その他)
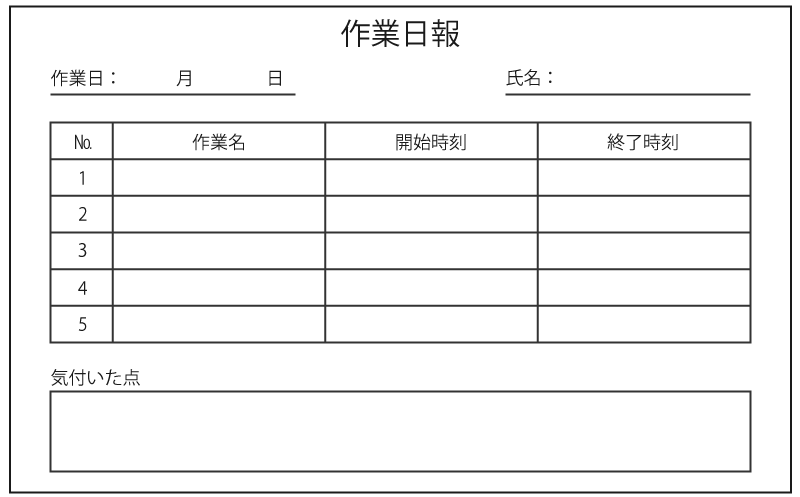
(2)事務担当者が時間を集計
作業者が記入した日報の情報をエクセル等に入力し集計します。
これで日別・作業別の実績(時間)が準備できました。
(3)日別の作業物量を集計
次は物量の情報を準備します。
システムからアウトプットできるデータや、台帳等で管理している情報(パレット数やピッキングリスト枚数 など)を活用します。データ準備のためにシステム開発や多くの労力を要する場合は、入荷や出荷など大きな作業単位の数値だけでも準備しましょう。
(4)生産性を算出し分析
生産性は(3)作業物量 を(2)作業時間で割って算出します。
日別や作業別で生産性を集計し、定期的なチェックに活用しましょう。
ITを活用し詳細に可視化
当社で運営する物流センターでは、さらに作業者別や時間帯別、商品別、ロケーション(保管場所)別の作業時間を把握するためにハンディ端末による作業実績データを収集・分析し、改善活動に役立てています。
また、ハンディ端末を使用しない業務(流通加工や運搬・清掃など)に関しても生産性を可視化するため、FLabor(フレイバー)というソリューションを自社開発し活用しています。
FLaborは現場管理者向けの「生産性可視化ツール」で、現場における様々な業務シーンのタイムスタンプ(作業時間情報)を取得できます。各作業の開始時・終了時にICカードをタブレット端末にかざすだけで作業時間が登録でき、「定期生産性チェック」に必要なデータが簡単に収集できます。
AIによる顔認証機能を活用すれば、ICカードをかざす手間も省けます。
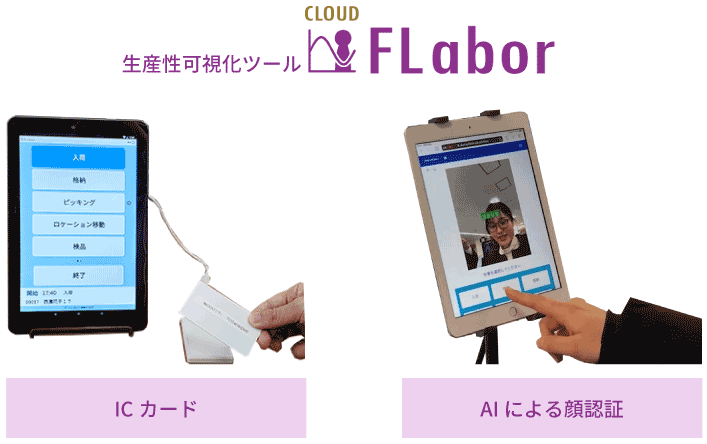
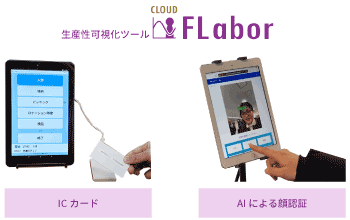
※FLaborの詳細はこちら
まとめ
物流センターにおけるC:Cost(コスト)の改善のためには、生産性管理の強化がとても有効です。
生産性を可視化し定期的にチェックしましょう。
- ・日別の生産性:生産性の低下している作業とその原因を見つける
- ・週または月別の生産性:物量の波に合わせた要員手配ができているかをチェック
2つの生産性チェック
手間をかけず早く取り組みたい方は、まずは業務日報の活用をお勧めします。作業者1名は1時間当たりにどれだけの作業を実行できるのか、その生産性は週または月別でどのような推移になっているかをチェックしましょう。
さらに詳しく生産性を調査・特定したい方は、ITの活用が有効です。
ハンディ端末や作業時間を収集できるツールを活用することで、より効率的にデータ収集できます。加えてエクセルやBIツールを使えば、より深い分析ができ多くの気付きを得ることができます。
このように生産性を数値で管理すると、改善活動の効果がどのように現れているかの振り返りが可能です。
施策の評価もでき、改善活動のサイクルがスピードアップします。
FLabor(フレイバー)を活用した改善活動については、導入事例ページで詳しく解説していますので、ぜひ参考にしてください。
- ※導入事例はこちら
-
- KPI活用のPDCAサイクルが高速化 ~課題発見を機に生産性が13%向上~
- 株式会社ゲオホールディングス様「FLabor」導入事例