こんにちは。WMS:倉庫管理システム「SLIMS(スリムス)」を提供するセイノー情報サービスです。
物流現場に潜んでいる「見えていない課題」を見つけるにはコツがあります。
当コラムでは2つの事例をもとに課題の見つけ方とコツ、そして改善策をご紹介します。
目次
コラムのポイント
- ・物流センター長こそ「見えていない課題」を見つけやすい理由
- ・現場管理者ならではの仮説の立て方
- ・何気なくやってしまうムダ・工数ロスの見つけ方
物流現場では全ての課題が「見えている」わけではない
物流現場では全ての課題が「見えている」わけではありません。
通常、改善活動は「見えている」課題から優先的に取り組まれます。
より高度な管理・運用が行われている物流現場は「見えていない課題」の改善に取り組んでいます。
「見えていない課題」を探して改善することで、物流品質をより向上させることができます。
物流現場における「見えていない」課題とは
例えば「梱包エリアで作業待ちの品が滞留しやすい」など「目に見える」形で問題が発生すれば、梱包エリアの作業員数を増やすなどすぐに対応されます。
一方、意識して探さなければ見つけられない課題もあります。
例えば「個別対応が必要なため、梱包作業に手間がかかる顧客(届け先)」がいたとします。作業者や現場のチームリーダが「この顧客への対応は大変だ」「時間がかかる」と感じていたとしても、「大口顧客なので仕方がない」となることは珍しくありません。しかし物流コストを顧客別に調べると、他の顧客よりコスト高になっていた、つまり改善すべき課題であった、ということがあります。こうした課題とは認識されていない課題が物流現場には潜んでいます。
当社ではこれらを「見えていない」課題と呼んでいます。
物流現場の見えている課題・見えていない課題に関する詳しい解説はこちら
現場改善のカギは「見えていない課題」
先の通り見えている課題は比較的すぐ改善に取り組まれますが、見えていない課題は探すところから始めなければいけません。一見大変なように思えますが、コツを掴めば見つけられるようになります。特に物流センター長やチームリーダーなど物流現場を熟知している方だからこそできることがたくさんあります。
「色々と改善に取り組んできて、やるべき(やれる)事が無くなってきた」と感じていても、それは「見えている課題が無くなってきた」状態で「見えていない課題が潜んでいる」ことも少なくないため、ぜひ取り組んでいただきたい分野です。
見つけ方事例_1.仮説をもとに改善した生産性をさらに改善
「様々な事を試したが生産性が思うように向上しない」
「改善活動によって数値が向上したものの、これ以上の改善は難しい」
そんな悩みを持つ方に、データ分析を通して「見えていない課題」を見つけ、更なる効果を上げた事例をご紹介します。これは当社が3PLサービスを請け負っている現場で実際に取り組んだ改善です。
3PLに関する詳しい解説はこちら
日別の生産性を見てみる
当社は3PLサービスを提供しており、その現場で改善活動を積極的に進めています。生産性向上もその1つで、一定の効果が出ています。しかし更なる改善を目指そうと見えない課題を探すため、データを分析しました。
まず作業工程別の日別の生産性をグラフ化します。
すると生産性はなだらかではなく、日ごとに上がったり下がったりしています。そこで生産性が低い日の共通点を探したところ、「あまり忙しくない」日、つまり作業量の少ない日に生産性が低下していたのです。
生産性をデータ化する方法はこちら
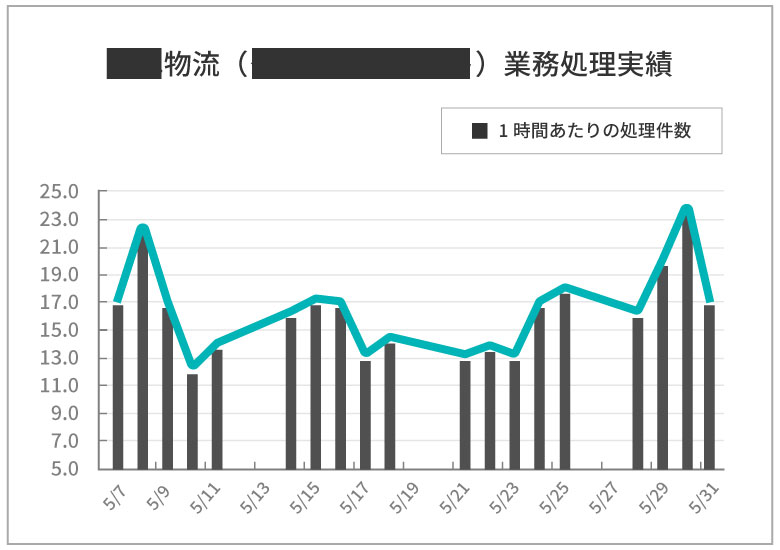
データを見る際のコツ
あまり忙しくない日の現場を見ていても作業員に待ちが発生したり遊んでいたりする様子は見受けられないが、生産性は低くなる、という現象は現場の管理者なら「何となく分かる」のではないでしょうか。
実はここにデータ分析のコツがあります。
分析する際は、仮説を立ててからデータを見てみましょう。一見難しいと感じるかもしれませんが、実は現場運営に携わる管理者だからこそ仮説が立てやすいのです。この事例のように「○○な時は△△になりやすい気がする(生産性の低下、ミスの発生など)」といった感覚をもとにしたり、作業者の「困った」や「気づき」を拾い上げてヒントにすると、比較的簡単に仮説が立てられます。
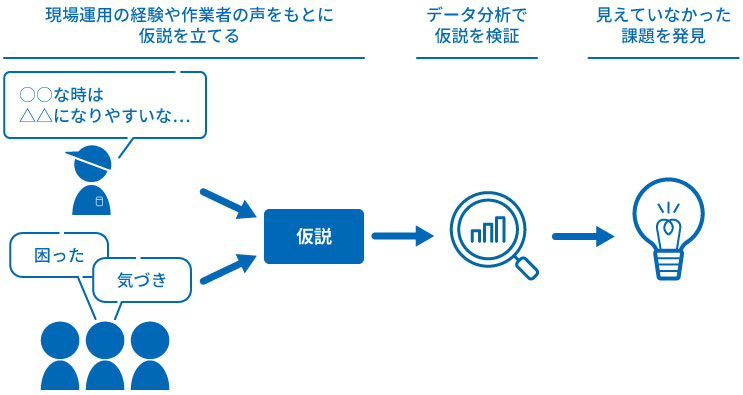
解決策は要員調整
先の通りデータから「生産性が良い日」の共通事項は「少し忙しい」ことだと分かっています。
そこで生産性が高かった日のデータから、作業量に対してどれくらいの作業員数にすると生産性が良くなるのかを算出します。そして要員調整によって「少し忙しい」状況をあえて作り出すと、生産性のバラつきが改善し、平均値も高くなります。
当社ではこのような分析や生産性の管理が簡単にできるよう、作業員管理システム「FLabor」を活用しています。
「セカンドストリート」によるリユース事業などを手掛ける株式会社ゲオホールディングス様でも活用いただいており、生産性が13%向上しています。
事例ダウンロード:株式会社ゲオホールディングス様「課題発見を機に生産性が13%向上」
見つけ方事例_2.現場観察でムダ、工数ロスの徹底排除
「ムダの排除」もよく取り組まれている改善テーマですが、コツを押さえたうえで現場を観察すると意外と新たな発見があります。
観察する際のコツ
改めて現場を観察すると、細かなムダやちょっとしたロスを見つけられます。
しかし改善活動が進んだ物流現場に潜むムダ・ロスは「見落としがち」なものばかりです。そこで予めどのようなムダ・工数ロスがありそうかリスト化しておき、それを見ながら現場を観察してみましょう。
その際のコツは、1つの作業に集中して細かく見ることです。そうすることで何気なくやっているムダを見つけられます。
リスト化する際のコツ
当社では作業を1つ1つの動作に細分化し、徹底的にチェックします。
例えば「歩行」を減らすために移動距離を短くする改善はされますが、ムダ・ロスを徹底排除したいなら「半歩戻り」「半歩踏み込み」も無くせないか検討すべきです。
作業中に手に持っているリストやハンディーターミナルの「持ち替え」も排除すべき動作です。さらに、そもそも手に何かを持っている「保持」も可能な限り無くしたほうがよいでしょう。日本製紙グループの物流を担う日本製紙物流株式会社様ではフォークリフトにタブレット端末を設置し、「作業指示書の保持」を無くしました。
事例ダウンロード:日本製紙物流株式会社「WMS・トラック予約システム導入による業務変革で売上拡大を狙う」
ロボット活用で解決されるロスも
意外に見落とされがちなのが「細かな作業中断」や「未習熟」による工数ロスです。
新人作業者を教育するために作業を中断する、作業に慣れておらず時間がかかるといったロスは「しょうがないこと」と見過ごされがちです。しかし物流ロボットを活用することで、解決できます。
GTP(棚搬送型ロボット)やAMR(自律走行搬送ロボット)を活用すれば、商品や格納場所に関する知識が無くても作業できます。ある物流現場ではGTPを導入し、1週間かかっていた新人教育を2時間に短縮しました。ロボット活用の狙いは将来の人手不足に備えることですが、副次的な効果があります。
物流ロボットの活用事例はこちら
まとめ
物流現場に潜む「見えていない課題」を見つけるのは一見大変なように思えますが、コツを掴めば見つけられるようになります。
データ分析
- ・最初に仮説を立て、それを証明するためにデータを分析する
- ・「○○な時は△△になりやすい気がする」といった現場感覚、作業員の「困った」や「気づき」などをもとに仮説を立てる
現場観察
- ・ムダやロスにつながる動きを予めリスト化し、それを見ながら作業を細かくチェックする
- ・リスト化する際は、作業を1つ1つの動きに細分化してムダ・ロスを徹底的に洗い出す
「色々と改善に取り組んできたので、やれる事が無くなってきた」と言う方はぜひ試してみてください。
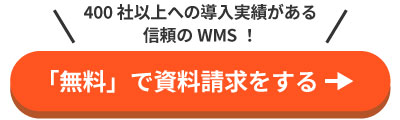
このコラムの監修者![]() |
セイノー情報サービスは400社以上へのWMS導入を通して培った物流ノウハウをもとに、お客様の戦略立案や物流改善をご支援しています。 当コラムは、経験豊富なコンサルタントやロジスティクス経営士・物流技術管理士などの資格を持った社員が監修しています。 |
---|