これまで改善活動の3要素QCDの中のQとCについて解説しました。
今回は3つ目のD:Delivery(納期)がテーマです。
「指定された納期通りに作業を完了させる」ための進捗管理手法をご紹介します。
目次
-
- ・作業進捗に応じて要員数を柔軟に変更
- ・進捗を管理すると生産性も改善
2. 2つの進捗管理
- ・目で見る進捗管理
- ・ITを活用した進捗管理
3. 進捗状況は現場全体で共有
4. まとめ
コラムのポイント
- ・今さら聞けない、進捗管理の必要性や目的
- ・進捗状況が一目で分かる確認方法
- ・現場全体に進捗状況を共有する重要性
物流現場における進捗管理とは
「今日は残業が何時間も発生してしまった」「業務終了間際になっても作業が終わらない」といった問題が発生したことはありませんか?
このような事態が発生するのは、作業進捗状況のチェック機能が存在しないためです。物流センターは、指定された納期通りに作業を終えることが求められています。
しかし、納期直前に作業遅延が発覚したためにリカバリーが困難となるケースもあります。そのため物流現場管理者は、納期遵守のため定期的に進捗状況をチェックする必要があります。
作業進捗に応じて要員数を柔軟に変更
物流センターの入荷量・出荷量は月や曜日によって変動します。
その作業量に応じて作業員を不足なく配置できれば、作業遅延を防ぐことができます。
しかし午前は入荷、午後は出荷が多いなど、1日の中でも時間帯によってどの作業に何人必要となるか変化します。また「入荷量がいつもより多い」「急な出荷依頼が入った」などのイレギュラーが発生し、必要人数が変わることもあります。
そのため要員数を固定するのではなく、「どの作業に余裕があるか」「どの作業が遅延しているか」を管理者が定期的に確認し、それに合わせて再配置すると良いでしょう。
状況に応じた柔軟な変更は高度なスキルが求められますが、現場管理者の腕の見せ所でもあります。
進捗を管理すると生産性も改善
進捗状況に応じた作業者の再配置を継続していくと生産性も向上します。
8話※で解説しましたが、作業量が増減しても要員数が固定式になっている場合、必要以上の要員を投入すれば余裕が生まれて生産性の低下を招き、反対に少なければ残業が発生し、納期通りに終了できないこともあります。
進捗管理をすることは、作業の遅延や未完了を撲滅すると同時に、生産性の改善にも貢献します。
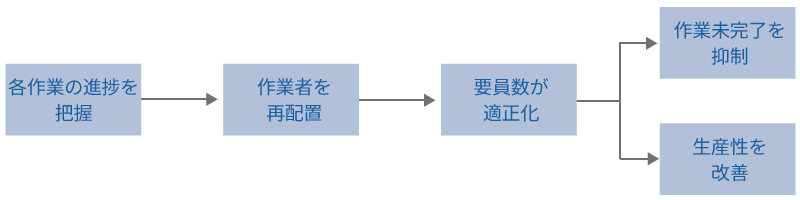
※第8話「生産性管理のキホン」はこちら
2つの進捗管理
前述の通り、物流現場では時間帯によって主体となる業務が変わります。
-
一般的な例
- ・入荷業務は午前中に集中することが多く、午後は余裕が生まれやすい
- ・出荷業務のスタート時は出荷検品や梱包作業は少なく、ピッキング作業が主体になる
- ・出荷指示を1日に何度も受信する場合、受信の前後はピッキング作業に余裕が生まれやすい
- ・夕方、運送会社に荷物を引き渡す時間帯は、出荷検品や梱包作業が慌ただしくなる
時間帯ごとに各作業に必要な要員数が変化していくため、現場管理者は作業者を柔軟に割り振っていくことが求められます。具体的には、進捗が良い作業チームから悪いチームへ作業者をシフトさせます。
では、各作業の進捗状況はどのように把握すればよいのでしょうか。当社の事例をご紹介します。
目で見る進捗管理
当日の物量を前日に把握できれば、進捗状況の管理は実に簡単なことです。
しかし一部の仕入先・届け先を除いたほとんどの場合において、当日の物量全体を掴むのは容易ではありません。
そのため、まずは把握できている作業量のうち、あとどれぐらい残っているかを把握することからお勧めします。パレット数や指示書の枚数、カゴの数などを定期的にチェックすることで、残りの作業量がおおよそ推測できます。
-
例:入荷作業
- ・入荷作業:荷受場所に仮置きしているパレット数
- ・格納作業:入荷処理済の札が貼付されたパレット数
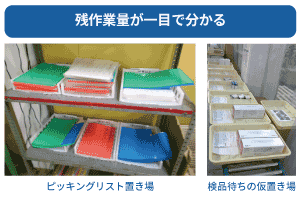
-
例:出荷作業
- ・ピッキング作業:ピッキングリスト置き場に残っている作業指示書の枚数
- ・出荷検品・梱包作業:検品や梱包待ちの仮置き場に置かれているカゴの数
ITを活用した進捗管理
当社では進捗状況を把握するために、WMS(倉庫管理システム)の情報を活用しています。
WMSにはハンディターミナルを介して様々な作業情報が集まるため、業務別にリアルタイムで詳細な進捗状況を把握することができます。
対象作業と活用する情報
- ・入荷:入荷予定情報と入荷実績情報との差分
- ・格納:入荷実績情報と格納実績情報との差分
- ・ピッキング:ピッキング指示情報とピッキング実績情報との差分
- ・検品:ピッキング実績情報と検品実績情報との差分
作業の予定情報と実績情報との差分をもとに、リアルタイムな進捗率と残作業量が確認できます。
また、出荷に関する進捗状況は運送会社別でも管理すると良いでしょう。運送会社の集荷時間を意識した進捗管理によって、「集荷に間に合わない」を防ぐことができます。
またITを活用することは、物流現場で飛び交う「イレギュラーな依頼」の管理にも有効です。
物流現場には「緊急出荷して欲しい」などの突発的な依頼や、在庫・輸送に関する問合せが頻繁に入ります。日々通常業務に追われながら対応していると、どうしても漏れ・遅れ・忘れが発生しやすくなります。
そこで、タスク管理ツールを活用して依頼の内容と進捗状況を管理します。1つの依頼を完了させるには多くのプレイヤーが関わり、たくさんの伝言リレーが発生するため、ITの特性である情報のリアルタイム性と一元性の効果が存分に発揮されます。
※イレギュラーな依頼の管理手法については、こちら
進捗状況は現場全体で共有
進捗状況は、ホワイトボードやモニターを活用して現場に掲示しましょう。
皆が見るような目立つ場所に掲示することで、作業遅延を発見しやすくなります。
また、管理者に加えて作業者も進捗状況を気にするようになり、遅延や残りの作業量に対する意識が高まります。
当社では、写真のように大型モニターで進捗を可視化しています。
短時間で自動更新するためリアルタイム性が高く、WMSの情報をそのまま活用しているのでコストも抑えられます。
WEBで情報共有できるので、例えば出張先やテレワークでも作業遅延に気づけるので、たとえ「現場」にいなくても状況判断やリカバリーの指示ができるようになります。
ホワイトボードや管内放送などアナログな可視化であれば今すぐ実践でき、加えてITを活用した場合はリアルタイム性や管理精度が格段に向上します。
自社に適している方で構いませんので、ぜひ一度お試しください。
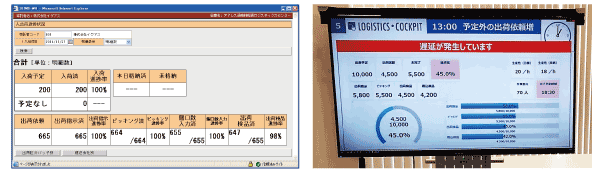
まとめ
物流センターは、指定された納期通りに作業を完了させることが求められています。
遅延なく作業が完了するよう、現場管理者は作業の進捗状況を把握する必要があります。
しかし1日の中でも、時間帯や業務内容、イレギュラーの発生などにより計画通りの要員数にならないことがあります。各作業の進捗状況を定期的に確認し、遅延に対して作業員を再配置できるようにしましょう。
進捗状況は、以下のような方法で把握できます。
- ・目で見る管理:パレットや指示書、カゴの数を定期的にチェックすることで残作業量を把握
- ・ITを活用した進捗管理:作業の予定情報と実績情報との差分から、現状の進捗率と残作業量を把握
また、進捗状況はホワイトボードや大型モニターを活用して現場に掲示しましょう。
遅延の早期発見と同時に、作業員の意識が高まり「可視化するだけで効率化」されるようになります。
このような改善活動の過程で得られた数値は、継続的に記録し評価することを併せてお勧めします。
現場管理者には数値の変化を読み取り、課題を早期に改善し、取組みを正しく評価することが求められています。
物流センターの改善活動に終わりはありません。
即実践しやすいものから始めてみてはいかがでしょうか。