前回は、改善活動の3要素QCDの中のQ:Quality(品質)について解説しました。
引き続いて、今回はC:Cost(コスト)を取り上げます。
このコラムでは、特に大きな比率を占めると言われている作業人件費にテーマを絞って解説します。
目次
- ・なぜ生産性の改善が有効なのか
- ・2つのアプローチ方法
- ・業務プロセスと作業ルールの設計で現場を止めない
- ・リカバリー処理は管理者が責任をもって行う
3. まとめ
コラムのポイント
- ・生産性を改善するメリット
- ・早く始めて効果を実感しやすいアプローチ方法
- ・取り組み事例の紹介
コスト適正化のための生産性管理
なぜ生産性の改善が有効なのか
物流センターにおけるC(Cost:コスト)の改善のためには、生産性管理の強化がとても有効です。
その理由は、2つです。
・得られるメリットが大きい
物流センターのコストは、主に建物の賃貸料、マテハンやシステムなどの設備費、そして作業人件費で構成されます。
作業の内容によっては若干差異が生じますが、作業人件費は大きな比率を占めると言われています。
比率の大きい費目を改善すること、加えて生産性管理は作業人件費の増減に直結することから、より大きなメリットが得られます。
・投資や賃金改定に比べて推進しやすい
作業人件費は、「人件費単価」×「1回あたり作業時間」×「作業回数」に因数分解できます。
そのうち「人件費単価」は、労働人口の減少や最低賃金の引上げ、働き方改革などを背景に今後も高騰することが予測されます。
また入出荷などに代表される「作業回数」は、仕入・生産・販売方法・在庫の持ち方などに影響を受けやすいため、物流センター単独の改善活動としては少々ハードルが高いと言えます。
それに対して「1回あたりの作業時間」、つまり「作業生産性」は物流センターにおける様々な工夫によって、早期の効果が得られます。
以上の観点から生産性管理には是非、取り組んでいただきたいと思います。
2つのアプローチ方法
生産性管理と言えば、「現状を可視化・分析して生産性を向上」させるデータ型のアプローチ方法がよく紹介されます。
しかし、分析のためにはデータの加工が必要となり、それ以前に正しいデータを大量に収集することが求められます。
またWMS(倉庫管理システム)で可視化できる作業は限られており、生産性管理が思ったように進まない、という声も聞きます。
直ぐに始められて、早期に効果を実感できるアプローチ方法をお探しなら、業務プロセスや作業ルールの見直しから始めてみてはいかがでしょうか。例えば、イレギュラー発生時などは、その対応方法が細かく決められていないことが多く注意が必要です。
イレギュラー発生時の対応方法を改善し生産性低下を防止
出荷前の最終検品者がピッキングミスを発見した場合、各作業者はどのような行動を取りますか?
ピッキング時に、商品の不具合や在庫差異を発見した場合はどうでしょうか?
これらのように、イレギュラーが発生した場合の対応方法がマニュアル化されていない物流現場では、作業者が集まって相談したり管理者を探しまわったりするため、作業が一時的に止まってしまいます。
物流現場は流れ作業で動いており、一旦現場が止まってしまうとトップスピードに戻るのにしばらく時間がかかります。そしてその間、生産性が低い状態が続いてしまいます。
業務プロセスと作業ルールの設計で現場を止めない
当社の物流現場では、作業者がイレギュラーを発見した場合は、その作業は一旦中止し別の作業に取り掛かるようルールを定めています。
例えば、出荷検品中にピッキングミスを発見した場合、該当商品を「ピッキングミス仮置き場」に移動させます。
その後、作業者は次の検品作業に着手します。
ピッキング時に商品不良を発見した場合も、作業者は該当商品を「ピッキングイレギュラー仮置き場」に移動させ、次のピッキング作業に着手します。
このようにルールを定めて対処することにより、作業者の手は止まらず、生産性が低下することはありません。
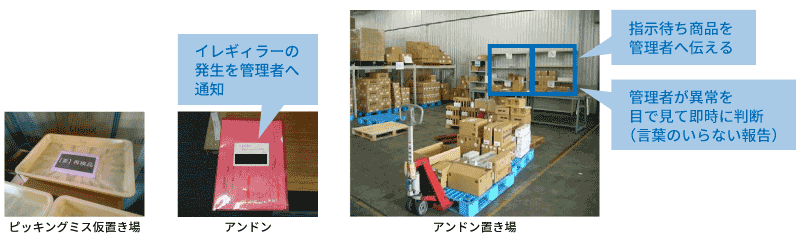
図1:仮置き場
リカバリー処理は管理者が責任をもって行う
第6話(日次の品質管理)でも触れましたが、仮置き場のチェックは現場管理者の役割の1つです。事前に設定された仮置き場を定期的にチェックし、イレギュラーの有無を確認します。
※品質管理における管理者の役割は第6話(日次の品質管理)を参照ください。
仮置き場に商品があれば、管理者が責任をもって最後まで対処します。イレギュラーへの対応は物流現場ではつきものですが、そのリカバリー方法を間違えてしまうと後々大きな問題に発展するケースもあるため、管理者による正しい対処が求められます。
当社の物流現場においても、以下のようなケースがありました。
出荷検品者がピッキングミスを発見しました。
10個ピッキングすべきところを、1つ多く11個ピッキングされていたため、出荷検品者は余分にピッキングされた1個を元の保管場所へ戻しに行きました。
ところがその時、酷似した別の商品の保管場所に誤って戻してしまいました。
その後、商品の混在に気付かずに別の作業者にピッキングされ、届け先へ間違った商品が出荷されてしまいました。
通常の流れでは、バーコードリーダーを使って商品の間違いをチェックするプロセスがあります。
しかし、イレギュラー発生時のリカバリー処理は、システムでカバーできないケースが多々あります。そのため、二次災害を防止するためにも、当社の物流現場では管理者自身が責任を持って処理するプロセスにしているのです。
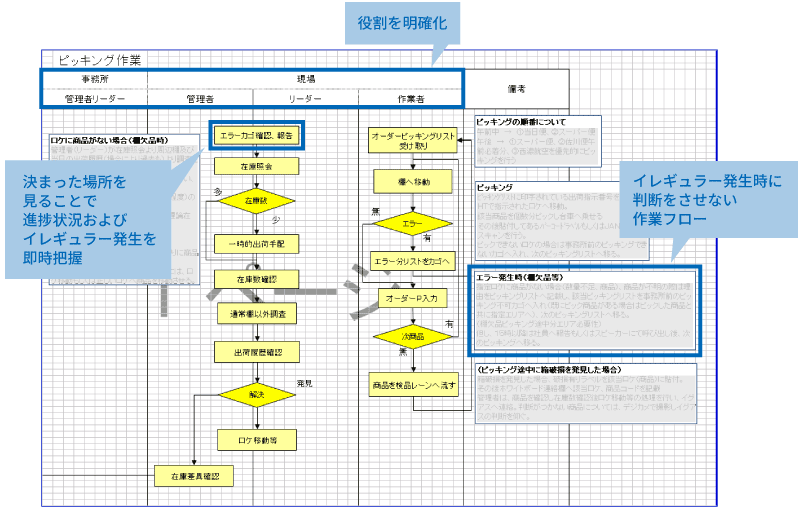
図2:物流現場管理者の役割を意識した業務フロー
まとめ
物流センターのコスト改善には、生産性管理を強化されてはいかがでしょうか。
あらためて、その理由は2つあります。
- ・得られるメリットが大きい:生産性が改善すればコスト比率の大きい人件費の削減が可能
- ・投資や賃金改定に比べて推進しやすい:生産性向上は物流センター単独で取り組める上に、新規の投資や賃金改定と違い工夫によって即実践できる改善活動
その中でも、直ぐに始められて早期の効果を期待される方は、イレギュラー発生時の業務プロセスや作業ルールの見直しをお勧めします。
- ・ルールを定めることで現場が止まること(生産性の低下)を防ぐ
- ・イレギュラー発生時は「仮置き場に置く」など、すぐ別の作業に取りかかれる業務プロセスへ変更する
- ・商品チェックや保管などのリカバリー処理は、二次災害を防止する意味でも管理者が責任を持って対処する
このようにイレギュラーに対し、迅速かつ適切に処理するだけでも生産性の低下を防ぐことができます。
イレギュラー発生時の業務プロセスや作業ルールの徹底は意外と見落とされがちです。
今一度現状を振り返り、活動してみてはいかがでしょうか。