こんにちは。物流アウトソーシングサービス「物流業務クラウド」を提供するセイノー情報サービスです。
物流はアウトソーシングの割合が高く、業務内容がブラックボックス化しやすい傾向にあります。特に大手企業は物流拠点が点在し、顧客や商品数に加えて取引する物流事業者も多く、現場運用を把握しきれない状況に陥ってしまいがちです。しかしそのままにしておくと業務が止まったり物流品質の低下を招く恐れがあるため、早急に解決すべき課題です。
当コラムではブラックボックス化を解消するメリットや取り組む際のポイントについて、事例をまじえて分かりやすく解説します。
目次
改善活動の落とし穴「ブラックボックス化」とは
ブラックボックス化とは、「業務が属人化して何がどうなっているのか担当者しか分からない」状態を指します。
他部門はもちろん同じ部署でも他の担当者がどうやってその業務を行っているのか、判断基準は何か、正しい結果が得られているか分からなくなります。
属人化によるブラックボックス化は専門性の高い知識やノウハウ、それらを培うための経験を必要とする業務でよく起こります。複雑な業務であるが故にシステム化が難しく、担当者固有のExcelで管理していることも少なくありません。
また業務をアウトソースしている場合もブラックボックス化する傾向にあります。
自社で運用する場合と比べると、現場で起きている詳細な情報が得られないことや、実業務から離れることで知識が減り、ノウハウが蓄積されなくなることが原因です。マニュアルや管理システムを提供していても、万が一イレギュラーが発生した際にどう対応したらよいかなど、素早く適切な判断ができなくなります。
ブラックボックス化のデメリット
業務がブラックボックス化していると、様々なデメリットがあります。
例えば、自社による改善活動が行えなくなります。業務がどう行なわれているのか、現在の状態は適切なのかが分からなければ、改善すべき点を見つける事も改善策を検討することもできません。
また該当業務を本人しかできない状況が続くと、担当者の精神的な負担は大きく会社としても業務が停止するリスクを抱えることになります。また、担当者を異動させたりアウトソース先を変更したりすると、物流品質が低下する恐れもあります。このようにブラックボックス化は企業にとって大きなリスクをはらむ、早急に解決すべき課題と言えます。
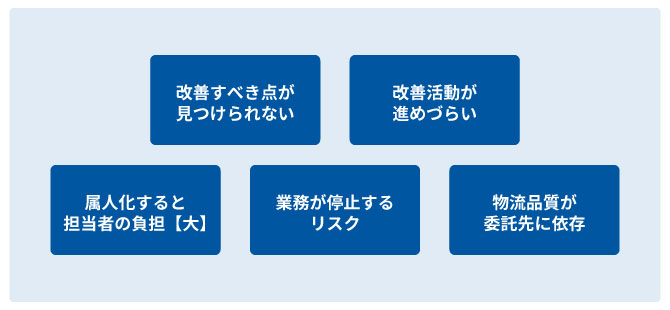
大手企業ほどブラックボックス化が起こりやすい
事業規模が大きくなるほど、現場運用がブラックボックス化しやすくなります。
物流拠点や顧客、商品数が多い場合は、商品特性や拠点ごとに管理方法・使用するシステムが異なることもあるため、物流部が現場運用を把握しきれない状況に陥ります。また庫内業務や輸送など業務を委託していることも多く、実運用が見えづらくなります。結果、委託先から「この作業には5名の作業者が必要、これ以上の削減はできない」という主張があった場合は、それを受け入れるしかなくコスト削減や改善活動が思ったように進まないことがあります。
ブラックボックス化の原因はシステムにも潜んでいます。
先の通り大手企業の物流部は現場から縁遠くなるため、データを通して現状を把握することになります。「業務をアウトソースしているがWMSは自社で準備し物流データを自由に活用できるようにしている」企業が増えたものの「データが様々なシステムに点在」していれば決して活用しやすい環境になっているとは言えません。拠点や商品によって異なるWMSを使用していたり、工場から各物流拠点への在庫補充など「WMSにも基幹システムにも入れられない」業務を担当者固有のExcelで行っていたりしないでしょうか。
データはあるがそこから現状を読み解くことができない、どこにどんなデータがあるのかも把握していない、データをつなげられず社内サプライチェーンを可視化できない、などデータ観点にも「ブラックボックス化」は起こっているのです。
関連コラム:大手企業のアウトソーシングによる「ノウハウ消失への対応策」を紹介
・
物流環境の変化
ブラックボックス化を解消するメリット
ブラックボックス化を解消することで、様々なメリットが得られます。
- ・今まで見えていなかった課題が顕在化する
- ・認識の統一や情報共有がしやすい
- ・営業や製造、調達など他部門との協力体制が構築しやすい
- ・全体をつなげて考えることができるため、全体最適化しやすい
改善に向けて他部門に協力して欲しいことがあっても、データ化されていないと「根拠」がないため話が伝わりません。「営業の依頼により貸切便で配送しているが、物流コスト削減の観点から特別積み合わせ便に切り替えたい」という案を考えても、「毎月大きな売上が上がっている顧客だから変更できない」と言われてしまいます。
しかしブラックボックス化が解消され物流部で運用とデータが把握できるようになれば、顧客ごとの売上高物流コスト比率や利益率を算出できるようになります。「物流コスト比率が高く実は利益率が低い」という事実を数字で示すことで、物流と営業部門が問題点を共有でき改善に着手することができます。
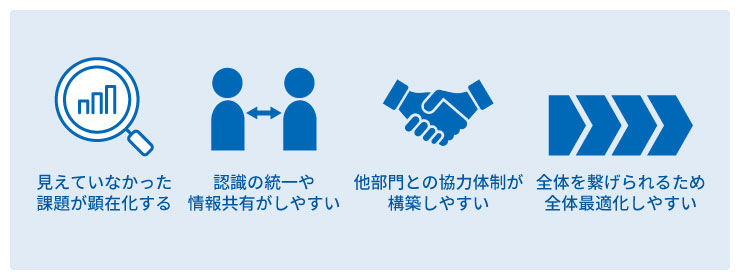
ブラックボックス化を解消するためのポイント
ブラックボックス化の解消に向けた活動の第一歩は「ルール化」と「可視化」です。
どのような観点で取り組むと良いのか、ポイントを3つ紹介します。
ルールを明確化する
まずは業務ルールをきちんと決め、共有しやすいようまとめましょう。特に判断軸はとても重要です。
判断に迷った際の「根拠」が明確になれば、誰でも一定レベルで業務が行えるようになり、作業の精度や効率の底上げにつながります。代理対応も可能になるため業務停止へのリスク対策にもなり、担当者の精神的な負荷を軽減する効果が期待できるほか、後継者も育成しやすくなります。
情報の共有・活用方法を決める
委託先、担当者、他部門との情報の共有・活用方法も明確化しておくべきです。
必要な情報の種類・内容、取得する経路やタイミング、共有方法、そしてどこを見てどんな事を読み取るのか、など熟練者のノウハウを参考にして取り決めます。
当たり前のように思えますが、実は徹底できていないことがしばしばあります。例えば「イレギュラー出荷」の依頼方法や、誰から誰に連絡・報告を入れるのか、どんな情報を渡すべきかがルール化されている企業は多くありません。依頼方法をルール化し、どう対応すべきか周知しておけば発生時の混乱や対応の属人化を防げます。また、依頼を一覧化してまとめておくのもポイントです。生産性が低下した原因を探るときなど、後々に問題点を把握することもできます。
取り決めた事を定期的に見直す
改善活動の基本である「定期的な見直し」は、ブラックボックス化の解消においても大切です。
取り決めたルールが遵守されているか確認し、徹底されていなければ再度周知します。会社方針や市場の変化によって取り決めた内容が陳腐化していればルールを見直しましょう。現場ではいつの間にか「個別対応」が増えたり、マニュアルとは違う作業方法をしていることがあります。実際にどのように作業されているのか定期的に確認することで、マニュアルに記載されている内容と実運用が乖離することを防ぎます。
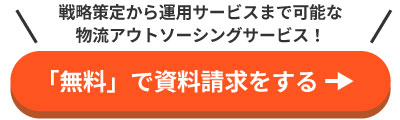
ブラックボックス化を解消した事例
取組みのポイントを3つご紹介しましたが、物流のブラックボックス化は意外なところに落とし穴が潜んでいるため解決が難しい課題でもあります。そもそもブラックボックス化していることに気づけていない場合も少なくありません。
そこでここからは事例をベースに解説します。「この業務、うちの会社はどうなっていたかな」と思い起こしながら読んでいただくと、解決策のヒントが見つかるかも知れません。
事例(1)工場から物流拠点への在庫補充
工場(生産部門)で製造された商品は、届け先への出荷に備えて各物流拠点に送られています。
物流拠点への在庫補充が工場の判断でプッシュ式に行われている企業では、生産部門の在庫(補充)計画担当者がどの拠点へ、いつ、どの商品を、いくつ送るのかを決めます。どちらかというと特殊な業務なため、システム化するほどではなく担当者固有のExcelで計画が立てられていることが多いでしょう。
このような在庫(補充)計画業務のブラックボックス化を解消するには、「情報の共有・活用方法を決める」ことがポイントになります。ある企業では、各拠点からの出荷予定(いつ・何が・いくつ必要になるのか)を工場の在庫(補充)計画担当者に共有し、それを各拠点の在庫情報と紐づけて可視化することで適切な配置配分ができるようになりました。
関連コラム:
在庫補充業務をブラックボックス化させないためのポイント
事例(2)物流コストの一元管理
「運送事業者から請求書が届くと、事務担当者が送り状をめくりながら請求内容が正しいか確認している」
「倉庫作業の委託先から請求書が届いても、妥当性のチェックができないのでそのまま支払っている」
WMSをリプレースする際にコスト管理システムも検討し、「物流コストが見えない」状態を改善する企業が増えています。ある大手企業は自社でコストを計算して委託先にデータを共有し、委託先がそのデータをもとに請求書を作成するようシステムと運用ルールを改修することで請求書チェックの手間を省くことに成功しています。
物流事業者の取り組み事例もあります。請求金額の計算が担当者固有のExcelやAccessで行われていましたが、ルール化・システム化を進めて請求業務のブラックボックス化を解消しました。様々な切り口による利益率も算出しやすくなり、改善に向けた施策立案のスピードアップが図れています。
関連コラム:
物流コストの可視化とは?取組みのポイントや重要性を解説
事例(3)輸送手配の最適化
「一番安い運送事業者を選択することで輸送費を下げたい」という話をよくお聞きします。
多くの場合、運送事業者の選定は顧客ごとや送り先住所によってある程度固定化されていますが、コストの観点から見ると改善余地があります。
例えば「5個口までは○○運送の方が安いが、それ以上だと△△運送の重量建てタリフの方が安く運べる」ことが可視化され、運送事業者を選択できるようになれば輸送費が削減できます。2024年問題などにより輸送費の高騰が懸念されていますので、輸送手配の最適化はより重要になってくるでしょう。
事例(4)出荷計画(作業のプランニング)
お客様からの受注情報をそのまま出荷指示としてWMS(倉庫管理システム)へ連携していませんか。
連携した受注情報全てを当日に作業組みしてしまうと現場に無理が生じます。センター長やリーダーが作業支援に入り残業することにもなれば人件費が上昇し、結局「改善に取り組んでいるものの、なぜか思うように成果が出ない」結果を招くことになります。
現場が作業しやすいよう「出荷依頼データは正確かつ迅速に処理」する必要があります。どこの拠点から出荷すべきか、いつ作業すべきか、どの運送事業者で運ぶべきかなど、作業のプランニングをすることで現場の生産性向上やコスト削減につながります。もし既にプランニングできていたとしてもExcel等で属人的に対応されている場合は、会社のノウハウとして蓄積できるようマニュアル化しておくことをお勧めします。
関連事例:WMS・LMSで出荷計画をシステム化
・
株式会社テクノアソシエ「WMS・LMSの活用で現物主義・標準化・可視化を実現」
まとめ
ブラックボックス化とは、「業務が属人化して何がどうなっているのか担当者しか分からない」状態であり、最悪の場合は業務が停止することもあり企業にとって大きなリスクをはらむ早急に解決すべき課題です。
しかし「ルール化」と「可視化」を進めることで、ブラックボックス化を解消することができます。運用ルールや情報の共有・活用方法をきちんと決め、共有しやすいようマニュアルなどの形でまとめましょう。取り決めた内容を定期的に見直すことで、現場と実運用が乖離することを防ぎます。
物流のブラックボックス化は意外なところに落とし穴が潜んでいるため解決が難しいのですが、事例を参考に「この業務、うちの会社はどうなっていたかな」と検討いただくことで解決策のヒントが発見できるかもしれません。
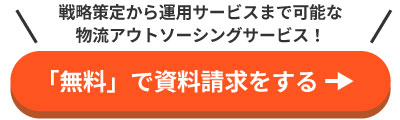
このコラムの監修者![]() |
セイノー情報サービスは400社以上へのWMS導入を通して培った物流ノウハウをもとに、お客様の戦略立案や物流改善をご支援しています。 当コラムは、経験豊富なコンサルタントやロジスティクス経営士・物流技術管理士などの資格を持った社員が監修しています。 |
---|