導入ソリューション
- 倉庫管理
- 統合物流管理
-
-
- 企業名
- 株式会社テクノアソシエ
- カテゴリ
- 倉庫管理(WMS)
- 企業規模
- 連結1,768名(2024年3月現在)
- 業種
- 卸売業
- 売上高
- 連結96,349百万円(2024年3月期) 事業内容 鋲螺類、加工品、金属素材、電材品、化成品、産業機器、その他販売及び、これに付帯または関連する事業
お客様の概要
株式会社テクノアソシエ様は、1946年の会社設立以来、鋲螺・金属加工品・化成品をはじめ産業を支える様々な部材・機構部品を商材として扱う住友電工グループの会社です。お客様のご要望(Needs)と仕入先・協力会社様がもつ各種の技術や製品(Seeds)を的確に引き合わせ、デザイン・試作・量産・保守まで一貫したサービスを提供することが強みです。
同社は、事業精神「心と心の絆」を基本に掲げ、お客様のニーズにきめ細やかに対応する「価値(Value)創造企業」として産業の変革に対応し、持続可能な社会の実現に貢献されています。
今回は社内で立ち上がった新システム構築委員会と物流改革プロジェクトをきっかけに、物流業務の効率化や標準化などを目的として弊社WMS「SLIMS」と統合物流管理システム「LMS」を導入いただきました。
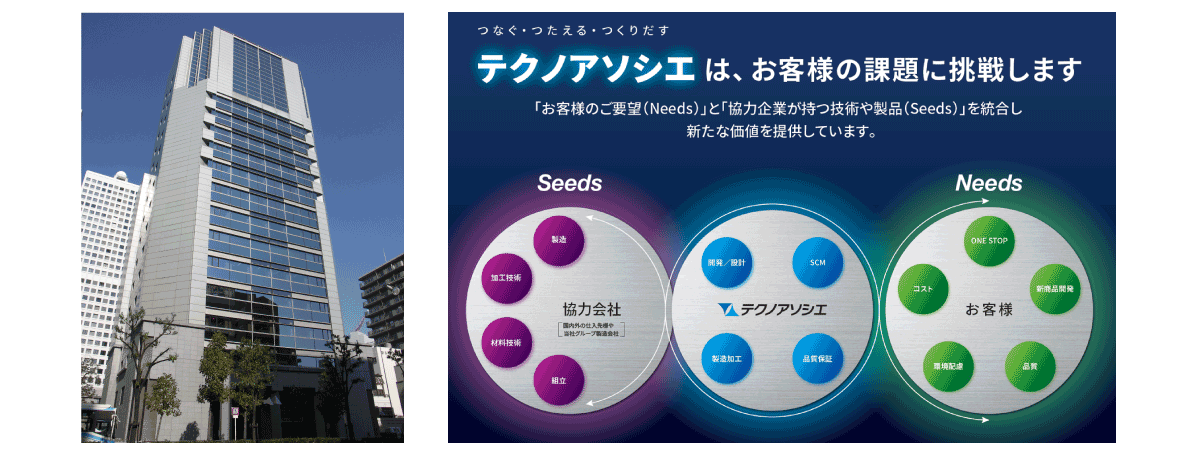
業務課題とシステム検討までの経緯
テクノアソシエ様では、販売管理システムと物流システムの老朽化を理由としてリプレースプロジェクトが発足されました。「新システム構築委員会 物流分科会(物流部メンバーが参画)」で検討・設定された新しいシステム・運用のコンセプトは「現物主義・標準化・可視化」の3つです。
新物流システムのコンセプト
■現物主義
既存システムでは現物在庫の移動と伝票処理のタイムラグによって、自社倉庫で保管している実際の在庫数とシステム上の在庫数に差異が生じることがありました。新システムでは管理対象を自社倉庫に限定し「現物主義」化し、さらに現物在庫を移動させる際にはシステムからの指示を必須とすることで、在庫管理の精度を向上させます。また、ロケーション別在庫管理とシステムによる在庫引き当てを導入することで「保管棚に行ったら在庫が無かった」という作業ロスを無くし効率化も目指します。
■標準化
同社の物流現場では得意先ごとに固定の作業者が選任されていました。得意先ごとにきめ細かな対応ができるものの、個別の運用が随所に存在しており属人化を生み出す原因にもなります。新システムでは得意先の要望に応えるための一部工程における個別運用は残しつつ、大幅な業務の標準化を目標にしました。
■可視化
同社では作業計画(いつ・どの出荷作業を行うか)を作業者に任せていたため、管理者による状況把握やマネジメントが行いづらい状態でした。新システムでは出荷の作業計画をシステムで立案することで、締め切り単位の作業量の可視化と、日々の作業量の平準化を目指しました。指示単位の作業状況が可視化されることで、トレーサビリティの確立と問題発生時のスピーディーな対処も実現します。
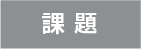
- ・従来からの仕組みでは在庫引き当てが難しく、それに関連し作業ロスも発生
- ・作業計画から実際の作業までの全工程が作業者に一任されており、管理者の目が行き届かない
- ・作業者ごとの工夫が多く取り入れられ属人化しているため、他者による作業支援が困難
- ・欠品などイレギュラーが発生した際は、各作業者から購買権を持つ営業部門へ直接の報告・交渉が発生
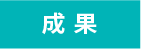
- ・在庫移動時にシステムからの指示が必須となったことで、現物在庫とシステム在庫数が一致
- ・引当機能をシステムで実装し在庫の「現物主義」を実現、作業ロスが激減し効率がアップ
- ・作業計画と進捗状況が可視化され、応援者の手配など管理者によるコントロールが可能
- ・欠品連絡が自動化され、購買権を持つ営業部門と倉庫間のコミュニケーション効率が向上
新システムの選定と導入までの過程
もともとはスクラッチ開発の前提でプロジェクトが進行していましたが、新システム導入までの時間的コストを抑えるため、パッケージシステム導入の可能性を模索することになりました。
多くのベンダーから資料が取り寄せられ、4社との面談を経て最終候補が弊社を含めた2社に絞り込まれました。
検討のカギは同社独自の運用とシステムの適合性
標準化を進めつつも、同社の強みである「得意先の要望に応えるきめ細かな対応」を無くさないことがシステム・ベンダーに求められました。しかし最終候補の1社は「現行の管理・運用方法を大きく変えなければ、システムの導入は難しい」と提案していたこともあり、同社内でパッケージ型WMSへの懸念が強まってしまいました。そこで弊社は長年の改善経験を持つメンバーが何度も現場へ足を運び、同社物流部との対話を重ねました。その結果、独自の運用にもパッケージ型WMSで対応できる可能性が高いのではないか、と懸念を払しょくでき、弊社WMS「SLIMS」が採択されました。
この検討過程においては、プロジェクトの成功を願いつつ双方の遠慮のない意見のぶつけ合いが功を奏したことも成功要因と伺っています。このように信頼関係を構築できたことも高く評価いただけた理由の1つです。
新コンセプトを継続的に社内へ情報発信
システム導入に向けて、同社物流部は新しいシステム・運用に関する考え方を社内に浸透させるための取り組みも行っています。
例えば社内報「Runup!!」をおよそ70回も発行し、先の3つのコンセプトや新システムによって業務がどう変わるかなどが発信されました。これにより、経営層や社内の関連する部門からも標準化と同社の強み(得意先ごとのきめ細かい運用)は両立できることに対して理解を得る事ができました。
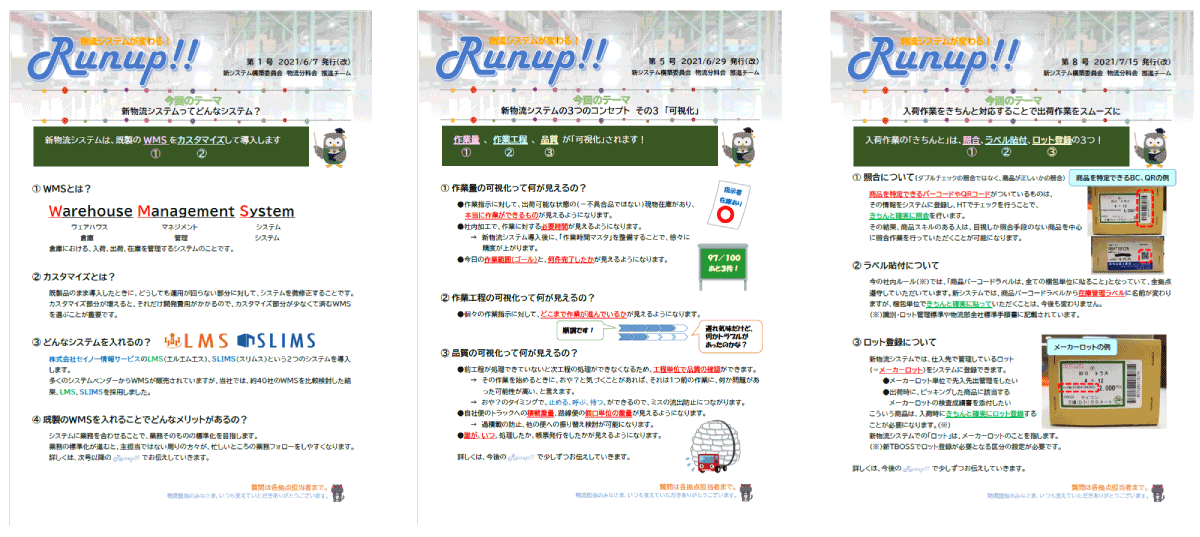
SLIMS・LMSの導入により実現した作業計画のコントロール
同社は新物流システムとして、WMS「SLIMS」とともに物流情報を統合管理できる「LMS」を導入しました。SLIMSとLMSを併用することで、作業計画のシステム化など高度な物流マネジメントを実現しています。
1.在庫の現物主義を実現
同社はSLIMS・LMSの導入を機に、在庫管理の考え方を現物主義(自社倉庫に保管している在庫を確実に管理)に切り替えています。従来は在庫の中には外部倉庫で保管しているものやメーカーへ品質確認を依頼しているものも含まれ、それが整理されずに管理されていました。しかし現在は自社倉庫の在庫を確実に管理し現物在庫数とシステム在庫数の誤差を無くすことで、高度な在庫管理を実現しています。
2.システムによる作業計画の立案と先行作業の削減
従来、作業計画(いつ・どの出荷作業を行うか)は各担当者に任されており、かなり先の日付の出荷準備まで行われていました。しかしSLIMSでの在庫引き当てが可能になったことから、現在は出荷の作業計画もシステム(LMS)で立案しています。出荷準備の前倒しは「3日先行まで」と業務ルールも統一され、当日に余分な作業をしたり、遠い出荷日の在庫を確保したりする必要性も無くなりました。
3.作業の進捗状況を可視化
作業計画のシステム化とハンディターミナルからのリアルタイムな情報収集によって、作業の進捗状況が可視化されました。
遅延しそうな作業があれば管理者が応援を指示するなどマネジメントしやすくなったため、夕方になって慌てることが無くなりました。またデジタルサイネージを用いて作業現場に進捗状況を掲示したことで、作業者のモチベーションアップにもつながっています。
4.作業効率の向上
今回のシステム導入により、様々な作業が効率化されました。
例えば棚卸作業。従来は計算機を用いて箱数や入り数から在庫数を算出し、ハンディターミナルで数量を入力していました。しかし現在は在庫管理ラベルにQRコードが付いているため、スキャンするだけで現在の在庫数入力が簡単に行えます。
また従来は欠品中の注文も作業指示書が印刷されていました。SLIMS・LMSの導入により「作業できる出荷のみ指示書が出る」「欠品中の商品が入荷されると作業者へ通知される」ように変わったことで、何度も入荷場を確認しに行くことが無くなっています。「入荷されたか見に行ったが未だ補充されていなかった」という作業ロスも起こらず、現場からは「作業の『空振り』を防ぐために行っていた『事前の在庫有無のチェック作業』が無くなった事は大きい」との声が上がっています。
5.購買権を持つ営業部門と倉庫間のコミュニケーション効率が改善
物流現場では出荷準備をかなり先の分まで前倒しで業務し、欠品が発生すれば営業部門へメールや電話で連絡していました。さらに連絡ルールは決まっておらず、対応は属人的でした。現在は在庫引き当てができなかった場合、営業部門が使用するシステムに情報が自動で送られます。メール文章を書いて配信する必要が無くなり、電話で互いの手を止める時間も短くなったことから、作業効率だけでなくコミュニケーション効率も大幅に改善されました。
全国展開に向けた導入前教育の徹底
テクノアソシエ様ではシステムの導入前に現場の管理者や作業者へ入念な教育を実施しています。
ポイントとなるのは「教育マップ」です。
教育マップとは、SLIMS・LMSの本番運用が始まる前にレクチャーすべき項目を列挙したものです。教育用のデモ画面を使い質疑応答する勉強会を実施し、抜け漏れなく導入前教育を行っていきます。
さらに勉強会では管理者・作業者の疑問点を丁寧に洗い出し一覧化しました。事前に細かく運用確認しておくことで、導入時の混乱を最小限に抑えられます。
このプロジェクトを機に制作し直したマニュアルも活躍しています。
従来からハンディターミナルによる作業はあったものの、手順などが様変わりしています。そのためマニュアルを用いて繰り返しレクチャーすることで、少しずつ運用を浸透させました。イレギュラーな処理が発生した際にもマニュアルによる運用確認が行われており、標準化を促進することに一役買っています。
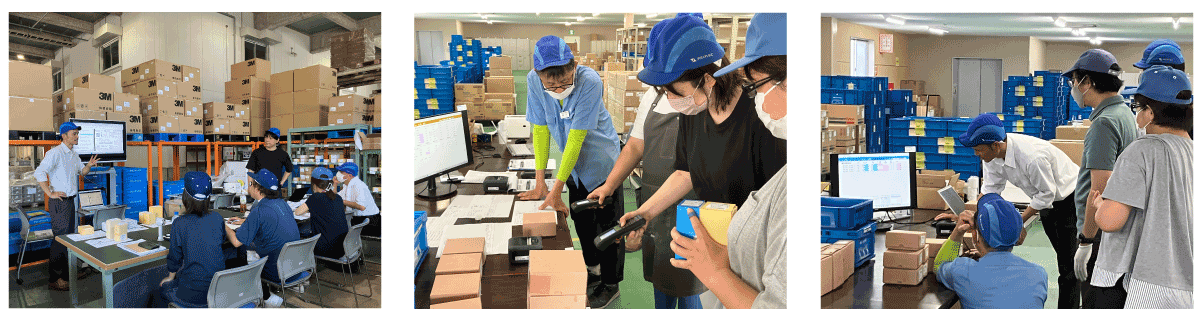
今後の展望
テクノアソシエ様は、全国19拠点へのSLIMS・LMS導入を計画されています。今後数年かけて順次導入を進め、全拠点で3つのコンセプト「現物主義・標準化・可視化」を実現していく予定です。
これらコンセプトは、物流改革が推進されていく上で大きな意味を持ちます。
例えば標準化が進めば、人手不足への対策になります。新人作業者への教育が容易になり、定着率も上がる可能性があります。さらに同社では、マテハンやロボットを活用した自動化への布石にもなると考えています。
また可視化が進めば、現場管理者の負担を減らせる可能性もあるという意見も出ています。可視化された情報をもとに本社にいながら現場の様子を把握できれば、毎日定例的に・どの拠点でも行っている業務を自動化したり、イレギュラー処理への指示を本社で代行したりできるからです。様々な業務に追われ忙しい日々を過ごす現場管理者をサポートする体制が実現すれば、物流の持続可能性が向上します。
属人化された業務の標準化・可視化は容易ではありません。しかしテクノアソシエ様は綿密な設計や計画によって1つずつ課題をクリアしていこうと、全国展開に向けて現在も日々邁進されています。
お客様の声
パッケージシステムを導入しても当社のお客様の様々なNeedsに応え続けることができるのか、決断を下すまでに紆余曲折がありましたが、セイノー情報サービス様は我々に根気よく向き合ってくださいました。
当社の運用を詳細に把握いただき、一つ一つ解決策を提案いただいたことは、大きな後押しになりました。
今までやり慣れていた作業を大きく変えることになるため、現場には大きな負担をかけることになりますが、全拠点導入を完遂した先には、当社の物流に関する課題を解決するための土台ができ上がると考えております。
今後とも良きビジネスパートナーとしてお付き合いいただきたく、よろしくお願いいたします。
物流部 次長
孝石 麻紀子 氏
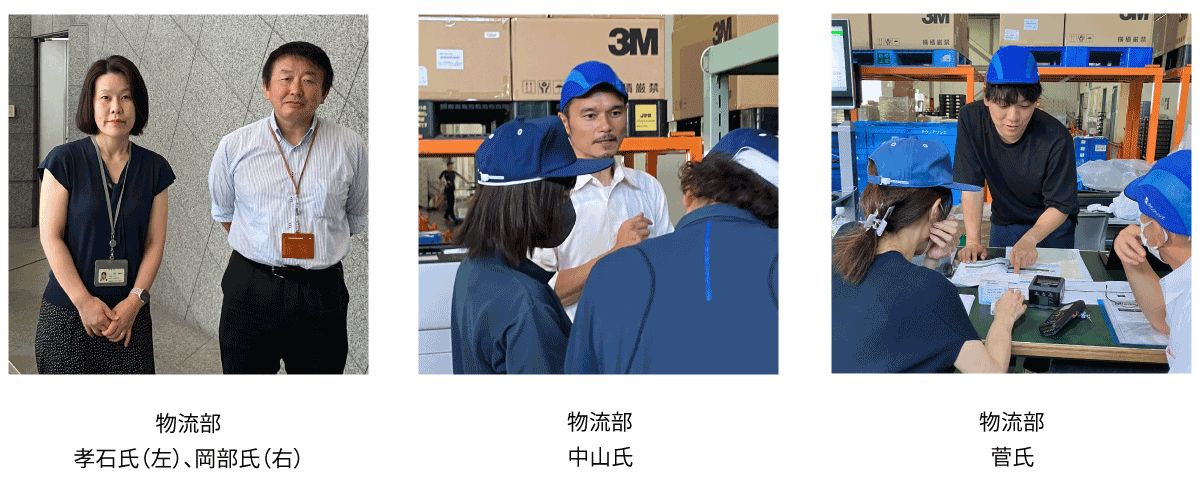