ロジスティクスPSIとは(第3回) から ロジスティクスPSIによる物流リソース適正化(第5回)までは、在庫と物流リソースの適正化ためのアプローチとして「ロジスティクスPSI」を説明してきました。今回は、ロジスティクスPSIについて、導入事例を通じて、さらに理解を深めていただこうと思います。
導入事例企業A社の概要
今回取り上げるロジスティクスPSIの導入事例企業A社は、年商400億円の日用品製造業です。取扱品目数は1000品目あり、このうち全国4箇所の工場で製造された製品は、工場併設倉庫で一時保管後、18箇所ある物流センター(在庫補充拠点)へ移送されます。そして、全国にある代理店を経由し、得意先に流通しています(図1)。 そのため、在庫計画はこれらの物流構造の中を流通する在庫の補充計画、移送計画、そして、その製品の生産計画に関係します。また、リソース計画は倉庫のキャパシティ計画や輸送計画から構成されます。
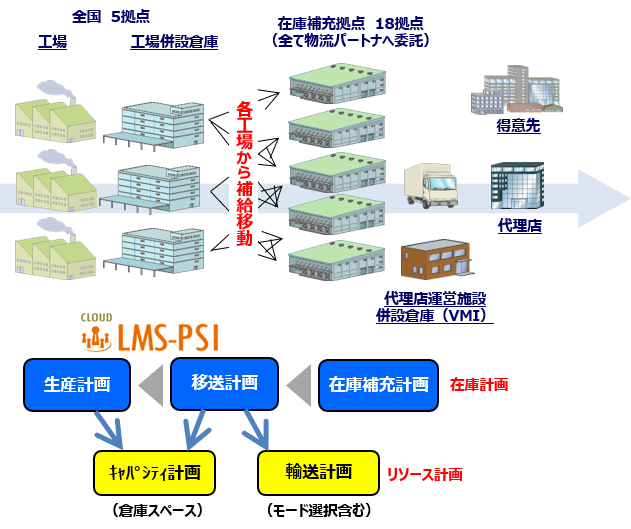
A社の取り組みテーマ
A社では、中期経営計画におけるロジスティクスへの取り組みテーマとして、「物流コストの削減」、「在庫の適正化」および「輸送手段の安定的確保」の3つを掲げておりました。これら3つのテーマを達成するために、解決すべき5つの課題を設定しました(図2)。 ご紹介する導入事例では、「物流コスト削減」をテーマに、移送計画の標準化・効率化という課題に焦点を当てています。

移送計画の標準化・効率化
在庫補充拠点への移送における計画は、つぎの2つの方式に大別できます。
- 1. PULL型各在庫補充拠点の需要量に合わせて、欠品等発生しないように工場併設倉庫から各在庫補充拠点へ移送する。
- 2. PUSH型工場で生産された製品が工場併設倉庫のキャパシティを超えた場合、工場併設倉庫から各在庫補充拠点へ移送する。
需要に合わせて生産し、在庫補充拠点へ移送する「PULL型の移送」を行えば、PUSH型の移送は発生しません。しかし、A社では製品の作り過ぎにより、PUSH型の移送が発生していました。在庫補充拠点間の移送計画が適切に行われず、無駄な横持ち輸送が発生していたのです。その理由は、移送計画を担当者レベルで行っていたからです。さらに、これらの計画業務はExcelを使った手作業で行われており、作業が属人化(配車、発注など)し、非効率でした。また計画情報は一元化されず、分散していました。 そこで、移送計画業務に弊社のソリューションSPENCER/SLASHを導入しました(図3)。
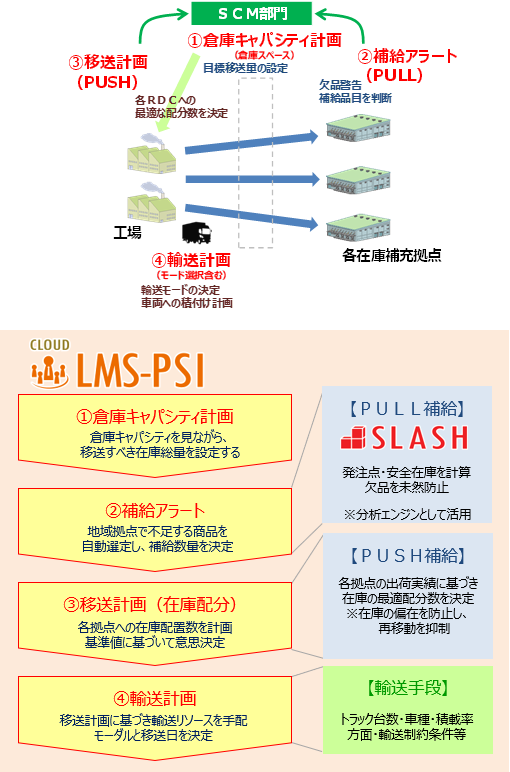
ロジスティクスPSI導入の効果
ロジスティクスPSI導入後のPULL型移送は、SLASHで安全在庫および適切な補充量・タイミングを算出し、欠品が抑制されました。そのため、移送計画の作業コストおよび在庫補充拠点への輸送コストが、合わせて1,000万円/年以上が削減されました。 また、PUSH型移送ではSPENCERで余剰在庫量の可視化を行い、在庫過多にならないよう各在庫補充拠点の補充量を導き出すことが可能になりました。加えて、SPENCERにより車両の積載率を確認し、補充予定の総量と比較することによって、移送量を調整することができるようになっています。