第3回は、在庫と物流リソースの適正化ためのアプローチとして「ロジスティクスPSI」を説明します。
PSIとは
前回も少し触れましたが、PSIは、日本では製販在庫計画とも言われる在庫管理手法です。生産管理の手法として培われ、いずれの企業でも生産や発注の意思決定に用いられる管理概念です。 ※P:生産/調達、S/販売、I:在庫の頭文字を取ったもの。
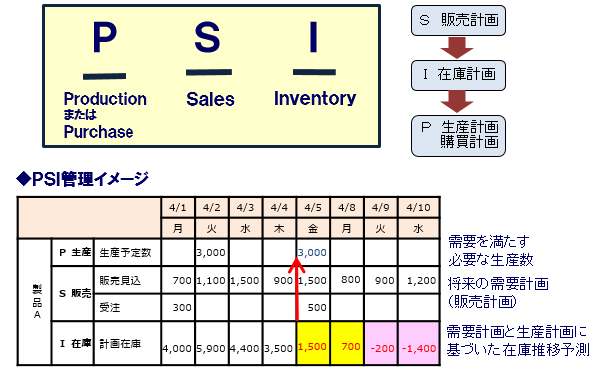
ロジスティクスPSIが狙う2つの適正化
ロジスティクスPSIは、倉庫と工場の2つの視点でロジスティクスの適正化を実現します。 倉庫には、輸送計画、物流センター作業、販売(S:Sales)計画に基づく在庫(I:Inventory)補充計画などがあります。また、工場にも生産(P:Production)計画、出荷計画、輸送計画などがあります。これらのPSI情報を1つのプラットフォームでリアルタイムに連携し、企業内サプライチェーン全体を可視化するのが、「ロジスティクスPSI」の考え方です。
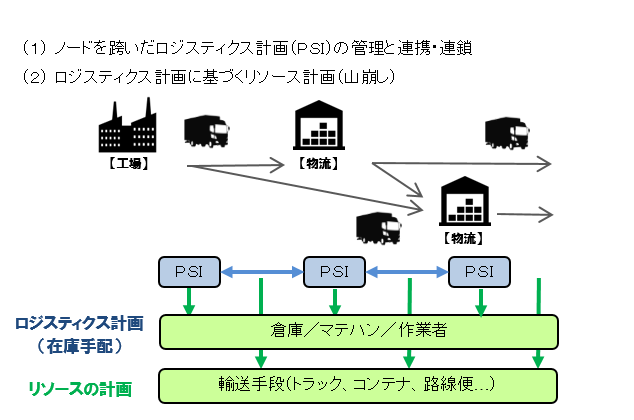
計画管理に重点を置く必要性
ロジスティクスPSIは、生産管理で培われた管理手法をロジスティクス管理に適用する考え方です。従来のロジスティクス管理は、「実行管理」に重点が置かれていましたが、リソース不足時代においては、より「計画管理」に重点を置く必要があります。
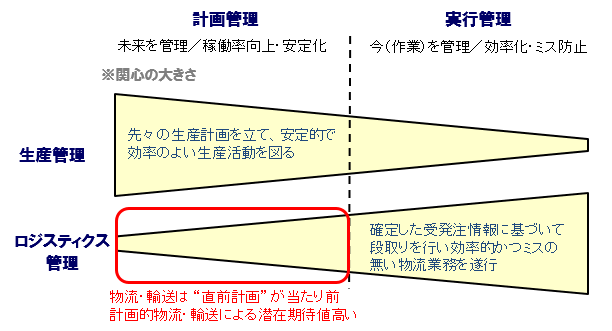
ロジスティクスPSIによる在庫の適正化
まず在庫について、市場の需要に近い営業の販売計画に基づいて、倉庫の補充量を計算します。そして、倉庫への補充=工場の出荷計画を基に生産計画を立てます。 このように「未来在庫」を全部門で共有することで、各部門が独自の基準で在庫を持つことがなくなり、適正化されます。これまでのような、川下の部門から川上の部門に情報が渡るたびに欠品を恐れて在庫を積み増すブルウィップ効果を排除できます。また、情報を共有することで、計画変更や納期調整に迅速に対応できるようになります。
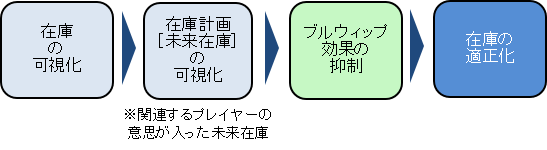
ロジスティクスPSIによる物流リソースの適正化
次に、トラックや作業員、保管スペースなどの物流リソースを最適化するには、サプライチェーン上の各企業もしくは社内の各部門がそれぞれPSI情報を保有した上で連携することが求められます。連携方法は、従来のように川上の部門から川下の部門へ情報を直前に渡すのではなく、川下から川上に一定期間の予測情報を渡すことが必要です。 例えば、当日確定した受注・出荷情報だけを運送依頼として物流会社に渡すという方法では計画性がありません。予想を超える物量がある場合は、都度、トラックや作業員を手配しなければなりません。この点で、PSI情報が連携されていれば、ピークになる日の作業を余裕がある日に山崩しすることが可能になり、物量や作業量が平準化されます。これにより、無駄な作業員の手配は不要になり、積載率や配車効率もアップすることで、物流リソースは適正化され、物流コストも削減できます。

次回は、今回示した2つのステップのうち、「在庫適正化」のステップについて展開します。