導入ソリューション
- 在庫管理
-
-
- 企業名
- 月桂冠株式会社
- カテゴリ
- 調達・生産管理
- 企業規模
- 351名(2023年4月)
- 業種
- 食品 製造業
- 売上高
- 173億円(2022年度) 事業内容 清酒・リキュール類の製造販売
お客様の概要
月桂冠様は1637年(寛永14年)創業、380年以上の歴史を誇る日本を代表する日本酒メーカーです。 明治時代には日本酒メーカー初の研究所を創設し、酒造りに科学技術を導入、醸造技術に革新をもたらすとともに事業を拡大してきました。 「品質第一」「創造革新」をモットーに、高品質な日本酒を製造・販売しています。 また日本から世界数十ヵ国に日本酒を輸出する一方、米国カリフォルニア州に米国月桂冠を設立、日本で培った四季醸造や新規醸造法などを技術移転した酒造蔵を稼働させ、 米国・カナダなど北米、南米、欧州、アジアなど各地への販売を通じて、世界に「Sake」を広めています。
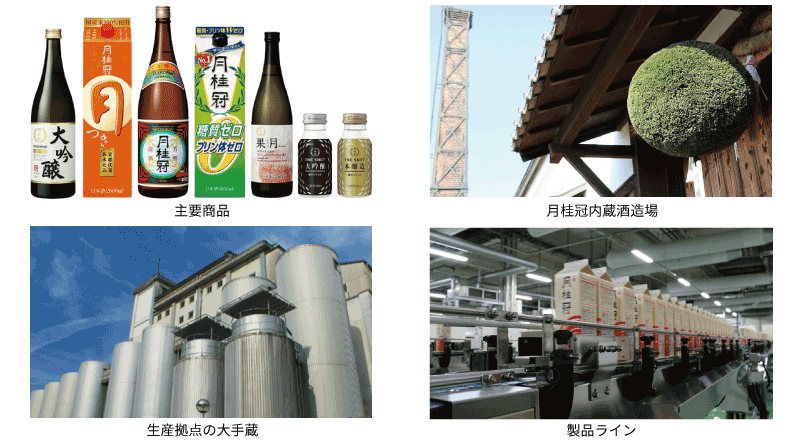
京都市伏見区に製造拠点として昭和蔵・大手蔵を構え、物流拠点は同市内の大手蔵に併設、「繁忙期8,000パレット(外部倉庫含む)、常時250アイテム以上を在庫しています。 日本酒は秋~冬にかけて出荷のピークを迎え、10月~12月には平常月と比べ約1.5倍~2倍の出荷となり、季節波動が大きいために「在庫適正化」が長年の課題でした。 季節変動に動じない在庫計画を目指しプロジェクトが発足しました。
- 課題
- ・商品特性の壁(季節変動など)
- ・組織の壁(在庫責任の所在)
- ・生産計画作業の壁(専門性がゆえの属人化)
- 成果
- ・在庫の適正化により保管キャパシティが向上
- ・発注点と安全在庫の活用で欠品が抑制
- ・生産計画立案時間の短縮(約1/8へ)
- ・生産計画業務の標準化と精度の向上
システム導入前の課題
商品特性の壁
繁忙期は出荷量が生産キャパシティを上回り、出荷ピークに合わせた生産が必要なため、高精度な生産計画に加え、原料・資材の調達、生産ラインの人員調整、保管スペースの確保など様々な準備が必要です。 加えて繁忙期が終わると出荷が落ち着くため、先を見据えた在庫コントロールが大きな課題でした。
組織の壁
在庫管理とひとことに言っても様々な部門が関連します。 販売情報を握る営業部門、原料・資材の調達を握る部門、ものつくりを担う製造部門、そして実際の入出荷など荷動きを管理する物流部門。 在庫に関わる担当者が多いために責任の所在も不明確となり、結局、製造現場主導の生産計画になっていました。 効率を重視した製造により過剰在庫となり保管スペースがオーバーフローし、慌てて外部倉庫を契約することもありました。
生産計画作業の壁
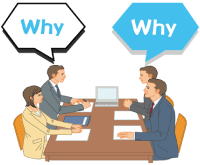
生産計画の立案は長らく専任のベテラン社員が担っていました。
前年の出荷動向、直近のトレンドを踏まえた生産計画を立てていきますが、当人しかわからない指標や長年の経験や勘をもとにした生産計画のため、数字の根拠がありませんでした。
また立案用のシステムは担当者固有のエクセルを使用しており、毎回最新の販売・在庫数値を入力するなどエクセルの作成自体にも時間がかかっていました。
取り組みテーマ
以上の課題を打破するため在庫改善プロジェクトが立ち上がりました。そしてその中心となった部門は物流部でした。
「在庫のリアルな荷動きを一番肌で感じているのは物流部である」という原点に立ち返った考え方です。
取り組みのテーマを以下の3つに絞り込みました。
- 1. 適正在庫を把握し、季節変動に動じない在庫指標を確立する
- 2. 在庫に一番身近な部門が、出荷と連動した生産計画を立案する
- 3. 生産計画の専門性を排除し、標準化・平準化・単純化された業務へ変革する
SLASHを活用した生産計画業務へ
業務の専門性を取り除くためにはシステムの活用が不可欠であるという結論に達し、複数社のパッケージソリューションを調査しました。 その過程において、統計学に基づき“根拠のある”安全在庫が算出されること、商品が持つ特異性を分析し可視化できること、 何よりも個別に複数存在したエクセルを集約できることが決め手となり、セイノー情報サービス(以下、SIS)のSLASHを採用しました。 決定の際には、実際の出荷データを用いた試解析結果と想定効果も判断材料としました。
需要トレンド分析と商品プロフィール
商品の季節性の高低、需要頻度の高低、最近の需要伸長度合などを数値化し、「要注意」商品をコンピュータが自動的に判定します。 加えて特有の要素(NB/PB、販売チャネル、生産の制約、イベント情報など)を病院のカルテのようにプロフィールで可視化し誰でも変化に気付けるようにしました。
発注点・安全在庫の自動算出
急激な季節需要に対応するため、特定期間の過去需要データを投入し、商品別の安全在庫・生産リードタイム期間の需要期待値を自動的に算出します。 この過程では弊社のコンサルタント、月桂冠様の物流部門、情報システム部門の有識者がトライ&エラーを幾度も繰り返し、試行錯誤しながら適切な分析日数や指数を決定しました。
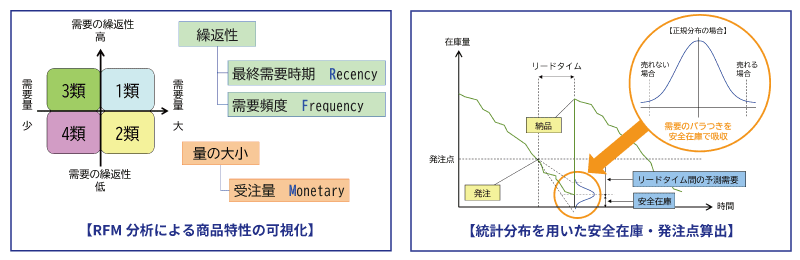
生産計画シートの自動作成と一元化
従来の生産計画は壜・パック・カップなどで各々の担当者がそれぞれのエクセルで計画を立案していました。 SLASHでは計画シートを統一化し、商品プロフィールに加え2ヵ月先までのPSI(生産・販売・在庫)情報を可視化しました。シートはボタン操作一つで生成され、時間短縮と属人性排除の効果も狙っています。
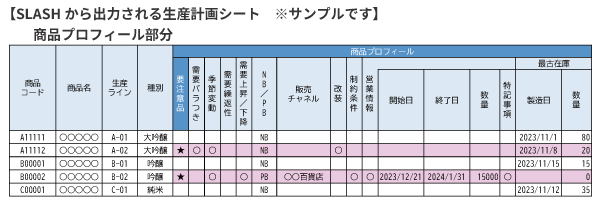
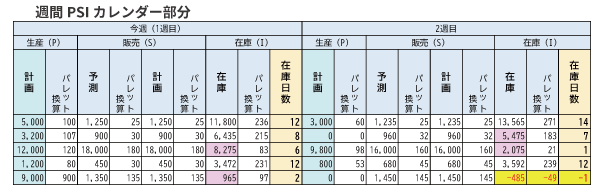
導入効果
システムを活用した業務運用の定着には時間がかかりますが、失敗を恐れない心の強さと粘り強さにより、下記の通り想定以上の効果を得られました。 ※システム導入の2年後に月桂冠様が試算
01 在庫の適正化
売上トップ10商品の平均在庫日数が約2日間改善
導入前:11.8日 ⇒ 導入後:10.0日
結果、商品鮮度の向上と物流センターの空スペースを確保-
02 欠品の抑制
欠品による売り上げ機会損失の抑制、品薄商品への事前の手当てが可能
導入前:年約40回の欠品 ⇒ 導入後:年4回に大幅改善 03 生産計画時間の短縮
生産計画シート作成に要する時間の短縮
導入前:1日4時間 ⇒ 導入後:約30分に短縮 約1/8へ改善
本来の計画業務に専念、加えて販売部門とのコミュニケーション時間を生成04 計画精度の向上
個別エクセルの全面排除により、休暇前の業務引継ぎ時間の短縮、簡略化を実現
計画業務未経験者でも、人事異動後の初月から生産計画の立案が可能05 情報の可視化と共有化
在庫指標の“単位”を全社的に「在庫日数」へ統一
更に社内システムに商品別の在庫日数ランキングを表示(在庫推移グラフも活用)
在庫に関する社内のコミュニケーションが活性化
今後の展望
以上の通り大きな効果を生み出した在庫プロジェクトですが、月桂冠様の活動はそれに留まりません。
本件は完成品(パック/カップ/壜詰など)が対象でしたが、今後は社内で管理される全ての在庫を対象範囲と考えています。
パック・カップや壜などの容器、キャップ・ラベル・包装紙などの資材に加え、原酒にいたるサプライチェーン在庫の適正化を視野に入れています。
そのためには物流部門という垣根を超え、調達・生産・物流・販売など関係する部門が同じ情報を共有し、変化に対してフレキシブルに次の一手が打てるプラットフォームの構築が必要とのことです。
創業から380年以上の歴史を誇る月桂冠様ですが、これから先も歩みを止めることなく進化し続けていきます。
お客様の声
月桂冠の物流部ではさまざまな指標(KPI)を設定して、日々業務の改善を進めています。
生産計画においては在庫日数という指標を軸に業務を進めますが、それをするにあたってはSLASHが中心的な役割を担ってくれています。
現在、全社視点での社内SCMの改善に取り組んでいます。SIS様にはこれからもSCM改善につながるご提案を期待しています。
物流部 部長
上村 太郎 氏
SLASHを導入してから約7年経過しましたが、導入前と比べるとコロナの影響を受けながらも出荷調整の回数、未出荷数量ともに大きな効果を発揮しています。
今後、調達・生産・物流・販売などのSCM業務を統合的に管理できる仕組みの構築を検討しております。
SIS様には持ち前の物流ノウハウと提案力でSCMプロジェクトの実現にご協力頂きたいと考えております。
物流部 物流課 主査
徳岡 志一 氏
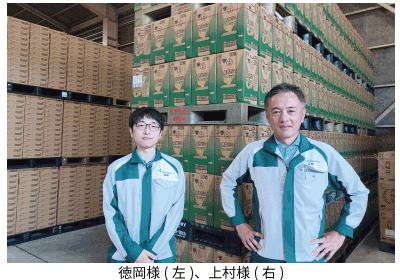
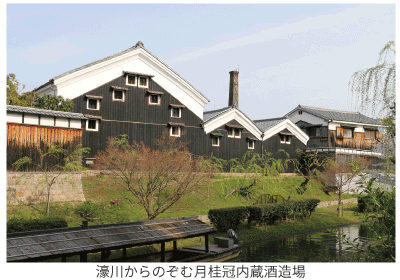