導入ソリューション
- 生産管理
-
-
- 企業名
- 調味料製造業
- カテゴリ
- 調達・生産管理
- 業種
- 食品 製造業
- 取扱商品
- 調味料
概要
調味料を中心として取り扱っている食品メーカーのA社様。業務用から家庭用まで様々な商品を豊富に取り揃えています。
-
課題
- ・正確な製造原価を把握したい
- ・食品トラブルの際に迅速に対応できるよう、トレーサビリティを確立したい
-
成果
- ・利益率アップ
- ・トレーサビリティ強化で、トレースフォワードは5分、バックは30分で可能
- ・全情報の可視化による業務改善の促進
課題
製造原価を下げて利益を上げたい
製造工程に潜むムダは、コスト増に直結します。ムダを特定するためには、製造に関わる全情報を取得しなければなりませんが、できていない状況でした。企業存続を考えれば、早期の改善活動が不可欠でした。 また、食品製造業にとって重要とされるトレーサビリティの強化にも取り組みたいと考えられていました。
課題解決方法
製造原価を把握するためには、材料費や労務費などの情報を、製造拠点単位で取得しなければなりません。しかし実際は、製造拠点によって違うはずの原価を一律で計算しているなど、正しい原価計算ができておらず、人手では限界がありシステムでの管理を決定されました。 トレーサビリティも同様で、どこから仕入れどこへ出荷したのか、全ての情報を商品ごとに記録しなければなりません。これまでは膨大な情報を手作業で記録していましたが、有事の際に入荷元や出荷先を調べるのにあまりに時間がかかってしまうため、こちらもシステム導入での解決を目指す事に決定されました。
物流ノウハウを活かした管理
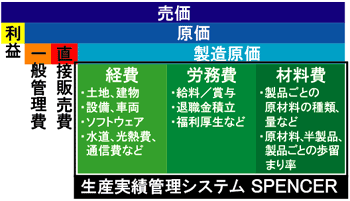
以前、経営方針を見直す際にコンサルティングをお手伝いさせていただいた弊社へご相談がありました。 そこで課題解決するための方法として、原価計算に必要な情報(材料費、半製品や製品の製造にかかる人件費などの労務費、設備維持費や光熱費などの経費)を製造拠点ごとに管理できる仕組みと、原価計算に欠かせない歩留まり率を計算する仕組みを兼ね備えた、生産実績管理システム SPENCERをご提案しました。 これによって、製造拠点や商品ごとに製造原価が把握でき、使用する原材料や作業工程の見直しや、原価改善などを意識した設備投資などの活動が、製造拠点ごとに行えるようになります。 トレーサビリティの確立は、物流ノウハウを応用し原材料にラベルを貼ることで、分量、賞味ロット、入荷日などを手入力からハンディターミナルによる入力に変えることで、正確な情報が簡単に取得できるようになります。これらは生産実績管理システムに用意されている機能のため、一つのシステムで全ての課題に対応できました。
- 生産実績管理システムで原価管理、トレーサビリティを確立
導入の効果
-
01利益率アップ
製造拠点ごと、商品ごとに製造原価が分かるようになり、効率の悪い拠点や商品などに対し対処できるようになりました。結果として製造コストを抑えられ、利益率がアップしました。
-
02トレーサビリティ強化
社内のトレースにかかる時間の目標として出荷先の特定は30分、入荷元の特定は2時間としていましたが、その数値を大幅に上回り、出荷先特定は5分、入荷元特定は30分(原因分析除く)を達成できました。
-
03全情報の可視化による業務改善の促進
生産に関する全情報が把握できるようになり、業務改善の活動指針になりました。それによって、在庫削減の活動も進み20%削減できました。