こんにちは。WMS:倉庫管理システム「SLIMS(スリムス)」を提供するセイノー情報サービスです。
物流現場に潜む課題を見つけられれば、改善余地を大きく広げられる可能性があります。
当コラムではそれがどのような特徴を持つ課題なのか、どうやって見つけるのかご紹介します。
「色々と改善に取り組んできて、やるべき(やれる)事が無くなってきた」と言う方はぜひ参考にしてください。
目次
コラムのポイント
- ・現場作業をテーマとした改善活動の目的と取組み例
- ・見えていない課題を見つけるコツ
- ・「見つけて改善」できた事例
物流現場における改善活動とは
どの物流現場でも、何らかの改善活動が行われています。
多くの現場が活動の目標値としてKPI(物流評価指標)を設定し、達成するために日々PDCAサイクルを回しているのではないでしょうか。企業によってはチームごとに改善活動に取り組み、報告会で成果を発表する制度が導入されていたりもします。
物流現場のKPIの種類や設定方法はこちら
改善活動の目的
物流現場における改善活動の目的は2つに大別できます。
コスト削減
1つ目は物流コストを削減することです。
特に人件費や倉庫料、輸送費など「支払物流費」の削減が期待されています。社外への支出を減らして手元に残るお金を増やす、つまり多くの利益を生み出すことで、設備増強や研究開発、物流現場へのロボット導入が可能になります。これらは企業が成長するために必要な投資です。
最近は労働力不足によって人件費や輸送費が高騰しています。利益の増大に直結するコスト削減は、今後より強く求められるでしょう。
物流品質の向上
2つ目は顧客サービスとしての「物流品質の向上」です。
物流は「顧客との接点」の1つです。商品や個数を間違えず正しく出荷することはもちろん、納品リードタイムの厳守・短縮やJIT納品への対応など、物流品質をより良くすることで信頼性や顧客満足度が向上します。それが顧客の囲い込みにつながって取引の維持拡大、つまり売上増大に貢献できます。
物流現場でよくある課題
物流現場が主導して取り組める課題にはどのようなものがあるでしょうか。
活動例を目的別に紹介します。
活動目的 | 得たい効果 | 課題 |
---|---|---|
コスト削減 | 効率化 | ・各種業務の多能工化 ・作業者の円滑なシフト体制 ・新人が直ぐに確実に出来る業務体制 ・入荷、格納、ピッキング、検品、梱包、 返品業務工数の低減 |
省スペース化 | ・棚の省スペース ・一時仮置きスペースの削減 ・デッド品、過剰在庫品の整理整頓 ・クイックチェンジ(新作、季節品等) | |
資材コストの削減 | ・消耗品の削減 ・必要機能を満たす梱包資材費の低減 | |
物流品質の向上 (売上の増大) |
信頼性の向上 | ・誤出荷ゼロ ・出荷遅延ゼロ ・流通加工ミスゼロ ・棚卸差異ゼロ ・商品の破損ゼロ |
リードタイム削減 (顧客満足度の向上) |
・スルー品の拡大 ・帳票作成時間の短縮 ・工程間の商品の滞留低減 ・返品処理のクイック対応 ・緊急品出荷のクイック対応 ・入出荷計上、報告スピードアップ |
「どの改善に取り組むべきか」は、企業(物流部)として「コストと品質、どちらを重視しているのか」から考えてみるのも1つです。
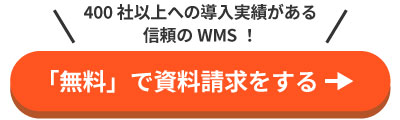
物流現場の見えている課題、見えていない課題、つくる課題
物流現場の課題は3タイプに分けられます。
それぞれにあった取組みを行うことで、より確実に改善できます。
- ・見えている課題:作業者も現場管理者も認識している課題
- ・見えていない課題:気づいていないが実は起こっている課題
- ・つくる課題:企業が成長するためには乗り越えなければならない課題
見えている課題
「見えている課題」はすでに問題が起こっており、作業者も現場管理者もそのことを知っています。
見えている分、3つのタイプの中では比較的「解決」に近いと言えます。せっかく「見えている」のですから、積極的に取り組んで改善していきましょう。
見えている課題(一例)
- ・誤出荷(数量・品名)、誤破損などのクレーム
- ・届け先への商品未着や指定期日遅れ
- ・取扱量、アイテム数増加によるスペース不足
- ・長時間残業
- ・業務の属人化
- ・同梱、個装依頼への対応に手間がかかっている
- ・リサイクル、廃棄問題
- ・人手不足(特に繁忙期)
見えていない課題
物流現場では全ての課題が「見えている」わけではありません。
気づいていなだけで、実は重大な課題が隠れていることもあるため、放っておくのは危険です。例えば利益改善に取り組むある企業は、顧客ごと・担当営業ごとに物流コストを算出しています。コストが上回ってしまっている顧客については、営業部に情報共有し、改善を図るようにしました。売上が高い顧客を「お得意様」として手厚く対応するのは悪い事ではありませんが、コストも意識する必要がある、という事例です。
また改善が進んで数値が向上しづらくなってきた生産性をより向上させるためには、見えていない課題(改善余地)を探して改善しましょう。
つくる課題
企業がビジネスを続けていると市場の動向など「外部環境の変化」や、経営戦略や営業戦略といった「内部の変化」に対応するべく乗り越えなければならない壁が出てきます。そういった今後課題になりそうなことを「つくる課題」と呼びます。企業自らがその壁を「課題」と認識し立ち向かうことを決めて取り組むため、「つくる」と表現されます。
この課題に物流現場だけで取り組むことはありません。経営層や本社物流部門によって戦略・対応方針が立てられ、それに沿って活動が進められます。例えば将来の人材不足に備えてのロボット活用や、ドライバーの不足に備えて競合他社との共同配送を推進する活動が該当します。
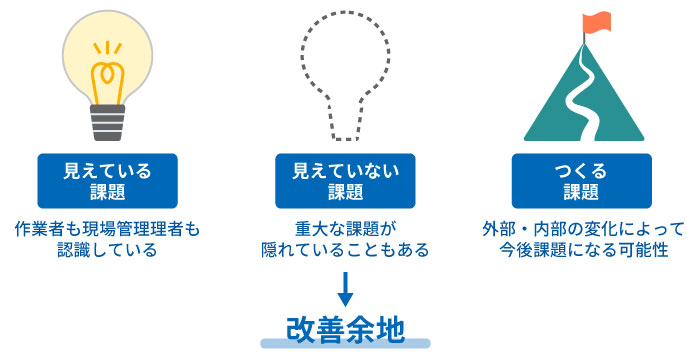
物流現場の「見えていない課題」を見つける方法
物流現場における「見えていない課題(改善余地)」を見つける方法を3つご紹介します。
データ分析で課題を見つける方法
WMS(倉庫管理システム)をはじめ情報システムに蓄積されている作業時間や生産性実績など、データから課題を見つける方法です。
データの見方・使い方のコツをご紹介します。まず、データは実績値だけで見るのではなく「理想値」と比較しましょう。理想の数値は、その工程にかけられる時間・人数から算出できます。
しかしデータは膨大で、過去データ全てを対象にしていると中々進みません。
そこで問題がありそうな日を絞り込んで調べるのです。
例えば生産性。当社が調査を依頼された現場で、「平均値」を下回った日だけを抽出しました。すると物量が多く「忙しい」と感じた日よりも、物量が少なく余裕を感じた日の生産性に低下傾向が見られました。そこで物量に合わせた要員配置を変更し、あえて「少し忙しい」状態にして、生産性を向上させました。
400社への導入実績を持つ倉庫管理システム「SLIMS」の詳細はこちら
生産性向上を支援するソリューション「FLabor」の詳細はこちら
業務フローを整理して課題を見つける方法
いま行っている作業を改めて業務フローに起こしてみることで見つけられる課題もあります。
日本の物流現場は非常に優秀で、顧客や営業部門の様々な要望をできるだけ叶えようと努力してきました。その結果、「顧客ごとの個別対応」が増えるなど作業が煩雑になり、当初の想定には無い業務が増えてしまうこともあります。
そこで業務フローを整理しなおしてみるのです。
そこから作業の重複や戻り、煩雑な緊急対応、チェック業務のための滞留などが見つかったら、標準化・定型化しましょう。ちょっとした手間だからと見逃さず、本当に必要かを客観的に考えてみるのが整理のコツです。
現場を見て課題を見つける方法
うまくまわっているように思える現場でも、着眼点を変えると改善余地を見つけられることがあります。
よくあるのは、作業上のムダやロスを探すことです。
歩く、探すといった作業をもっと減らせないか、オーダー処理や伝票・ラベル発行を待つようなロスを無くせないか、報告や相談のために作業中断が入っていないかなど、チェックしたい行動をリスト化してセンター内を見てみましょう。
この時のコツは、現場全体を見るのではなく、1つの作業に集中して細かく観察してみることです。
そうすると「なぜあの動きを?」というような何気なくやっているムダを見つけられます。
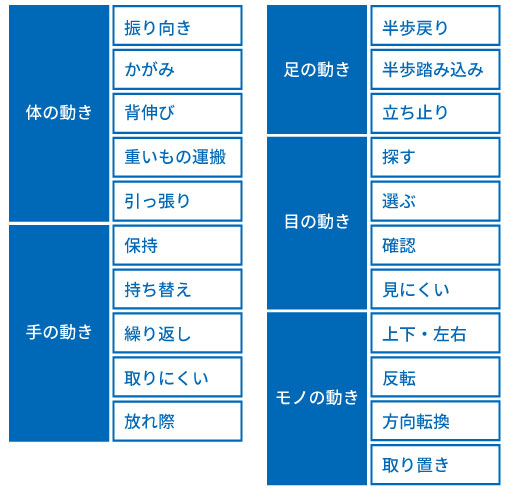
まとめ
物流現場に潜む課題を見つけられれば、改善余地を大きく広げられる可能性があります。
隠れていて見えていない課題は、データ分析・業務フローの整理・現場観察で見つけられます。
「色々と改善に取り組んできて、やるべき(やれる)事が無くなってきた」という方はぜひ「見えていない課題」にチャレンジしてください。
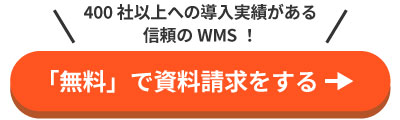
このコラムの監修者![]() |
セイノー情報サービスは400社以上へのWMS導入を通して培った物流ノウハウをもとに、お客様の戦略立案や物流改善をご支援しています。 当コラムは、経験豊富なコンサルタントやロジスティクス経営士・物流技術管理士などの資格を持った社員が監修しています。 |
---|