物流現場で最も作業コストがかかっている業務は出荷です。出荷作業には「ピッキング」、「検品」、「梱包」の各工程がありますが、最も無駄が発生しやすいのが「ピッキング」です。ピッキングには 探す、歩く、確認する、数える、手に取る、置く など多くの動作があり、人に依存した作業が大半です。システム化を推進している物流現場においても、ピッキングはこのような作業が多いことがコストがかかる理由となっています。 では、どのようにしてピッキングのにかかるコストを減らせばよいのでしょうか。 ※ここでは、ロケーション管理(商品の所在管理) が実現されており、「探す」行為が発生しない物流現場でのピッキングを想定対象としています。
ピッキング時の移動を減らす方法とは?
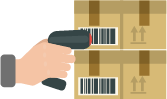
ピッキング作業の中で最も時間がかかるのが移動です。移動距離を短くする対策として、ピッキングリストの並び順の改善をよく見かけます。これによりコストを削減できることもありますが、実はその前にやるべき大きな改善があります。それは、多種多様な商品を「どう配置しどう保管するか、それによって移動距離を短くする」という改善です。 ここで、物流現場に限らず、改善活動の基本的な考え方であるECRSを紹介します。 ECRSとは「Eliminate(排除)」「Combine(結合)」「Rearrange(交換/変更)」「Simplify(簡素化/単純化)」の略で、改善活動をより効率的・効果的に進めていく手法です。具体的には、以下のような内容です。
E:無くせないか?
C:順序を変更し効率化できないか?
R:別の業務と一緒にできないか?
S:簡素化・単純化できないか?
では、このECRSの考え方をピッキング作業の移動に当てはめてみましょう。
そうすると、「作業者を最短距離で移動させる」のではなく、「作業者の移動そのものを出来る限り無くす」ことを考える必要があることに気づけるのではないでしょうか?
商品の配置の最適化し、コストを削減しよう
ムダな移動を無くすために、2つの観点から商品の配置を考えてみます。
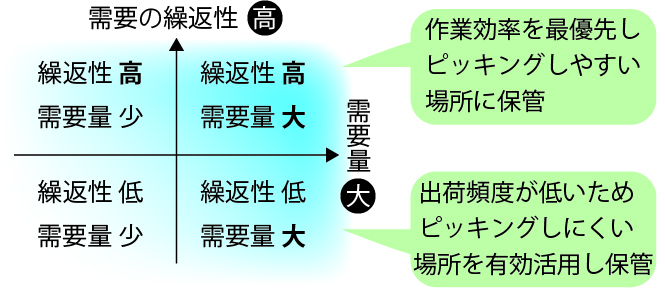
① 出荷頻度に応じた商品配置
出荷頻度の高い商品は倉庫の手前やメイン通路から近い場所に、出荷頻度の低い商品は倉庫の奥に配置します。つまり、商品の出荷頻度に合わせて商品の保管場所を考えるのです。② 商品の関連性を意識した商品配置
また、商品の配置を変更する際に1つ注意点しなければならない点があります。
それは、各商品の特性(重量・サイズ・荷扱い条件)を考慮することです。例えば、小さな商品や取扱いがデリケートな商品をピッキングした後、大きな商品や重量物をピッキングするのは順序が良いとは言えません。荷崩れや重量による破損を避けるために、先にピッキングした商品をカゴから取り出す必要があります。そのため、重量物や大きな商品から最初にピッキングできるように配置したり、取扱いに注意すべき商品は最後にピッキングできるように配置することも作業効率に大きな影響があります。
ピッキング作業のコスト改善は>商品配置の見直しで改善
コスト改善に取り組む場合や生産性を上げたい場合は「なぜここに保管されているのか?それは効率的なのか?」というように、自社の物流現場が効率を意識した商品配置になっているか、今一度見直してみることをお勧めします。
次回は、出荷作業における残業者をゼロにする改善策についてお話しします。
当社の倉庫管理システム の詳細はこちら