今回のコラムは、「物量の変動」を「敵=勝つ対象」としてスタートしたいと思います。物量は、季節、月間、曜日、日々、もっと言えば、1日のうちでも時間ごとに変動します。図1は、物量の変動の例として、あるメーカーの日々の物量(出荷明細数)を1年間に渡って示したものです。
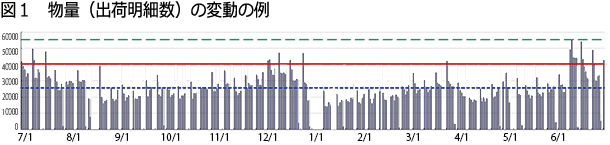
物量の変動と人時生産性を可視化する
物流現場における人時生産性(作業員1人の1時間あたりの生産能力)を高める必要があることに異論はないと思います。また、人時生産性は、物量が多ければ高くなり、少なければ低くなることは、皆さんがすでに気づいていること、体験していることです。
各業種において、この図1で示したような日々の物量の変動に対する物流現場の人時生産性は、どうなっているのでしょうか。
図2~4は、変動する物量に対するピッキング工程の人時生産性の実例です。
これらは、当社の人時生産性改善ソリューション「FLabor(フレイバー)」を用いて、作業時間と人時生産性を可視化しています。
「日別の作業量」と「日別の人時生産性」の変動に注目してください。
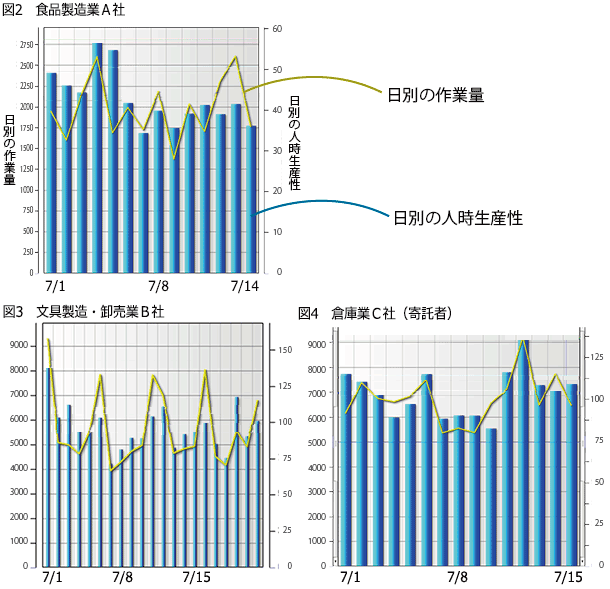
いずれも、人時生産性は、物量が多ければ高くなり、少なければ低くなっています。先に述べた「皆さんがすでに気づいていること、体験していること」を裏付けた(可視化した)ことになります。
改善の余地を把握する
つぎに、改善余地を見てみましょう。図2から4では、青・赤・緑の線を引いています。
青は調査対象期間中の日別人時生産性の平均値を、緑は同じく人時生産性の最高値を示しています。また、赤は調査対象期間中の日別人時生産性の平均値を超えたデータのみの平均値を示しています。
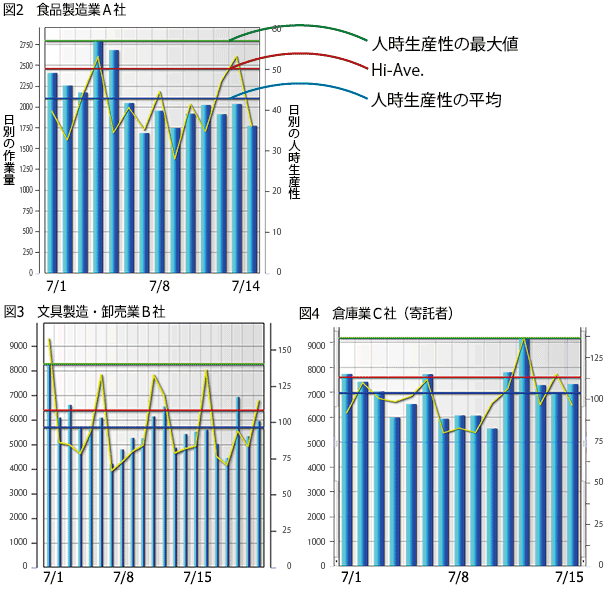
セイノー情報サービスでは、この赤い線を「Hi-AVE値(ハイ・アベレージ値)」と称して、当面の目標値として推奨しています。人時生産性が高まれば、Hi-AVE値も上昇し、次の改善目標値になります。これで、目標の人時生産性と今の人時生産性のギャップが改善余地として可視化・把握できました。
作業員コントロールでコスト削減に貢献する
物流現場におけるコスト削減を実現するためのアプローチには、「作業員コントロール」と「作業工程効率化」があります(図5)。
まず、「作業員コントロール」は、いかに生産性を高くかつ平準化するかという視点で、人時生産性の可視化を行い、労働契約を見直し、作業進捗管理のリアルタイム化を行います。
一方、「作業工程効率化」は、いかに作業手順を効率化するかという視点で工程効率の見える化を行い、作業動線の変更、システム化を行います。
これらはいずれも、作業コスト(変動費)の削減に貢献します。改善に必要な能力として、作業員コントロールには、運営力や気遣いが、作業工程効率化には、企画力や気付きが必要です。このうち、作業員コントロールは、作業工程効率化と比べて、深い改善知識と分析作業時間が不要であり、すばやい改善が可能です。
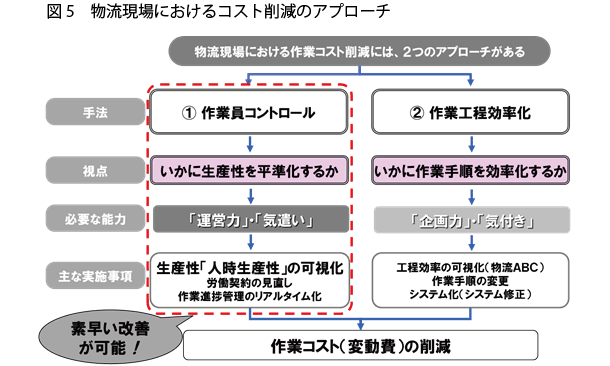
今回は、物流現場における物量の変動と人時生産性の可視化について述べました。次回以降は、本社物流部門、物流現場、労務管理者の改善ニーズに立ち戻って、整理していきます。