今回は、これまでにコラムで何度も登場しましたFLabor(フレイバー)の活用法に関するトピックを紹介します。
仕事柄、お客様から「うちの物流コストは、競合他社に比べて高いか低いか知りたい」という質問を受けます。企業間競争をしている以上、競争優位となるための当面のゴールを知り、目標値を設定して、その達成に向けて取り組むことが重要であることは確かですので、外に目を向けるのも分かります。
私は、このような質問を受けた時、きちんと比較できる情報が公開されている場合は、「お気持ちはよくわかるのですが、物流コストの範囲や基準が企業によって異なるので、無理に比較せず、参考程度としてください」として、調査情報の提供に応じています。
その後に「ところで、内に目を向ける必要はありませんか?」と、その実情をお聞きすることにしています。
意外? 各物流拠点でバラバラな評価指標を見直す
全国に複数の物流拠点を設置して、事業運営している企業は多いわけですが、ここでは、北海道から九州まで全国に5つの物流拠点を構え、事業運営している消費財卸売業A社様を取り上げ、物流拠点における作業生産性向上の取り組みを紹介します。
5つの物流拠点は、同じ商品を取り扱い、それぞれ担当する地域の配送拠点になっています。インタビューでは、各物流拠点でさまざまな改善を行っていると聞きましたが、作業日報は手書きであり、その情報を本社がすぐに把握できない状態でした。加えて、各物流拠点の評価指標は、統一されていないという事実も判明しました。
<図表1 統一されていない物流評価指標>
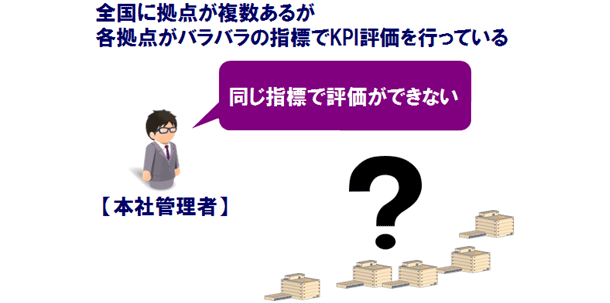
各物流拠点の作業生産性を本社で一元的に把握する
そこで、各物流拠点の作業生産性を、同じ指標で「可視化」、同じ運用で「要員計画、要員調整」、「本社物流部門の評価結果(改善効果)を一元的に把握」するため、FLaborを活用することにしました。
まずは、FLaborのレポーティングサービスを活用します。それにより、同じ作業の生産性を北海道支店と九州支店で比較し、生産性が高い支店の手順を他支店に横展開したり、生産性が悪くなっている要因を調べるなど、改善活動につなげます。
また、以前は作業生産性を把握するため、手書きの作業日報を各物流拠点でパソコンに入力し、本社に送信していたため、1ヶ月前後のブランクが生じ、作業生産性をリアルタイムに把握できませんでした。
今では、作業生産性をリアルタイムに把握できるため、物流現場の「いま」を知り、改善が早く進むようになっています。
<図表2 各物流拠点の生産性を共通指標で把握>
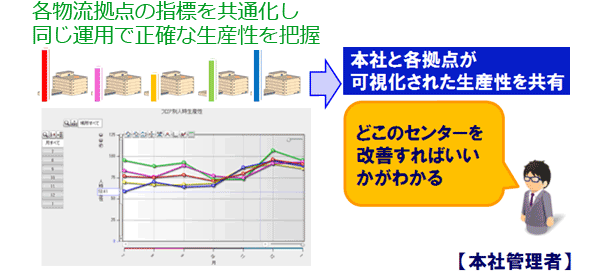
A社様では、さらに個人別の作業生産性を把握し、改善に結び付ける活動に取り組んでいます。個人別の作業実績情報をFLaborに取込み、個人毎の作業生産性を可視化しています。
感覚的な作業アサインメントから脱却し、計画を自動化する
要員計画は、作業単位ごとの目標値に基づきますが、すでに可視化されている個人別の作業生産性があれば、「人数」だけでなく、「能力」のファクターも取り入れた精度の高い要員計画が行えます。
さらに、作業者に対し、個人ベースで計画した正確な勤務計画表が出せます。これにより、「今日終わらなかったから明日出勤してください」といった、感覚的なアサインをなくせます。
<図表3 要員計画の適正化>
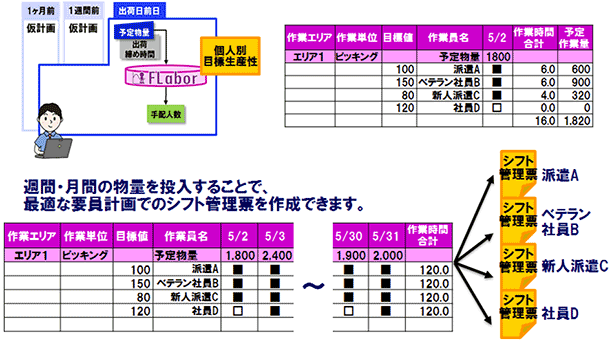
また、この計画表を紙やメールでアウトプット出来るようにすれば、予定表の簡素化や通知の自動化が実現できます。